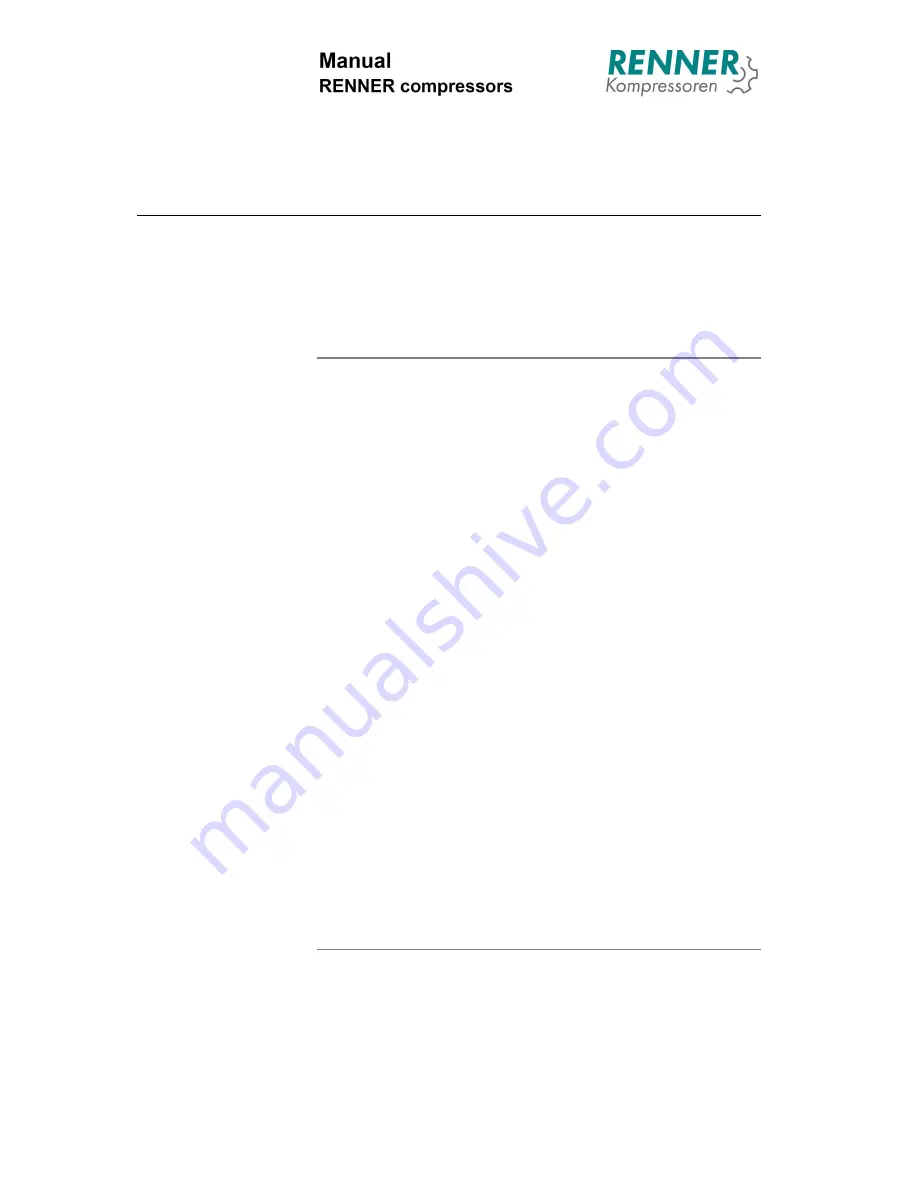
AW2 – Appendix Motor Bearings
AW-1
Appendix W2
Maintenance of Motor Bearings
This Appendix provides an overview of how motor bearings are
to be maintained. This description only applies to current sys-
tems and may differ to the maintenance required for older mo-
tors.
Our compressors
up to 37kW
are fitted with motors having
closed, continuously lubricated deep-groove ball bearings –
theoretical service life is between 15,000 and 30,000 operating
hours (oh). If operating conditions are different to that defined
in the instruction manual, it is imperative that the maintenance
intervals are adjusted to the prevailing circumstances and con-
ditions to ensure reliable operations. Should there be high lev-
els of dirt and dust, frequent switch-ons and high ambient tem-
peratures as well as operations at 60Hz, the maintenance inter-
vals must be adjusted accordingly.
1. Switch off unit and prevent it from being restarted by
accident.
2. If applicable, uninstall the motor and remove the ancillary
components (fan impeller, frame, fan cover, pulley)
3. Disassemble the bearing cover (center) and bearing shield
(outside)
4. Remove the old bearing with a puller (if difficult, carefully
warm up the bearing) and remove the old grease
5. Carefully warm up the inner ring of the new bearing
6. Push the new bearing to the stop on the shaft and keep it
there briefly
7. Generously grease the new bearing with suitable grease
8. Re-assemble the bearing cover and bearing shield
9. Re-install bearing seal
The type designations of the motor bearings can be found in
Table 1.
Contents
Continuously lubri-
cated motor bear-
ings
Description
Procedure for re-
placing bearings