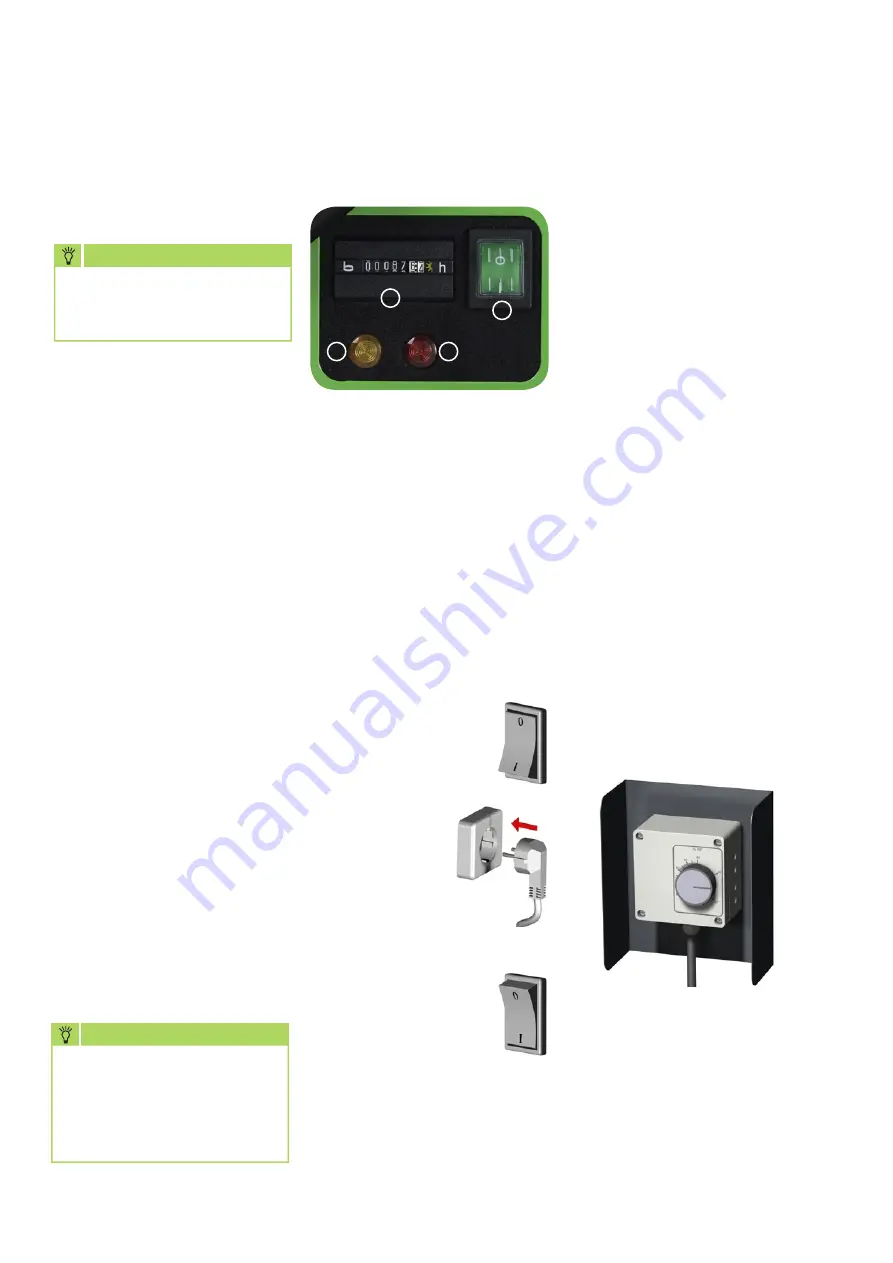
Starting the unit
1. Set operating switch [2]
to position “0” (Off).
2. Connect the
mains plug of the
unit to a correctly
installed and
protected socket-
outlet.
20V/50 Hz
.
3. Set the operating switch
[2] to position “I” (On).
The green pilot light in the switch
[2] illuminates.
The units switch on with a delay
of about 10 seconds and then
operate in continuous duty.
Prior to each commissioning or as
required, the air inlet and outlet
must be checked for clogging.
Prior to commissioning
■
All electric extension cables
must have an adequate cross-
section and must only be used
fully uncoiled or unrolled.
■
Do not pull at the cable.
■
After switching on, the units
operate fully automatically until
switched off normally via the
float switch of the filled con-
densate container.
(not with AMT 110-E).
■
The condensate container must
be placed correctly.
■
In order to prevent compressor
damage, the units must be pro-
vided with a safeguard prevent-
ing immediate reconnection of
the compressor after switching
off.
The compressor initially
switches on again after a wait-
ing time of about 1 minute!
Commissioning
Control panel
1
2
1 = Operating hour counter
2 = Operating switch with
“pilot light”
3 = YELLOW - Pilot light
„Container full”
4 = -RED-Pilot light
„Fault/Overheating“
Operation with a hygrostat
The REMKO hygrostat (accessory)
is supplied with a special adapter
plug.
Commissioning of the units in con-
junction with a hygrostat and its
operation take place as follows:
1. Plug the adapter plug into a cor-
rectly protected socket-outlet.
2. Place the hygrostat at a suitable
point in the room to be dehu-
midified. Not in the immediate
vicinity of the unit and heat
sources.
3. Plug the mains plug (or a cable
extension) into the adapter plug.
4. Set the required humidity on the
hygrostat.
5. Set the operating switch [2] on
the unit to the position “I”.
The units switch on automatically
when the prevailing humidity is
higher than the value preset on the
hygrostat.
The units now operate fully auto-
matically until the relative humid-
ity (% RH) is reached or normal
switch off takes place via the float
switch in the condensate container
(not with AMT 100-E). In this case,
the yellow “container full” pilot
light illuminates.
nOTE
Clogged outlets and filters
must immediately be cleaned
or replaced.
nOTE
At room temperatures below
10°C
and a relative humidity
below
0%
, economical/ef-
ficient use of the unit is not
ensured.
10
REMKO AMT