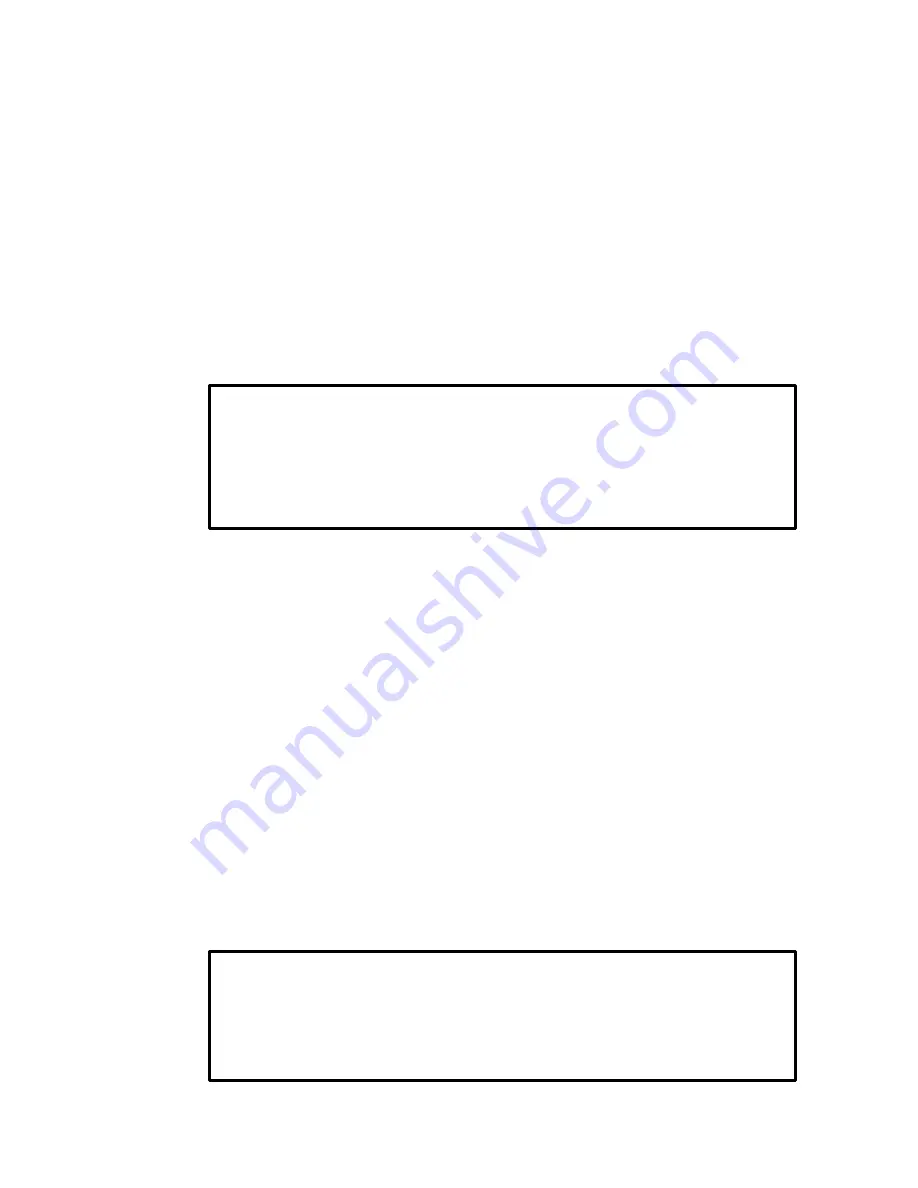
47
6. Check the direction of motor rotation:
D
Press START and quickly press STOP to verify correct motor
rotation. If the motor shaft doesn't rotate because all
potentiometers are set to minimum levels, turn the Speed or
Torque potentiometer slightly CW and repeat this start/stop
operation.
D
If motor shaft rotation is incorrect, press the Stop switch and wait
for the motor to completely stop. Remove AC input power, and
reverse the motor armature power leads A1 and A2 at the motor.
Reapply AC input power and repeat the direction of rotation
check.
D
On applications utilizing DC tachometer speed feedback, when
the direction of rotation of the motor is changed, the polarity of
the tachometer also changes. The connection of the tachometer
must remain 419 negative with respect to 519 for a given
direction or rotation.
DANGER
THE DC TACHOMETER MUST BE CONNECTED WITH THE NEGATIVE LEAD
TO TERMINAL 419 AND THE POSITIVE LEAD TO TERMINAL 519 FOR THE DE
SIRED DIRECTION OF ROTATION. REVERSE CONNECTION WILL CAUSE
THE MOTOR TO RUN AT MAXIMUM UNCONTROLLED SPEED. FAILURE TO
OBSERVE THIS PRECAUTION COULD RESULT IN SEVERE BODILY INJURY
OR LOSS OF LIFE.
7. On controllers employing DC tachometer speed feedback, the
following steps may be used to determine the correct direction of
rotation and the correct polarity of the DC tachometer speed
feedback signal.
D
Turn off power.
D
Reconnect unit as a voltage regulator. Make sure J3 jumper is at
the appropriate voltage level.
D
Remove the DC tachometer leads from terminals 419 and 519,
clearly marking the leads to distinguish one from the other, and
connect a DC voltmeter (0 to 60 volt scale) to the DC
tachometer leads.
D
Turn on power.
D
With the desired direction of motor rotation established, using the
voltmeter that is connected to the DC tachometer signal leads,
determine the polarity of the DC tachometer leads. Mark the
negative polarity lead 419 and the positive lead 519.
D
Stop the controller, remove AC power, replace the J3 jumper to
the tachometer position and connect the DC tachometer leads
to the controller as noted above, (-) 419 and (+) 519.
8. Adjust the speed or torque range:
WARNING
DO NOT DEPEND ON THE MINIMUM POSITION OF THE SPEED OR TORQUE
SETTING POT TO STOP THE MOTOR. IN THE MINIMUM POSITION, THE CON
TROLLER AND MOTOR ARE STILL ENERGIZED. THE DRIVE MAY RESTART
UNEXPECTEDLY. FAILURE TO OBSERVE THIS PRECAUTION COULD RE
SULT IN BODILY INJURY.
Summary of Contents for DC2 VS series
Page 1: ......
Page 2: ......
Page 3: ......
Page 4: ......
Page 5: ......
Page 31: ...3 16 419 519 TB2 Motor Mounted D C Tachometer Figure 3 8 D C Tachometer Connection...
Page 48: ...5 6 Figure 5 1 Wiring Diagram of Basic Speed Controller 0 57210 30...
Page 49: ...5 7...
Page 51: ...5 9 J4...