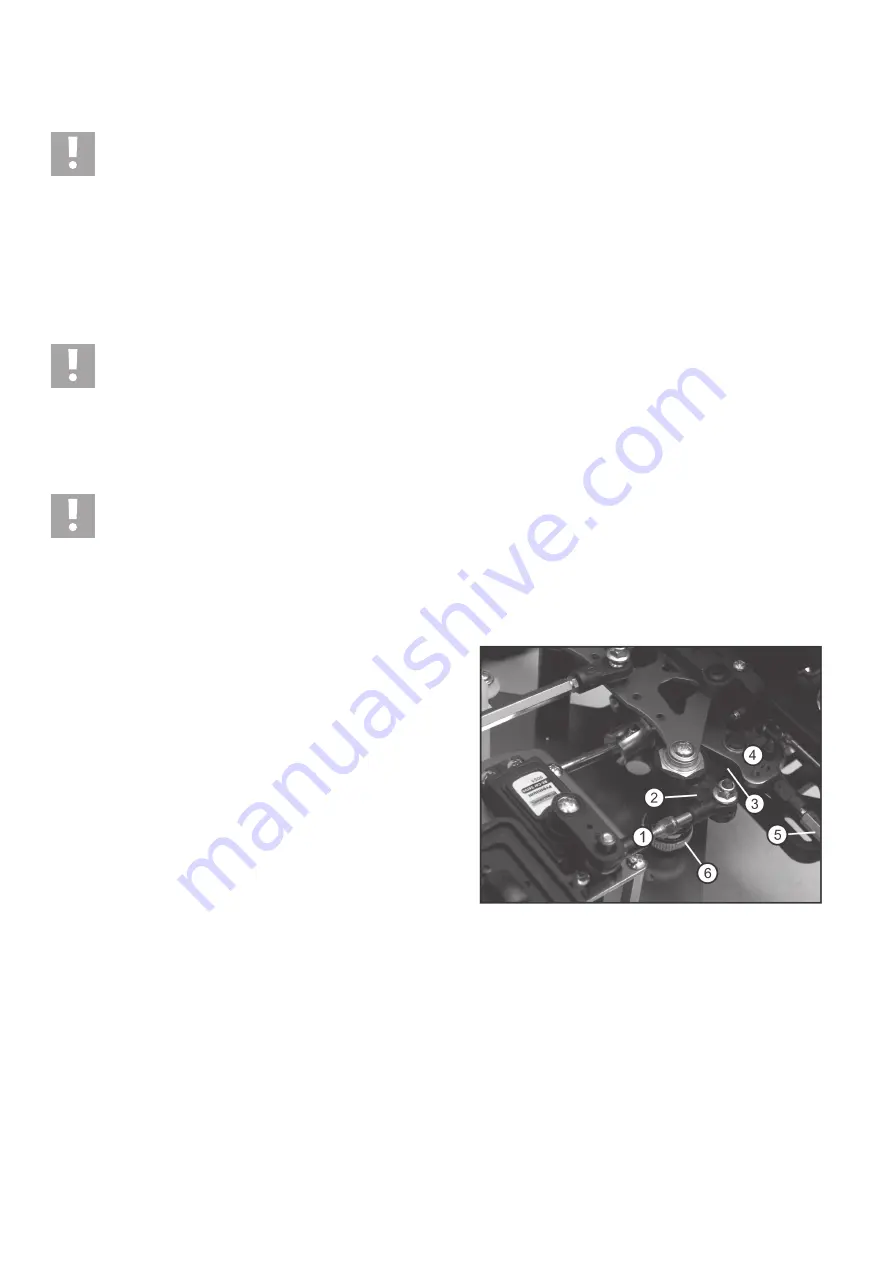
35
e) Fail-Safe Module (optional)
To control the vehicle when reception is poor or the receiver battery is low, the model should be equipped with a fail-safe module. The fail-safe module controls
the throttle/break servo; it is installed between the receiver and throttle servo. The module is then placed in the RC box.
In programmable remote controls, a failsafe function is often already integrated. Check the operating instructions of the included remote control
before purchasing a failsafe module to find out if failsafe is possible. If so, this function should also be activated.
Before first use, this failsafe has to be programmed to the right position of the throttle/brake servo.
The programmed failsafe position must ensure that to engine is throttled back and the brake is activated.
f) Checking the Range of the Remote Control Transmitter
In order not to lose control over you model you should, before each first start or after a crash, check the function and range of the RC system. For the range test,
it is sufficient to check the steering servo function.
Due to the good traction of the wheels and the weight of the vehicle, the wheels - in contrast to driving operation - would not follow your steering commands
spontaneously and directly while still on the floor. Therefore, support the model at the front axle in a way that allows the wheels to hang freely.
Only perform the range test without the combustion engine running!
• Move approx. 50 m away from the model.
• Move the steering wheel (channel 1) to the right. Now the wheels must turn towards the right!
• Move the steering wheel to the left. Now the wheels must turn towards the left!
• Release the lever of the remote control. The wheels must return to the straight position.
Never drive the model with a defective remote control!
If the remote control does not function properly, first check the charge status of the transmitter and receiver batteries and make sure that nobody uses the same
frequency as you do.
g) Servo Function Check
Steering servo
The steering servo is connected to channel 1 of the remote control transmitter, the
steering wheel.
Steering Setup
The steering of the vehicle is designed as an axle leg steering.
At the same time the steering knuckle arms are connected with the three-part steering
link. The pivoting movement of the servo control lever has an effect on the steering
linkage (1) and on one arm of the servo saver (2).
The servo saver comprises two rectangular levers that are more or less firmly connected
(pressed together) by adjustable spring force. If the press-on pressure of the spring is
increased, the steering commands are performed more precisely when standing and
when driving. Disadvantage: Impacts from the steering geometry are transmitted to
the servo gear “harder”.
The second steering lever of the servo saver (3) steers the centre part of the steering
link, the steering plate (4), and in this way causes the wheels to turn via the steering
link (5).
When hard impacts are transmitted through the steering link during operation, they are not immediately transmitted to the steering servo, but are absorbed with
the help of the resilient connection of the two steering levers of the servo saver.
The servo saver effect can be set with a knurled nut (6). If the press-on pressure of the spring on the two steering levers is increased by twisting the knurled nut
accordingly, the two steering levers of the servo saver are pressed together more strongly. This will reduce the protective function for the servo and increase
control precision.
Turning right and left is limited by a mechanical stop of the steering knuckle arm against the axle leg support.
Figure 5
Summary of Contents for 27 51 16
Page 102: ...102 ...
Page 103: ...103 ...