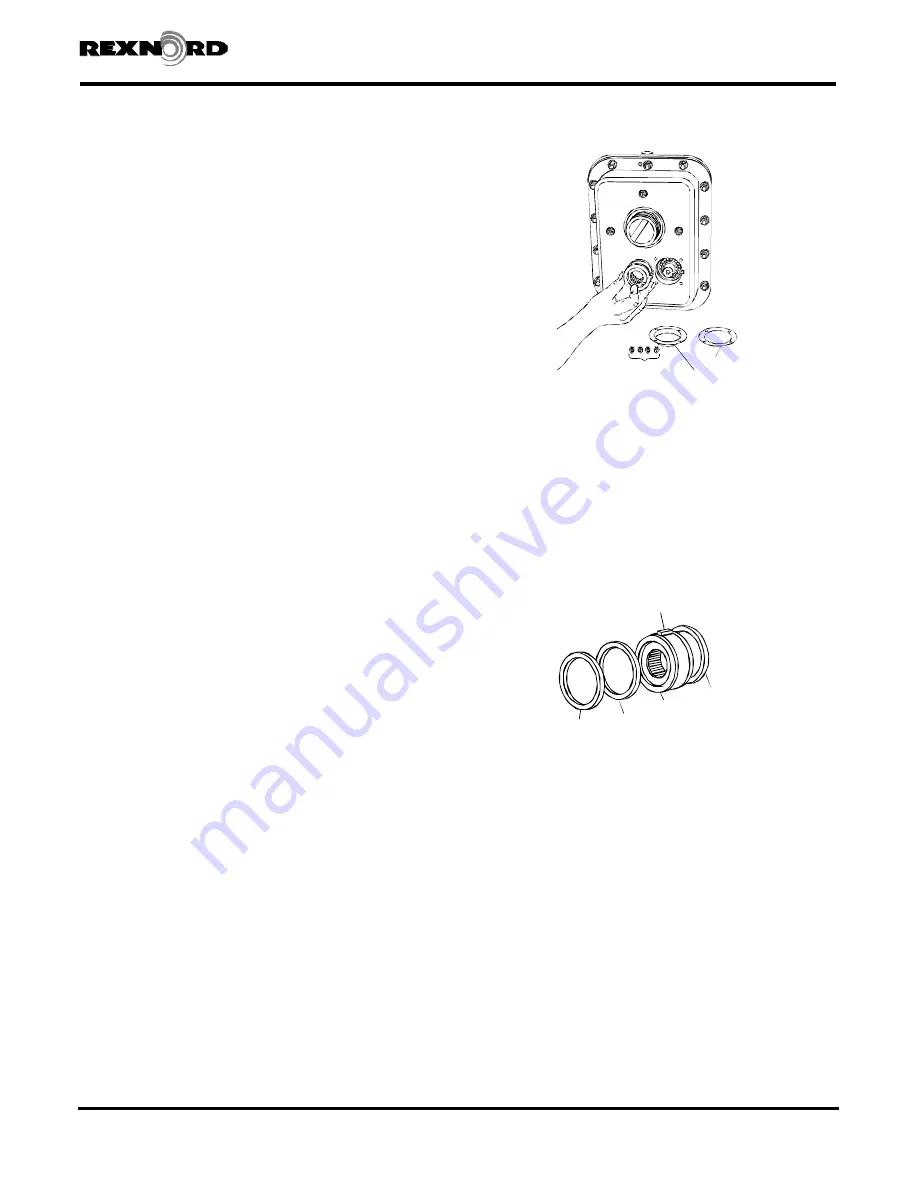
Introduction
The following instructions apply to INSTALLATION ONLY of internal
backstops in horizontal drives, Sizes 5107 thru 5215 single and
double reduction and Size 5307 & 5315 double reduction.
CAUTION:
If backstop is to be replaced, the high speed shaft
must also be replaced. Refer to instructions regarding high
speed shaft replacement, Section
III
.
Remove all external loads from system before servicing drive or
accessories, and lock out starting switch of prime mover.
