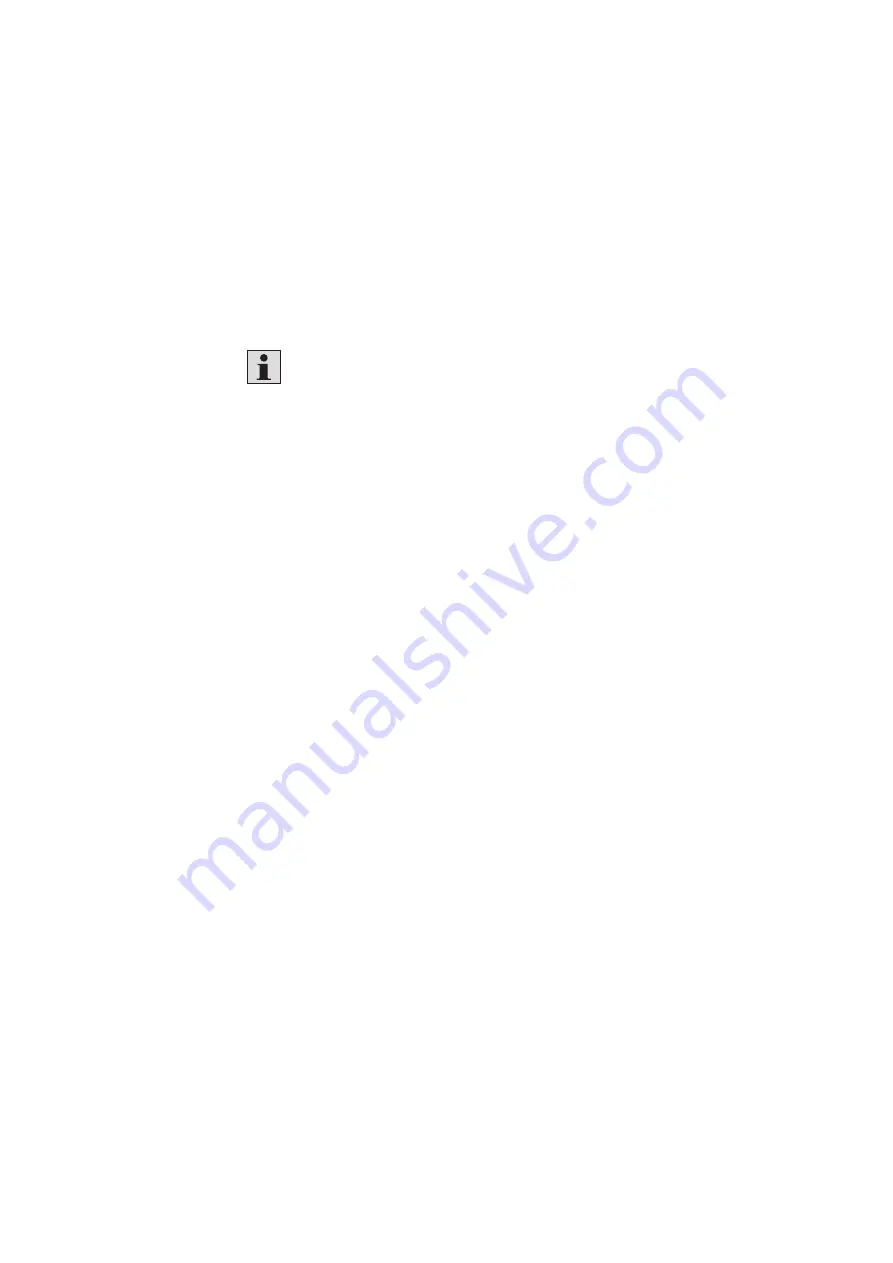
Transport and storage 27/76
CytroPac, RE 51055-B/02.2021,
Bosch Rexroth AG
6.2 Storing the hydraulic power unit
▶
Store the hydraulic power unit in a dry location at constant temperature and in its
original packaging, if possible.
Ideal storage temperature: +5 °C to +25 °C.
▶
Provide for 100 % UV protection.
▶
Store the hydraulic power unit protected against shocks.
▶
Store the hydraulic power unit in an upright position.
▶
Make sure that the cover of the hydraulic power unit is closed during storage.
The maximum storage time of the hydraulic power unit is 12 months.
If the storage time exceeds 12 months, check the function of the hydraulic power
unit and flush it with suitable cleaning liquid prior to commissioning.
Carry out flushing as described in chapter 8.1.4 “Flushing the hydraulic system“
on page 49.
Storage conditions
Maximum storage time