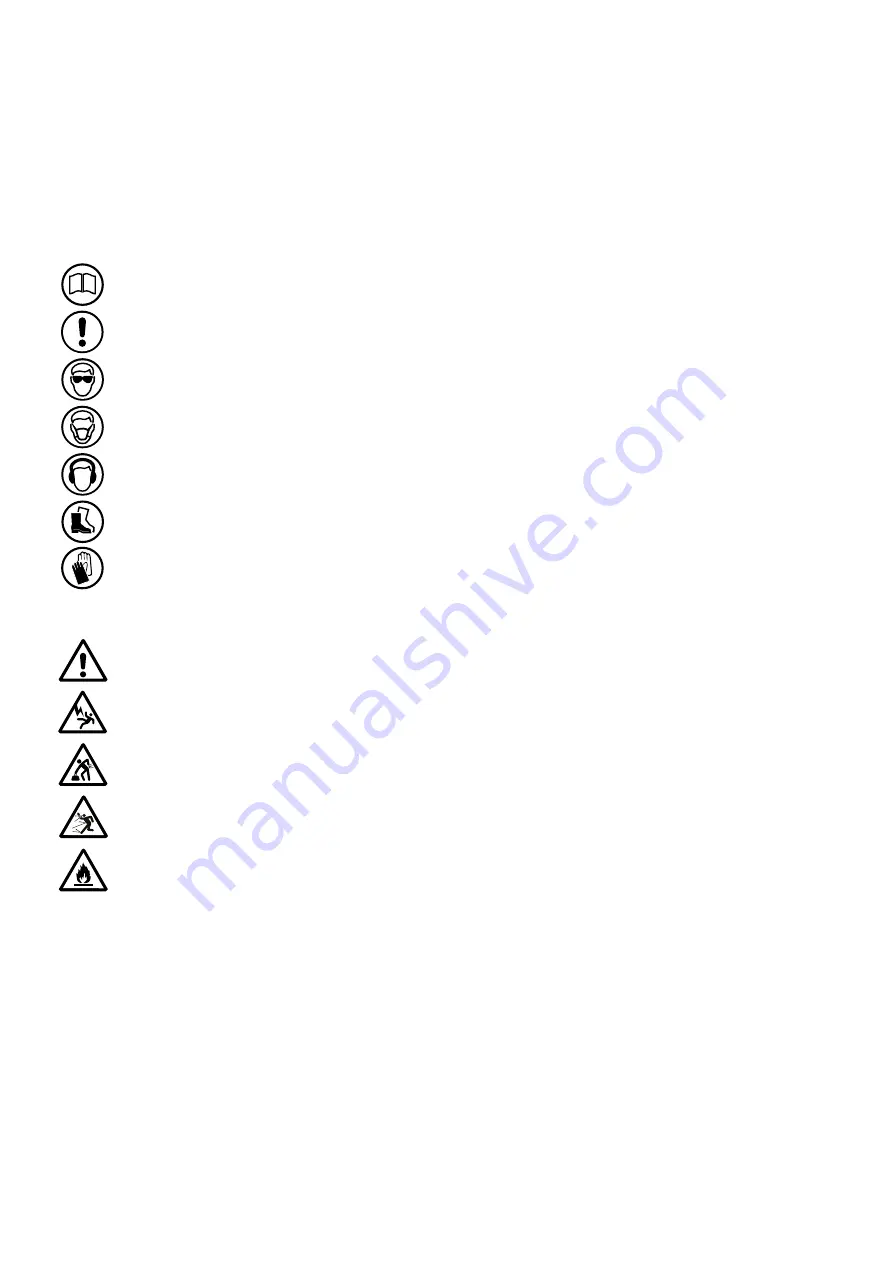
3
Part Description
Part Number
THE SYMBOLS AND THEIR MEANINGS SHOWN BELOW MAY BE USED THROUGHOUT THIS MANUAL. PLEASE ENSURE THAT YOU
TAKE THE APPROPRIATE ACTION WHEREVER THE WARNINGS ARE USED.
Explanation of Symbols
i
Kg
i
Kg
i
Kg
i
Kg
i
Kg
i
Kg
i
Kg
i
Kg
Mandatory
Instructions
Warning
Read and fully understand the instruction manual
before attempting to use the machine.
Indicates an instruction that requires particular attention
Wear protective eyewear
Use respiratory protective equipment
Use suitable protective footwear
Use hearing protection
Use protective work gloves
Indicates a risk of severe personal injury or
damage to the machine
Indicates a risk of severe personal injury
from electrical shock
Risk of personal injury from lifting of heavy items
Indicates a risk of severe personal injury from
airborne objects
Risk of fire
i
Kg
i
Kg
i
Kg
i
Kg
Summary of Contents for TS250C
Page 28: ...28 11 Parts Lists Diagrams ...
Page 29: ...29 11 Parts Lists Diagrams cont ...
Page 30: ...30 11 Parts Lists Diagrams cont ...