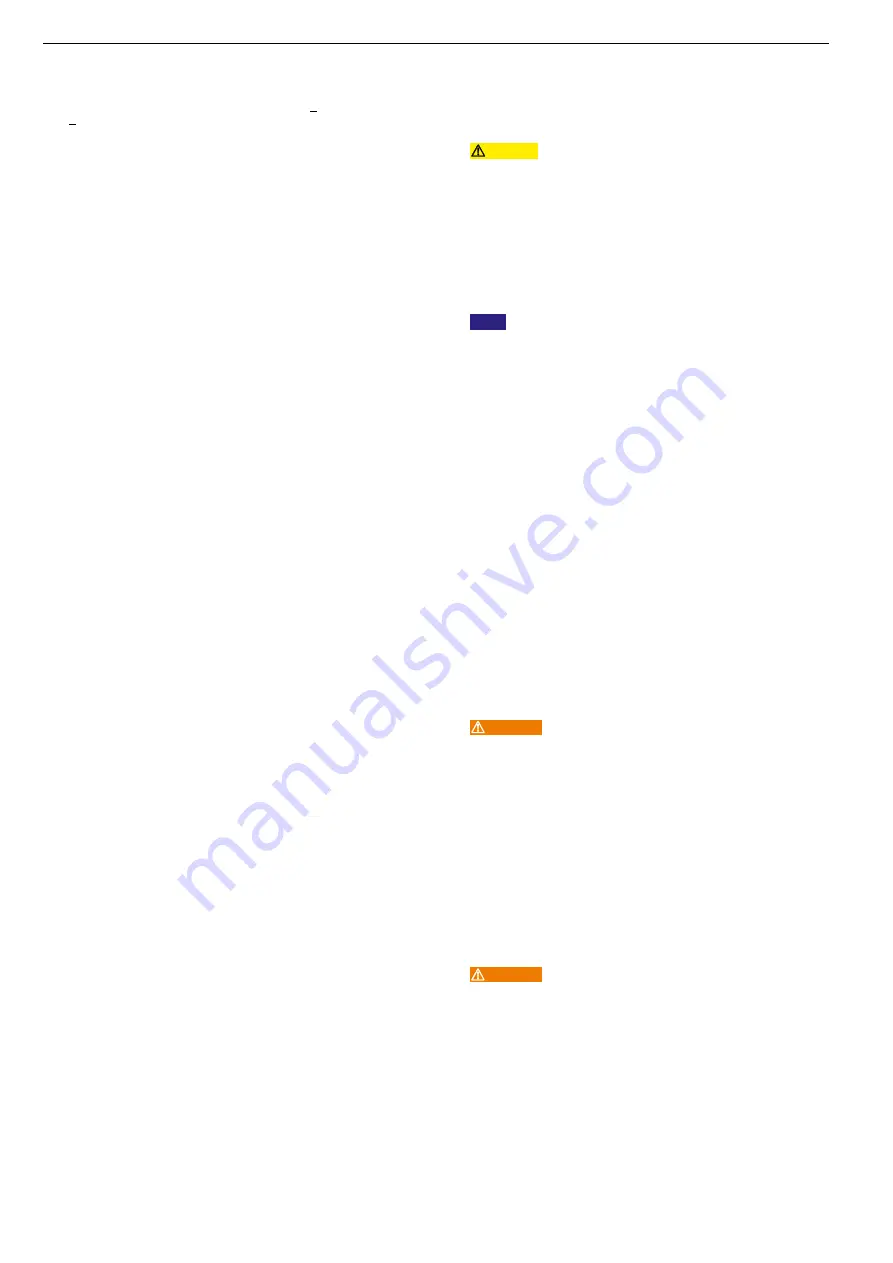
The temperature can be adjusted on all REMS sleeve welders EE. They are
supplied with an electronic thermostat. The type of thermostat fi tted is identifi ed
on the rating plate by code letters, examples of which are given below:
for ex. REMS MSG 63 EE: Adjustable temperature (
E
), electronic thermo stat
(
E
). The preset temperature is adjusted to within ± 1°C.
Mechanical temperature control (thermostat) FE
The required operating temperature is set at 263 ± 3°C. Pay attention to the
manufacturer’s information pipe and fi ttings! Before starting any welding work,
the temperature on the surface of the welding tools should be monitored.
2.5 Preheating of the sleeve welding unit EE
The heating element sleeve welding unit starts to heat up when the connecting
cable is connected to the mains. The red mains indicator lamp (6) and the green
temperature indicator lamp (7) light up. The electrical device takes about 10
minutes to heat up. On reaching the set nominal temperature, the built-in
temperature controller (thermostat) in the device switches off the power supply
to the heating element. The red mains indicator lamp stays alight. The green
temperature indicator lamp fl ashes and indicates the constant switching off or
on of the power supply. The welding process can begin at the earliest after
waiting another 10 minutes (DVS 2207 Part 1).
Preheating of the sleeve welding unit FE
If the connecting lead of the heating element sleeve welding unit is connected
to mains, an acoustic signal sounds and the device begins heating up. The
green mains indicator lamp (6) and the yellow temperature indicator lamp (7)
light up. The device takes about 10 minutes to heat up. On reaching the set
nominal temperature, the built-in temperature controller (thermostat) switches
off the power supply to the heating element and an acoustic signal sounds
again. The yellow temperature indicator lamp fl ashes. The welding process
can begin after waiting another 10 minutes (DVS 2207 Part 1).
