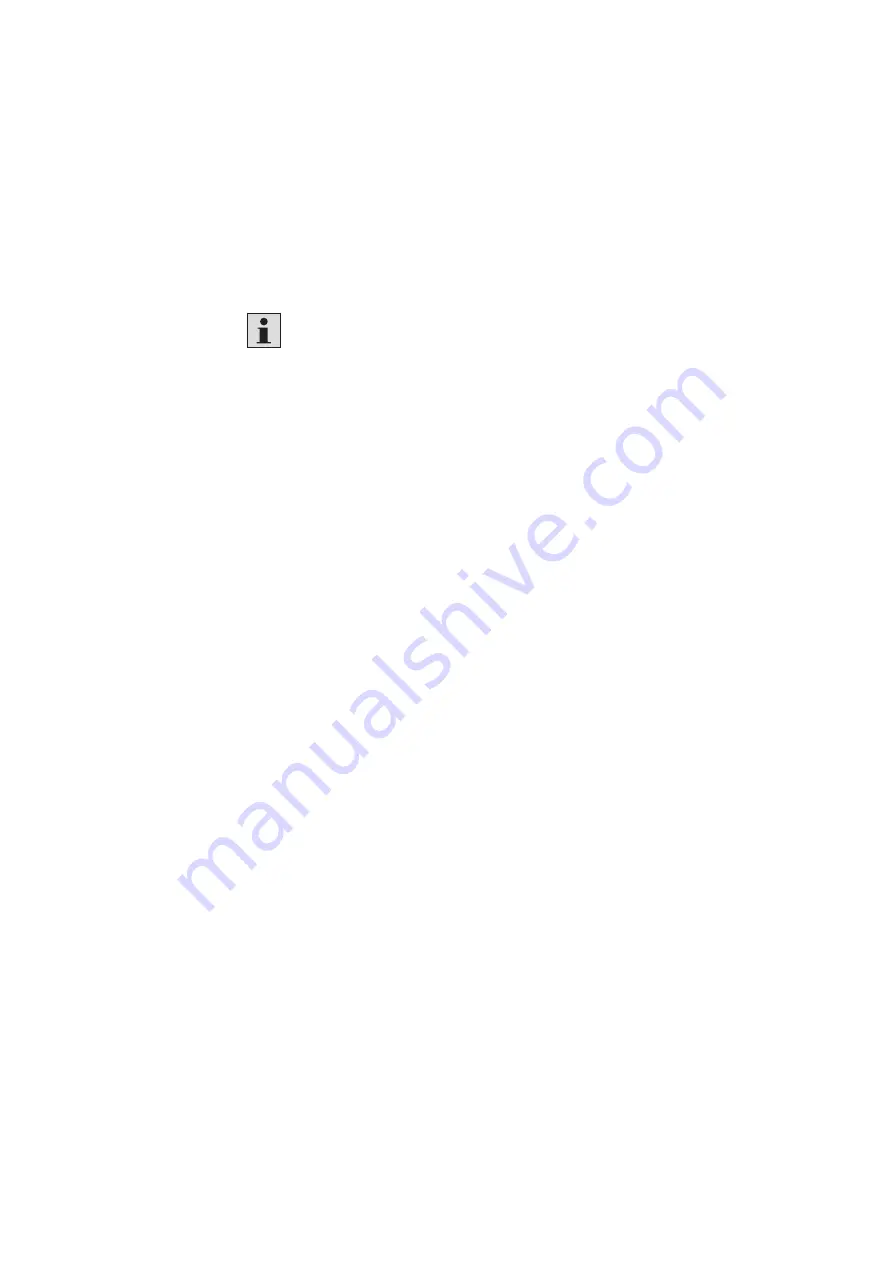
CytroPac, RE 51055-B/02.2021,
Bosch Rexroth AG
53/76
10.5 Maintenance
10.5.1 Checking the electrical components/installation
▶
Have the entire electrical installation regularly checked by a skilled electrician.
▶
Additionally, carry out regular machine and system inspections according to
DIN EN 60204-1 (VDE 0113 part 1) or DIN VDE 0701-0702.
▶
Check the power unit housing, cables and plug-in connections and connector
contacts for damage.
Inadmissible damage includes breaks, cracks, abrasion, deformation or
discoloration. The hydraulic power unit may only be operated when the electrical
components are not damaged.
10.5.2 Fill level monitoring
The fill level is monitored via the integrated fill level sensor with two switching points
(warning and shutdown). In the "Basic" configuration, it must be evaluated by the
machine control, and shutdown of the hydraulic power unit must be ensured if the
level has fallen below the shutdown limit.
1. Expansion due to increase in temperature
(Rough calculation: Delta V = thermal expansion coefficient x delta T)
– Correct the fill level
2. Exceeding of the maximum fill level due to presumed water ingress
– Close water valves (shut off the cooling water supply)
– Take a hydraulic fluid sample from the bottom of the oil tank and check it for
water content
– If water ingress is confirmed, finish the working cycle of the machine and put it
out of operation under safe conditions
– Make additional inspections and take the following measures depending on the
results:
– Eliminate the cause of water ingress
– Clean or drain and change hydraulic fluid
– If necessary, flush the system
– Check the hydraulic fluid for its admissible water content
– Identify and correct the cause of leakage.
– Afterwards, fill in hydraulic fluid to the correct level
Measures if the maximum
fill level is exceeded
Measures if the minimum
fill level is fallen below