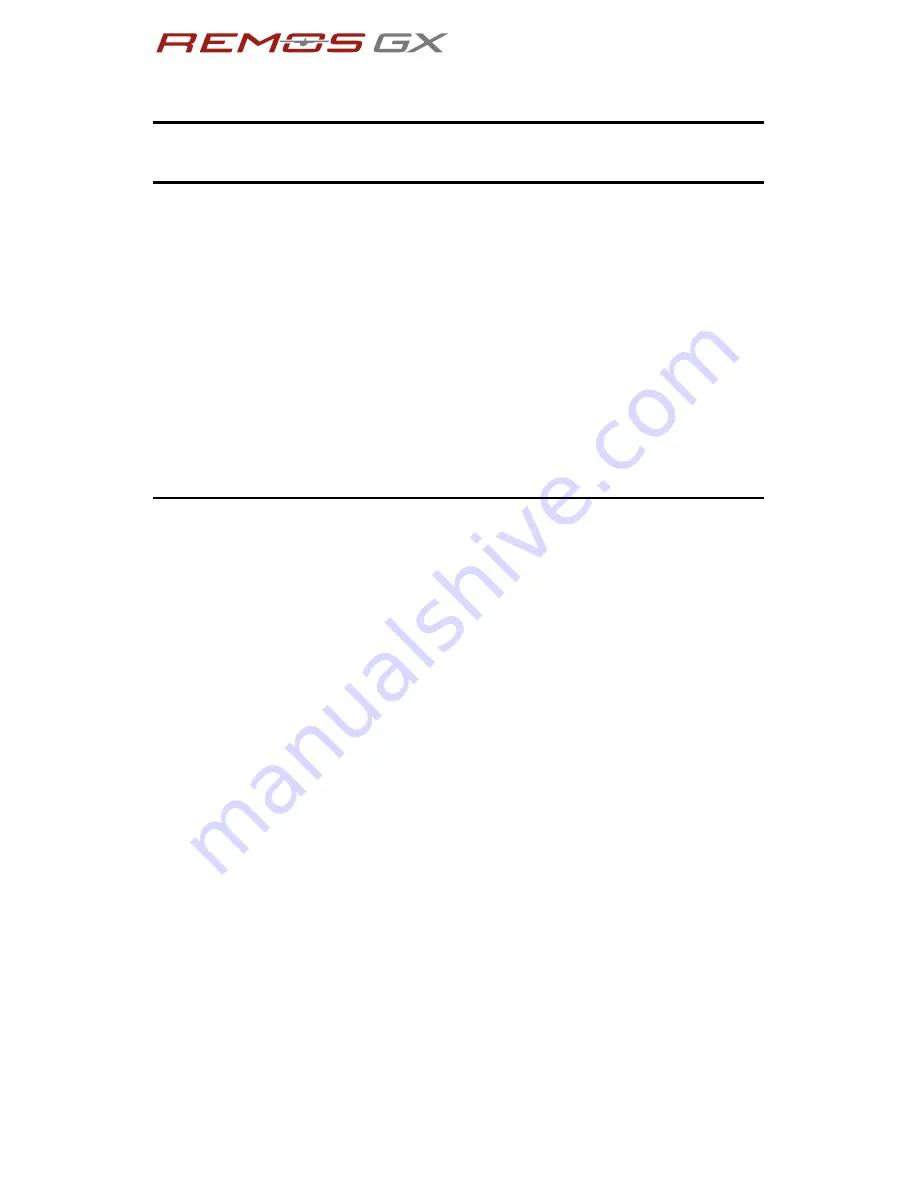
G3-8 MA FM 1204 - R07
4
Normal Procedures
Normal Procedures 4 - 9
4.8
Taxi
Procedure
1. landing light
RECOMMENDED
2. parking brake
RELEASE
3. engine speed
AS REQUIRED
4. control on ground
VIA PEDALS
5. min. turn radius
ca. 20 ft = 7 m
6. braking
AS REQUIRED
7. taxi speed
APPROPRIATE
4.9
Departure
Briefing
1. wind, weather, visibility
OK
2. ATIS
CHECKED
3. runway
CORRECT DIRECTION
4. traffic pattern
ALTITUDE and ROUTING
Summary of Contents for REMOS GX nXES
Page 12: ...G3 8 MA FM 5201 R01 1 General Information General Information 1 8 intentionally left blank...
Page 92: ...G3 8 MA FM 5205 R01 5 Performance Performance 5 14 intentionally left blank...
Page 163: ...POH Supplement Flight Training...
Page 177: ...POH Supplement Glider Towing...
Page 197: ...POH Supplement Banner Towing...
Page 213: ...POH Supplement Continued Airworthiness...
Page 229: ...POH Supplement Abbreviated checklists...
Page 235: ...G3 8 MA FM 1213 R01 Imprint Supplement Abbreviated Checklists 13 6 intentionally left blank...