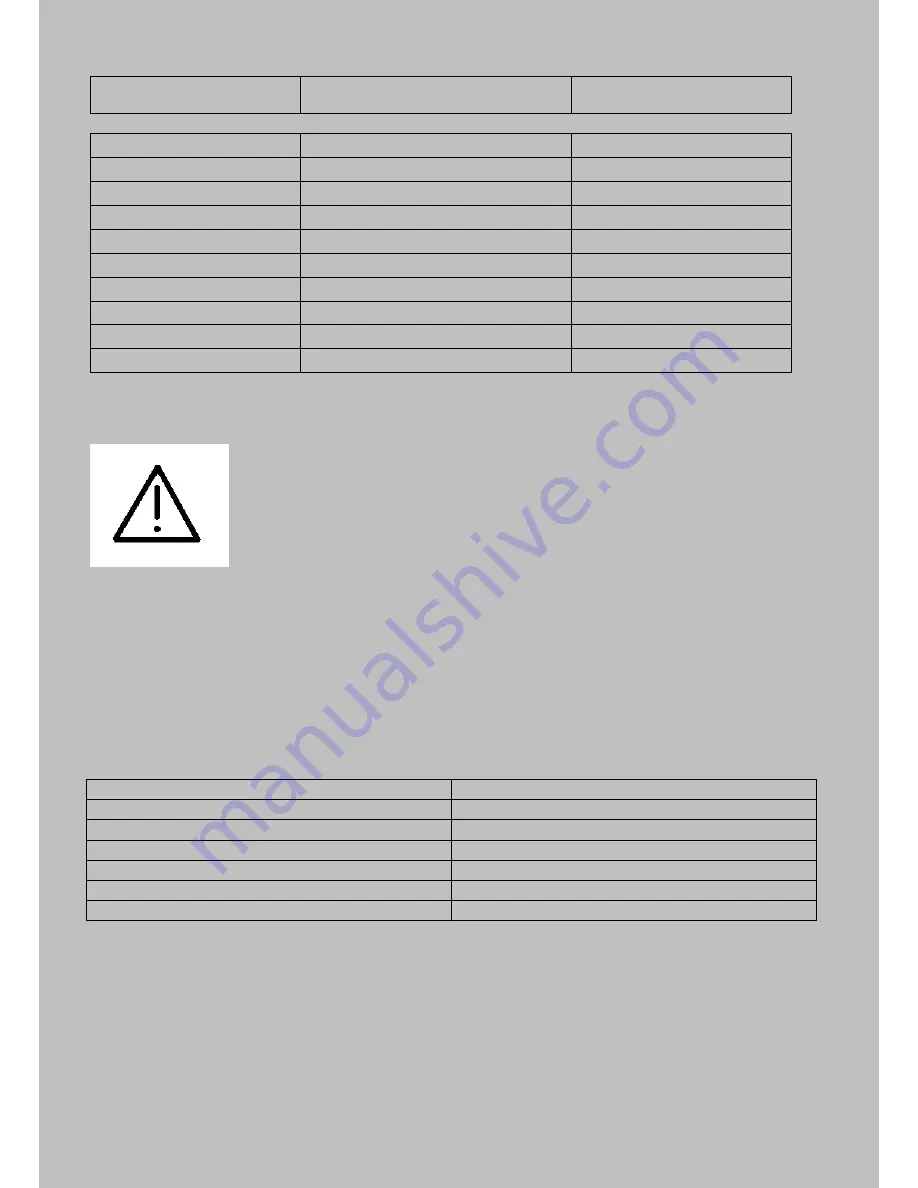
Operation and Maintenance Manual – Steam sterilizers mod. BABY S
Rev. 01 del 01-07-2013 - C:\Documenti\Manuali di istruzione\BABY S GB-R01.doc
Pag. 5 di 28
Description
Unit of measurement
Values
Power source voltage rating
V
230 V.a.c. ~
Power source frequency
Hz
50
Machine power rating
W
1000
Boiler volume
mm
Ø 170 x 270
Operating pressure
Bar
2.1 - 1.1
Machine dimensions X, Y, Z
mm
390 x 370 x 300
Gross weight
Kg
25
Pack dimensions
mm
470 x 450 x 380
Operating temperatures
°C
+ 3°C
……
+ 35°C
Distance from walls
cm
8 - 10
X = depth
Y = width
Z = height
The electrical system is protected against the risk of over-currents installed inside
the machine by two 10 A delayed action fuses ( T 10 A ).
The electronic control and powering boards protect the various users by means of 3
dedicated fuses: 2 quick-acting 1 A types (F 1 A) and one 100 mA delayed action
type (T 100 mA) – (see enclosed wiring diagram).
Only have these fuses changed by a skilled electrician.
The noise level of the machine has been tested. The continuous equivalent weighted
acoustic pressure level A is less than 70 dB (A) and the continuous equivalent
weighted acoustic power level A does not exceed 85 dB (A). The measured noise
level measured is therefore very low. For this reason, the operator need not take any
particular measures (also in view of the fact that the machine operates
automatically).
DATA AND SPECIFICATIONS OF THE PRESSURIZED VESSEL:
Serial N° of vessel, Serial N° of door
Month N°, Year N° (see internal label)
Max. operating pressure:
2.4 Bar
Max. operating temperature:
160°C
Min. operating pressure:
-0.9 Bar
Test pressure:
8 Bar
Reference standards:
TRD 421
Volume of vessel:
7 lt.