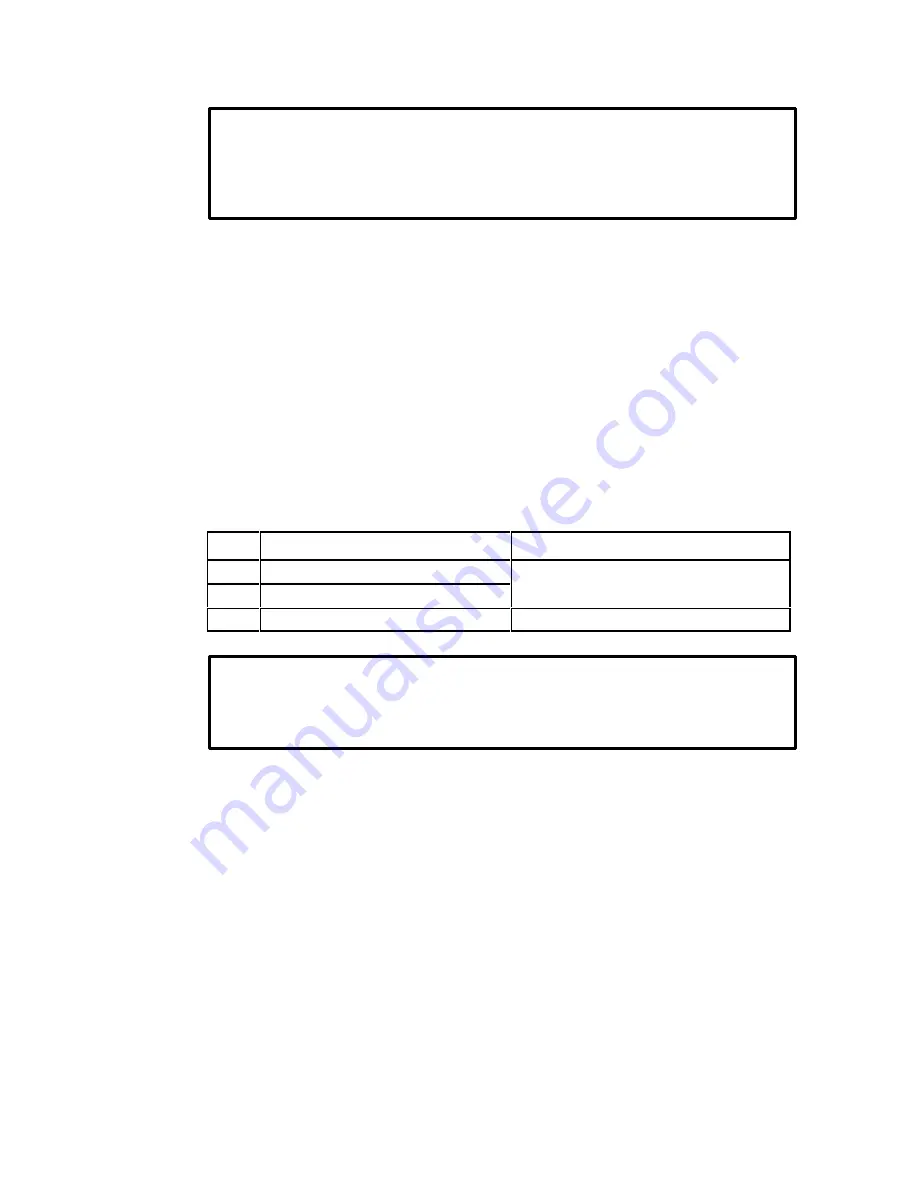
39
Wire AC Power to the Controller
DANGER
DO NOT OPERATE THE CONTROLLER WITH AVAILABLE SHORTCIRCUIT
CURRENTS IN EXCESS OF 10,000 AMPERES. FAILURE TO OBSERVE THIS
PRECAUTION COULD RESULT IN SEVERE BODILY INJURY OR LOSS OF
LIFE.
1. Size the AC line supply conductors for the specific controller rating
and according to all applicable codes.
2. Run the AC line supply through a conduit entry in the bottom of the
controller to terminals TB1L1 and TB1L2/F1.
Wire the DC Motor to the Controller
1. Size the motor armature circuit conductors A1 and A2 according to
all applicable codes.
2. Run the DC motor armature leads and the shunt field supply leads
(if a permanent magnet field motor is not used) through the same
conduit entry used for the AC line supply.
3. Use the appropriate tightening torque as listed in Table 31 for wire
connections to input and output terminals.
Table 31. Terminal Strip TB1/TB2 Tightening Torques (lbsin).
TB
Terminals
Torque
TB1
Input Terminals 51, L1, L2/F1
All: 9 minimum
12 maximum in lbs
TB1
Output Terminals A1, A2/F2
All: 9 minimum - 12 maximum inlbs
TB2
Thermostat 32, 132
4 inlbs
CAUTION:
If motors other than a straight shunt are used with the DC2 controller and
an S1 and S2 winding is present on the motor, additional motor connections other
than those detailed in this instruction manual are applicable. Failure to observe this
precaution could result in damage to, or destruction of, the equipment.
4.
For all models (except DC271, 78, 91 and 98 Reversing and
Dynamic Braking Models):
If CCW motor rotation is desired
looking from the back of the motor or the shaft end), connect motor
armature leads A1 and A2 to controller terminals TB1A1 and
TB1A2/F2, respectively, as shown in Figure 34. If CW motor
rotation is desired (looking from the back of the motor or the shaft
end), reverse the motor armature connections at the motor.
For the Reversing and Dynamic Braking Models DC271, 78, 91
and 98 only:
If CCW motor rotation is desired when the
Forward/Off/Reverse switch is in the FORWARD position (looking
from the back of the motor or the shaft end), connect motor
armature leads A1 and A2 to controller terminals TB3A1 and
TB3A2, respectively. If CW motor rotation is desired (looking from
the back of the motor or the shaft end), reverse the motor armature
connections at the motor.
Summary of Contents for DC2 VS series
Page 1: ......
Page 2: ......
Page 3: ......
Page 4: ......
Page 5: ......
Page 31: ...3 16 419 519 TB2 Motor Mounted D C Tachometer Figure 3 8 D C Tachometer Connection...
Page 48: ...5 6 Figure 5 1 Wiring Diagram of Basic Speed Controller 0 57210 30...
Page 49: ...5 7...
Page 51: ...5 9 J4...