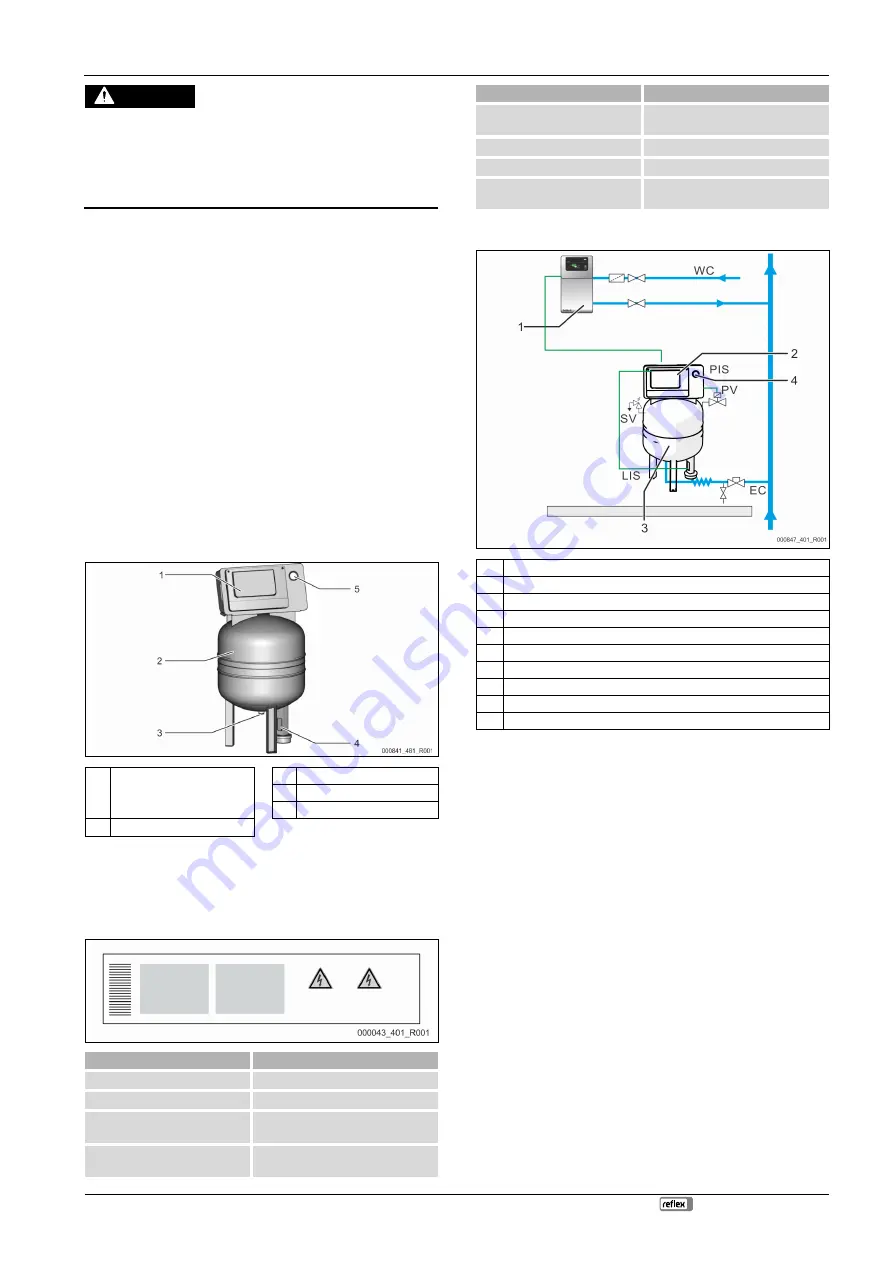
Description of the device
Reflexomat XS — 02.16.2022 - Rev. A
English — 17
CAUTION
Risk of injury due to pressurised liquid
If installation, removal or maintenance work is not carried out correctly, there
is a risk of burns and other injuries at the connection points, if pressurised
hot water or hot steam suddenly escapes.
•
Ensure proper installation, removal or maintenance work.
•
Ensure that the system is de-pressurised before performing installation,
removal or maintenance work at the connection points.
Note!
When installing the on-site safety valve, the operator must ensure that
there is no danger during blow-off.
Note!
Equipment parts with a safety function in respect of water-side
pressure limiting according to the Pressure Equipment Directive
2014/68/EU and temperature limiting according to the Pressure
Equipment Directive 2014/68/EU are not supplied.
The operator is responsible for on-site provision of water-side pressure
and temperature protection.
4
Description of the device
4.1
Description
The Reflexomat XS is a mini-compressor system. The main usage areas are
heating and cooling circuits.
•
An expansion vessel of 80 l nominal volume
•
The control unit is factory-installed on the expansion vessel.
•
All electric and air connections between control unit and primary vessel are
pre-installed.
4.2
Overview
1
Control unit
•
Compressor
•
Controller
3
Expansion line "EC"
4
Weight measuring cell "LIS"
5
Pressure gauge
2
"RG" primary vessel
4.3
Identification
4.3.1
Nameplate
The nameplate provides information about the manufacturer, the year of
manufacture, the manufacturing number and the technical data.
Information on the type plate
Meaning
Type
Device name
Serial No.
Serial number
min. / max. allowable pressure PS
Minimum/maximum permissible
pressure
max. allowable flow temperature of
system
Maximum permissible flow temperature
of the system
Information on the type plate
Meaning
min. / max. working temperature
TS
Min./max. operating temperature (TS)
Year of manufacture
Year of manufacture
max. system pressure
Max. system pressure
min. operating pressure set up on
site
Minimum operating pressure, set on-
site
4.4
Function
1
Make-up with water e.g. using "Fillcontroll Auto" / Servitec S
2
Control unit
3
Primary vessel as expansion vessel
4
Pressure gauge
WC Make-up line
PIS Pressure sensor
SV
Safety valve
PV Solenoid valve
LIS Weight measuring cell for level measurement
EC
Expansion line
Expansion vessel
A diaphragm divides the interior of the vessel into an air space and a water
space. This prevents the ingress of atmospheric oxygen into the expansion
water. The primary vessel is connected to the air side control unit and connected
hydraulically to the system circuit. Pressure relief is provided on the air side by
the "SV" safety valves of the vessel.
Control unit
The control unit comprises a "CO" compressor and the "Reflex Control Smart"
controller. Via the primary vessel, the pressure is measured with the "PIS"
pressure sensor and the water level with the "LIS" weight measuring cell and the
values are then displayed via the app,
Maintaining pressure
•
If the water is heated, it expands and the pressure increases in the system
circuit. If the pressure set at the controller is exceeded, the "PV" solenoid
valve opens and discharges air from the primary vessel. Water flows from
the system into the primary vessel and the pressure drops in the system
circuit until the pressures in the system circuit and the primary vessel are
the same.
•
The pressure in the system circuit drops when the water cools. When the
pressure drops below the set value, the "CO" compressor cuts in and
delivers compressed air into the primary vessel. This displaces water out of
the primary vessel into the system circuit. The pressure in the system
circuit rises.
Make-up
The addition of more water is controlled via the controller. The "LIS" weight
measuring cell determines the water level and sends this value to the controller.
This controls an external make-up. Water is directly added into the system circuit
in a controlled manner by monitoring the make-up time and the make-up cycles.
Cooke Industries - Phone: +64 9 579 2185 Email: sales@cookeindustries.co.nz Web: www.cookeindustries.co.nz