2.6 Selecting the correct welding temperature EE
The temperature of the heating element sleeve welding unit is preset to the
average welding temperature for PP pipes (260°C). It may be necessary to
correct this welding temperature depending on the pipe material. The manu-
facturer information for pipe or mouldings must be observed accordingly! Ambient
infl uences (Summer/Winter/wind/humidity) may also necessitate temperature
corrections. Therefore the temperature of the heating tools (heating spigot and
heating socket) should be checked, for example, with a quick display temper-
ature measuring instrument for surface measurements with a contact surface
of approx. 10 mm. The temperature can be corrected if necessary by turning
the temperature setting screw (8). If the wrong temperature is set, please note
that the heating element may only be used 10 minutes after reaching the nominal
temperature.
3 Operation
The quality of the welded connections depends on the welder's qualifi cation,
the suitability of the machines and devices used as well as the compliance with
welding regulations. The weld can be tested by non-destructive or destructive
methods. Welding work must be supervised. The type and scope of supervision
must be agreed between the contract parties. It is recommended to document
the procedure data in welding logs and on data media. Within the scope of
quality assurance, it is recommended to make and test sample welds under
the given working conditions before beginning and during the welding work.
Every welder must be trained and have valid proof of qualifi cation. The intended
area of application may be decisive for the type of qualifi cation.
3.1 Description of process
In welding with the sleeve welder, the pipe and sleeve are welded together
overlapping. The end of the pipe and moulded sleeve are heated to welding
temperature by means of the welding tool (spigot and socket), then welded
together. The end of the pipe and fi tting are matched to the welding spigot and
socket respectively in such a way that a build-up of pressure takes place in the
joint when the two components are mated (Fig. 4).
Guideline DVS 2208 specifi es two methods of sleeve welding in cases where
the heated spigot and socket are of different sizes. In the case of method A,
no provision is made for any mechanical pre-processing of the pipe, while in
the case of method B, the pipe is mechanically stripped. The REMS spigot and
socket are confi gured solely for method A, i.e. no mechanical pipe processing
is required.
Sleeve weldings can be made manually on pipes up to and including diameters
of 50 mm. With larger pipes, a suitable welding machine must be used because
of the increasing forces required to achieve the joint.
3.2 Preparations for welding
Take care to observe the information issued by the manufacturer of the pipes
or mouldings. The end of the pipe must be cut off square and fl at, either with
a REMS RAS pipe cutter (see 1.2.) or REMS ROS pipe shears (see 1.2.). In
addi tion, the end of the pipe should be chamfered to facilitate insertion into the
socket (Fig. 6). This process should be performed with the REMS RAG pipe
chamfering unit (see 1.2.). Immediately before welding, the end of the pipe and
interior of the sleeve and, if necessary, the heating spigot and socket should
be cleaned with non-adherent paper or a non-fraying cloth and spirit or indus-
trial alcohol. In particular, no remnants of plastic must be left adhering to the
coating on the heating spigot or socket. When cleaning the welding tools, take
care to ensure without fail that their anti-adhesive coating is not damaged by
tools. The welding surfaces must not be touched again before welding takes
place.
CAUTION
CAUTION
Only touch the device on the handle (3) when it is hot! Never touch the
heating element (4), the heating tools (5) or the metal parts between the
handle (3) and the heating element (4)! Danger of burns!
3.3 Welding process stages
3.3.1 Heating-up
For the heating-up process, the pipe and moulding are pushed axially onto the
welding tools in a continuous movement until they reach the stop or the marking
on the tools. The heating-up time specifi ed in Fig. 5, colunn 2 must be observed.
During the heating process, heat penetrates into the joint faces and brings them
up to welding temperature.
AVIS
AVIS
If an acoustic signal sounds during heating up, the pipe and fi tting may not be
joined. The weld could otherwise be faulty and useless.
3.3.2 Changeover and joining
After the heating process, the pipe and moulding are pulled away from the
welding tools in a series of jerks and pushed together, without twisting, as far
as they will go. The changeover time specifi ed in Fig. 5, column 3 must not be
exceeded, otherwise the joint faces will cool to an impermissible extent.
3.3.3 Setting
The joint must be allowed to set (i.e. held) in accordance with the data given
in Fig. 5, column 4.
3.3.4 Cooling
The joint must not be subjected to the stresses imposed by further pipe-laying
operations until the cooling-off period (Fig. 5, column 5) has expired.
4 Maintenance
Notwithstanding the maintenance described below, it is recommended to send
in the power tool to an authorised REMS contract customer service workshop
for inspection and periodic testing of electrical devices at least once a year. In
Germany, such periodic testing of electrical devices should be performed in
accordance with DIN VDE 0701-0702 and also prescribed for mobile electrical
equipment according to the accident prevention rules DGUV, regulation 3
"Electrical Systems and Equipment". In addition, the respective national safety
provisions, rules and regulations valid for the application site must be considered
and observed.
4.1 Maintenance
WARNING
WARNING
Pull out the mains plug before maintenance work!
The anti-adhesive coating of the heating tools (5) must be cleaned with lint-free
paper or cloth or technical alcohol before every welding process. Plastic residue
stuck to the heating tools must be removed immediately with lint-free paper or
cloth or technical alcohol. Make absolutely certain that the anti-adhesive coating
of the heating tools is not damaged by the use of tools. The use of white spirit
to clean the heating tools can lead to a diminished quality of the weld due to
the water that it contains.
Clean plastic parts (e.g. housing) only with the REMS CleanM machine cleaner
(Art. No. 140119) or a mild soap and a damp cloth. Do not use household
cleaners These often contain chemicals which can damage the plastic parts.
Never use petrol, turpentine, thinner or similar products to clean plastic parts.
Make sure that liquids never get onto or inside the power tool. Never immerse
the power tool in liquid.
4.2 lnspection/repairs
WARNING
WARNING
Pull out the mains plug before carrying out maintenance or repair work!
This work may only be performed by qualifi ed personnel.
eng eng
10
Summary of Contents for MSG 125 EE
Page 111: ...111...