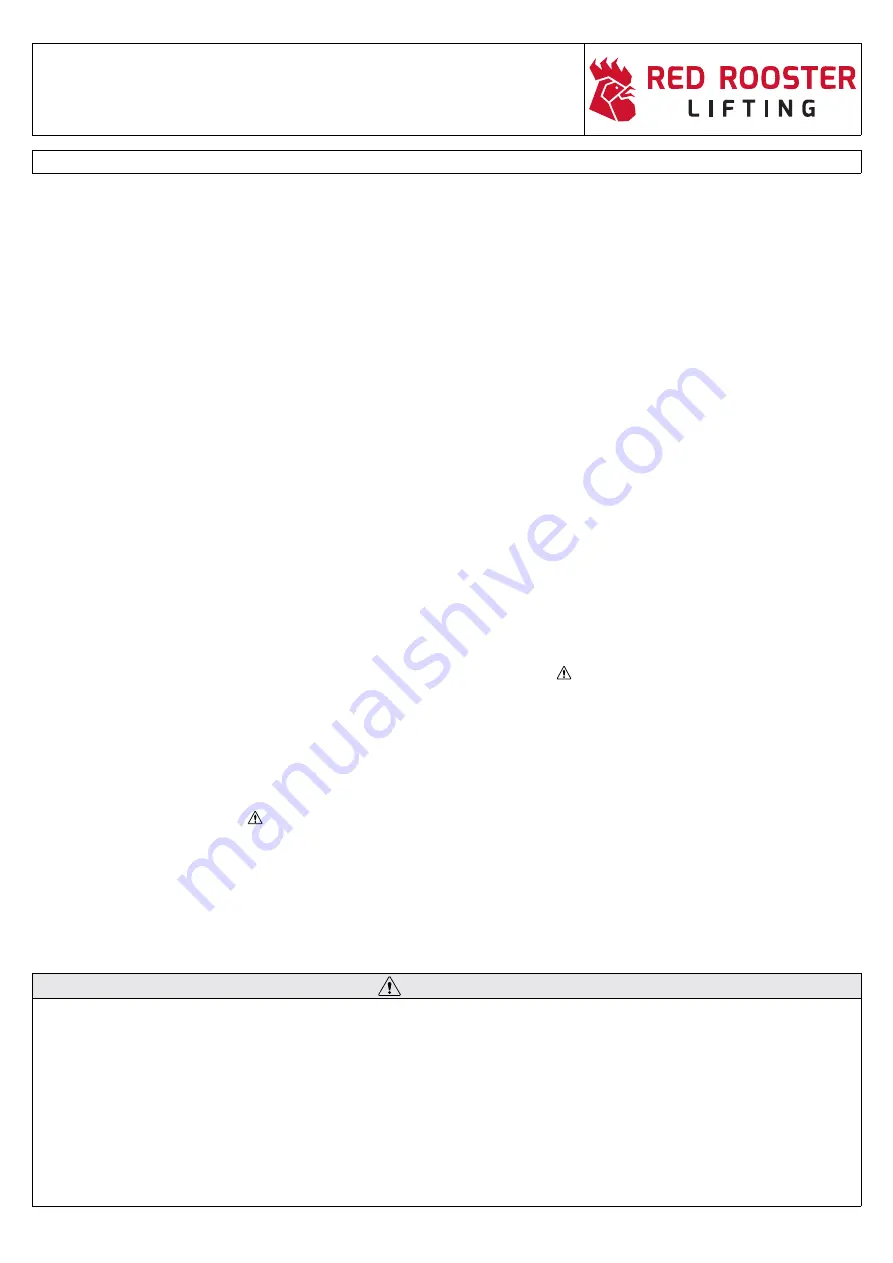
7
USER MANUAL
▪
Red Rooster Lifting Limited
▪
Nauta House, The Meadows, Oldmeldrum, Aberdeenshire, AB51 0EZ
▪
Tel: +44 (0) 1651 872101
▪
M01-AH27 REV2
GETTING STARTED - CHECKS BEFORE USE & HOSE SUPPORT BRACKET
1.3
CHECKS BEFORE USE
These checks should be carried out during installation and on a frequent and regular basis thereafter. If the hoist is used daily then it is
recommended that they are carried out daily as the checks take only minutes to complete and not only help avoid repair bills but significantly
reduce the possibility of an accident or dangerous occurrence. Thoroughly examine the equipment prior to installation to ensure that no
damage has occurred during transit. Hoists and trolleys should not be altered in any way without contacting Red Rooster for clearance, as this
may affect the certification of the unit.
