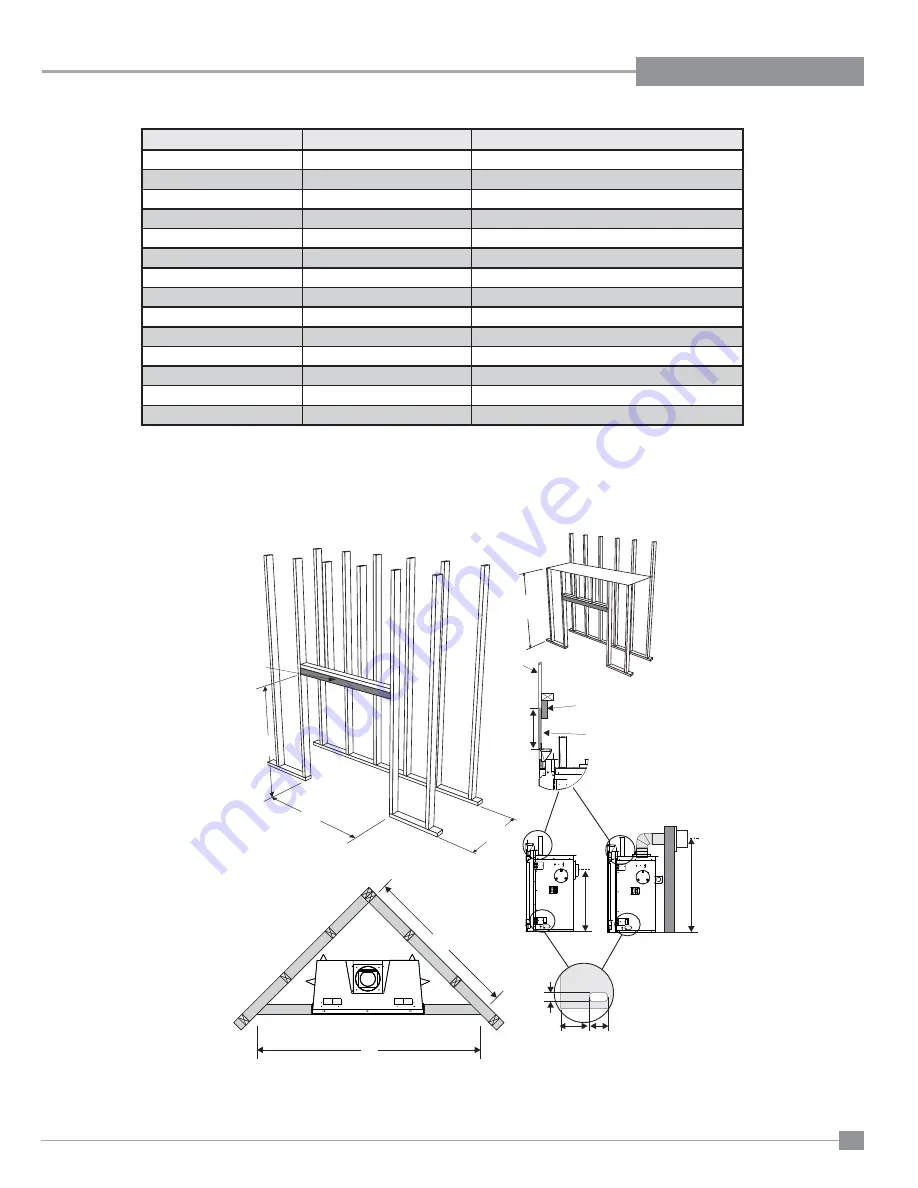
Regency Bellavista™ B41XTCE Gas Fireplace
13
INSTALLATION
FRAMING
Framing Dimensions
Description
B41XTCE
M
Framing Width
47-1/4"(1200mm)
N
Framing Height
49-1/2" (1257mm)
O (Rear Vent)
Framing Depth - Rear Vent
26-1/2" (673mm)
O (Top Vent)
Framing Depth - Top Vent
25-7/8" (657mm)
P
Corner Facing Wall Width
65-1/4" (1657mm)
Q
Corner Facing Wall Width
91-11/16" (2329mm)
R (Rear Vent)
Framed Chase Ceiling - Rear
49-1/2" (1257mm)
R (Top Vent)
Framed Chase Ceiling - Top
54-1/2" (1384mm)
S (Rear Vent)
Vent Centerline Height - Rear
28-1/2" (724mm)
S (Top Vent)
Vent Centerline Height - Top
47-1/2" (1207mm) Rigid / Flex
T
Gas Connection Height
1-1/2" (38mm)
U
Gas Connection Inset
5" (127mm)
V
Gas Connection Width
3-1/4" (82mm)
W
Non-Combustible Top Height
13-1/2" (343mm)
** Important: Framing height requires consideration of the hearth depth. Dimension N = N + the thickness of the installed hearth.
M
N
O
Q
P
R
U V
T
Opening for gas
connection
11" (279mm)
dia. Hole through
wall Vent.
Non-Combustible
Header
(steel stud) on edge
Drywall
(or other
facing)
W
Non-Combustible Facing
S
S
Non-Combustible
Header
(steel stud)
on edge