Lubricant
PETROLEUM BASED LUBRICANTS —
Use R & O type
lubricants which do not contain anti-wear(AW) additives if the
drive is equipped with an internal backstop.
CAUTION:
Do not use EP lubricants, lubricants with anti-wear
additives or lubricant formulations including sulfur, phosphorus,
chlorine, lead derivatives, graphite or molybdenum disulfides in
drives equipped with internal backstops. Refer to Appendix A for
proper selection of petroleum based lubricants. Use of an
improper lubricant will contribute to premature wear or
malfunction of the backstop.
SYNTHETIC LUBRICANTS —
Synthetic lubricants of the
polyalphaolefin type may be used in drives with internal backstops.
Before installing backstop, check direction of free rotation
(overrunning) indicated by the arrow etched on each side of the
backstop.
Backstop Application
Backstops are designed to prevent reverse rotation or backrun
without backlash in applications such as conveyors, bucket
elevators, fans, rotary pumps and kilns. Backstops are not
approved for use on systems that are designed for handling of
people such as elevators, manlifts, ski tows and ski lifts. DO
NOT use a backstop as a substitute for a brake.
Indexing
DO NOT use the backstop for indexing applications. The
backstop is designed to prevent reverse rotation five times or less
in eight hours, with one minute or more in overrunning direction
between backstopping load applications. If backstopping
operations are more frequent, or the time between operations is
less than one minute, the backstop is classified as an indexing
device and must be referred to the Factory.
Installation
(Backstop Added to Existing Drive Only)
1.
DRIVE PREPARATION:
Drain oil from drive. Remove
fasteners Ref. #27, end cover Ref. #23, and gasket Ref.
#16, Figure 1. Keep Size 5115J and 5207J end covers,
Size 5207J fasteners and all lock washers for reuse, all
other parts may be discarded.
2.
BACKSTOP PREPARATION:
Remove backstop Ref. #5A1
from the kit and wipe off any excess lubricant. On drive sizes
5107 (all ratios) and 5115 (24.87 ratio), assemble retaining
ring Ref. #5A2 onto one of the grooves on the backstop OD.
On drive size 5115J25, assemble spacer Ref. #5A6 to
backstop OD adjacent to retaining ring on inboard side. All
other size 5115J and larger drives, insert housing spacer Ref.
#5A3 (retaining ring used as housing spacer on drive size
5207J) into housing bore adjacent to bearing cup (Figure 2).
Assemble key Ref.#5A4 to backstop keyway (spacer Ref. #5A6
is between retaining ring and key on 511J25 backstop).
3.
ALL SIZES — BACKSTOP INSTALLATION:
Apply oil to
the O.D. of the high speed shaft backstop journal and the
sprags inside of the backstop. Align the backstop key with
the keyway in the exposed housing bore and carefully slide
the backstop into the bore while slowly rotating the high
speed shaft. The shaft will only rotate in one direction. DO
NOT FORCE OR HAMMER; this may damage the shaft or
misalign the sprags.
Check operation of backstop by turning high speed shaft in
required direction of rotation by hand. If the shaft does not
rotate in the required direction, remove backstop, reverse
it, reposition the retaining ring and spacer (where used)
and reinsert it into the housing bore as instructed.
Rexnord Industries, LLC
(PN-2128394)
378-200
3001 W. Canal St.,Milwaukee, WI 53208-4200 USA Telephone: 414-342-3131
November 2010
Fax: 414-937-4359 e-mail: info@rexnord.com web: www.rexnord.com
Supersedes 6-07
REF. #23 GASKET
REF. #16
SHAFT COVER
REF. # 27
FASTENERS
Figure 1
Backstop Installation
Falk™ Quadrive Shaft Mounted Drives Model A
•
Appendix B
Sizes 5107-5315
(Page 27 of 44)
REF. #5A4
REF. #5A2
DRIVE SIDE
REF. #5A1
REF. #5A6
SHAFT
COVER
SIDE
REF. #5A3 SPACER
(5115J25 ONLY)
Figure 2