AIR SUPPLY CHECKS:
▪
Inlet pressure: 5 to 6 bar (there will be pressure losses across the air set and on long hoses) The supply pressure should not
exceed 7 bar as this may affect the load limiter.
▪
Air flow: Check air flow requirement and minimum hose diameter also check that small bore fittings are not strangling the air flow.
▪
Keep the lubricator topped up with a light turbine oil (ISOVG3256).
▪
The filter should be checked regularly and manual units drained of water as required.
▪
THE AIR HOSE SHOULD BE SUPPORTED SO THAT THE WEIGHT OF HOSE IS NOT HANGING FROM THE AIR SET AND
`FITTINGS. THE AIR SET IS NOT DESIGNED TO SUPPORT THE WEIGHT OF THE HOSE. SEE PAGES 7 AND 12 IF A HOSE
SUPPORT BRACKET AND MANIFOLD IS FITTED TO THE HOIST.
▪
The air supply should be clean and relatively dry. Where the compressor produces a lot of water action should be taken to remove
the excess water.
▪
Check air connection size and type are compatible.
▪
Check security of air hose connection.
AIR SUPPLY CONNECTION:
Every installation is different, so the correct method of supporting the air hose should be reviewed while installing the hoist. This needs to
take into account the weight and size of the hose, obstructions both at deck and hoist level, connections, operating conditions and any likely
movement of the hoist and air hose.
The fittings and filter lubricator are not designed to take the weight of the hose.
If the air supply hose length is over 10 metres the hose ID should be increased to the next size.
AIR SUPPLY:
Vane type air motors are designed to function using clean, dry, lubricated air. The installation of an ‘in line’ air service unit although essential
cannot in itself compensate for serious contamination in the air supply. When operating the compressor in moist (humid) or dusty atmospheres
seek the advice of your compressor supplier with regard to the fitting of a dryer and filter.
AIR PRESSURE:
The hoist is designed to operate best in the pressure range of 5 to 6 bar (72 to 90 p.s.i). The speeds quoted on the manufacturer’s literature
are obtainable only at 6 bar (90 p.s.i) inlet pressure. The hoist will operate at much reduced speed at pressures below this figure.
AIR FLOW:
Refer to the hoist data sheet, to select the hose diameter which ensures adequate air flow. Failure to provide adequate airflow will result in a
pressure drop in the supply line and cause the hoist to stall and the brake to apply until the pressure increases. In addition, the brake will not
release cleanly and will overheat. (Although not in itself a hazard [the brake fails safe] it may prove frustrating to the operator and a hazard
may arise as a consequence.)
HOSE SUPPORT BRACKET:
Where a hose support bracket and manifold have been fitted to the hoist to take the weight of an air supply hose, several checks must be done.
▪
Check the hose hangs freely and does not interfere with the hoist chain.
▪
Check the hose is clear of the load to be lifted.
▪
Check the pendant hose is not obstructed by the air supply hose.
▪
Check the air hose is supported by the hose clamp / former / festoon system.
▪
DO use exclusively correctly rated and certified pneumatic hoses and fittings in the air supply line.
▪
DO support the air line up to the hoist, as the fitting and filter / lubricator are not designed to take a load and may not support the
weight of the hose.
▪
DO maintain the internal diameter (as per the table throughout the supply length) or reduce from the larger diameter to the
smaller diameter in the direction of the hoist.
▪
DON’T use hydraulic fittings. These often have a reduced orifice size resulting in a down line drop in air pressure.
▪
DON’T increase from smaller to larger diameter or insert a length of smaller diameter hose in the supply line as this will result in
reduced flow and pressure.
▪
DON’T create low points in the air supply line where water may be trapped (or if unavoidable install a drain tap).
▪
DON’T rely on pneumatic fittings to support airlines; they are not designed for this purpose.
▪
DON’T shorten the pendant by forming a loop or a coil. This will prevent the strainer wire from supporting the pendant and will
cause the hoses to become detached or kinked.
CAUTION
CAUTION
CAUTION
CAUTION
DANGER