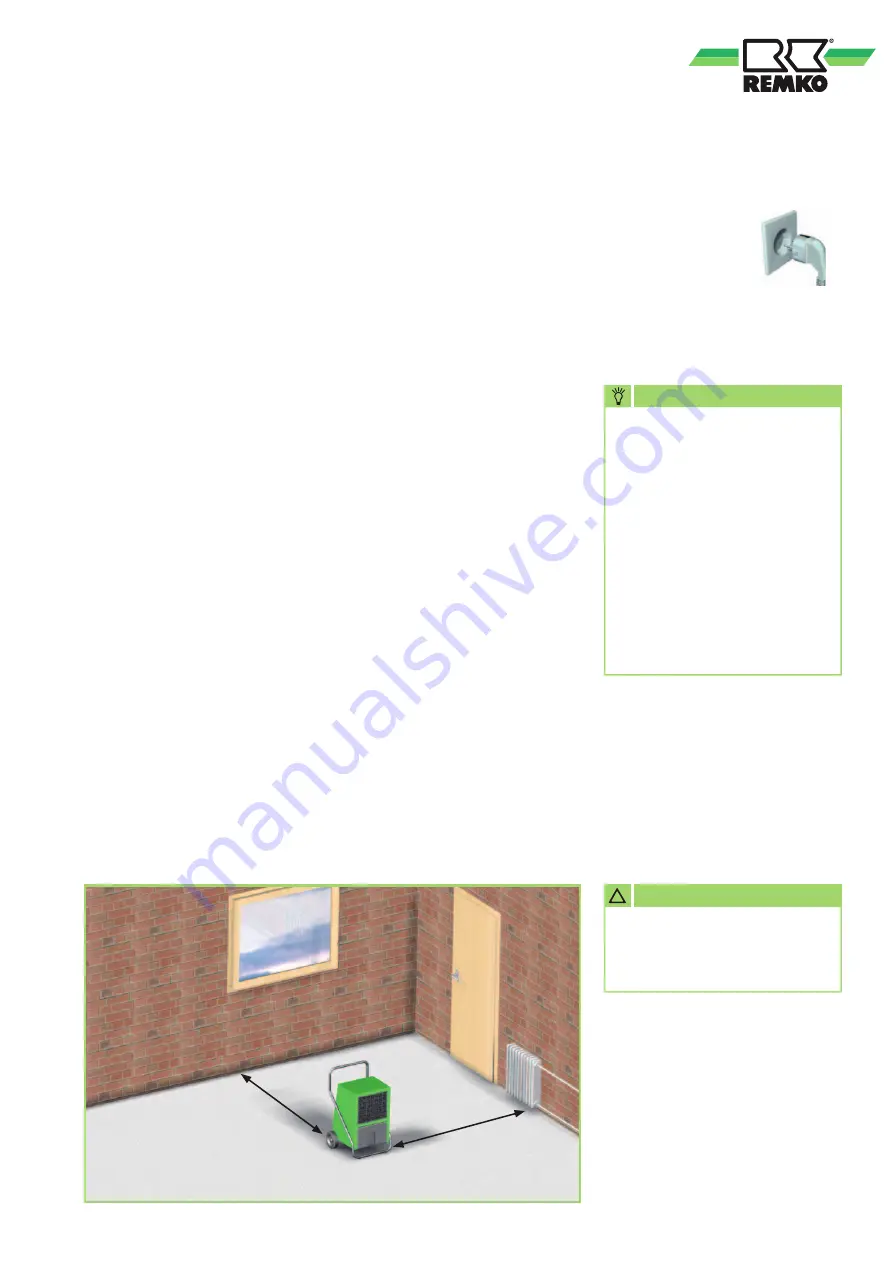
Electrical connection
■
The units are operated
with 230 V / 50 Hz
alternating current
■
The electrical connection is
made using a built-in mains
cable with earthed safety plug
■
Extensions
to the connection cable
may only be carried out by
authorised electricians, subject
to the length of the cable,
connected load of the unit and
taking into consideration how
the unit is used at its location
Set-up
For the best economic and safe use
of the units, the following notes
must be followed in full:
■
The units must be set up
in an upright and level position,
to ensure that the condensate
can drain freely
■
To ensure optimum air
circulation, the units should be
set up in the centre of the room,
where possible
■
It must be ensured that the air
can be sucked in on the front
of the unit and blown out of
the rear of the unit without
obstruction
■
Observe a minimum clearance
of 50 cm from walls at all times
■
Units must never be set up
in the immediate vicinity of
heaters or other sources of heat
■
The room being dried or
dehumidified must be closed
to the neighbouring atmosphere
■
Air circulation is improved if
the unit is set up approx. 1 m
above the ground
■
Avoid having opened windows
and doors etc., and avoid
frequent entry to or exit from
the room as much as possible
■
If the units are to be used
in dusty environments,
appropriate care and
maintenance measures
should be taken according
to the relevant conditions
■
The output of the unit is entirely
dependent on the conditions
inside the room, room
temperature, relative humidity
and observance of the set-up
instructions
■
The units may not be used
in environments containing
a great deal of dust or chlorine,
or in places with atmospheres
containing ammonia
ATTENTION
All cable extensions must only
be used in fully un-reeled or
reeled off condition.
NOTE
The electrical connection
to the units must be made
at feedpoints with residual
current devices in accordance
with VDE 0100, Section 704.
When installing the units
in extremely damp
environments such as laundry
rooms, showers etc., the unit
must secured with a residual
current device provided
by the customer in accordance
with the regulations.
Wall clearance
min. 0.5 m
Maintain adequate clearance from
heaters or other sources of heat.
Keep windows and doors closed!
!
9
Summary of Contents for AMT 115-E
Page 2: ......