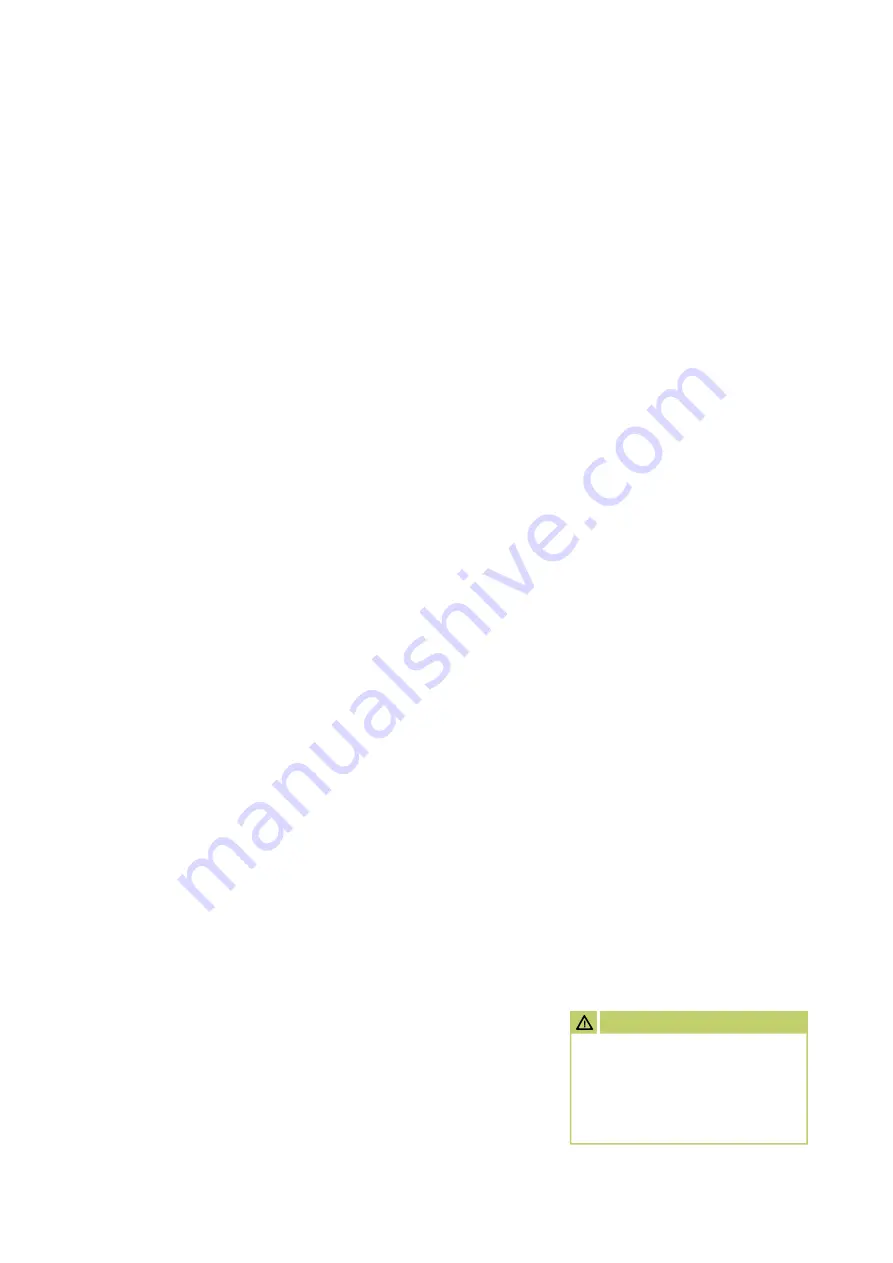
Heat of condensation
The energy transferred from the
condenser to the air is composed
of:
1. Heat energy previously removed
in the evaporator.
2. Electrical motive energy.
3. Heat of condensation released
during condensation of the water
vapour.
For the change from a liquid to a
gaseous state, energy is necessary.
This energy is termed heat of
evaporation.
It does not cause any rise of
temperature, it is only necessary
for the change from a liquid to a
gaseous state.
Vice versa, energy is released during
the liquefaction of gas, which is
termed heat of condensation.
The amount of heat of evaporation
and condensation is the same.
For water, this is:
2250 kJ/kg (4.18 kJ = 1kcal)
This shows that a relatively large
amount of energy is released
through the condensation of water
vapour.
If the moisture to be condensed is
not introduced through evaporati-
on in the room itself, but from out-
side, e.g. via ventilation, the heat
of condensation released in the
process contributes towards room
heating. In drying processes, the
heat energy is recirculated, which
is consumed during evaporation
and released during condensation.
The supplied air during dehumidi-
fication creates a large amount of
heat energy, which is expressed in
a rise of temperature.
The time necessary for drying
normally does not depend only
on the unit capacity, but is rather
determined by the rate at which
the material or parts of the build-
ing release their moisture.
Safety information
The units were subjected to ex-
tensive material, functional and
quality inspections and tests prior
to delivery.
However, the units may constitute
a hazard if used by untrained per-
sonnel, improperly or not for the
intended purpose.
The following information must
be observed:
■
The units must not be installed
and operated in hazardous lo-
cations.
■
The units must not be installed
and operated in atmospheres
containing oil, sulphur or salt.
■
The units must not be exposed
to direct water jets.
■
The air openings must always
be kept free.
■
The air suction grille must al-
ways be kept free of dirt and
loose objects.
■
The units must not be covered
during operation.
■
Never insert foreign objects
into the units.
■
All electrical cables outside the
units must be protected against
damage (e.g. animals, etc.).
■
The units must only be in-
stalled or mounted in the in-
tended position (horizontal).
■
Free and frost protected
condensate discharge must
always be ensured.
■
The unit connections must
always comply with the
respectively applicable
installation regulations.
ATTENTION
The units must be installed
and mounted so that they
are easily accessible for
monitoring, repair and
maintenance.
6
REMKO SLN 40-80