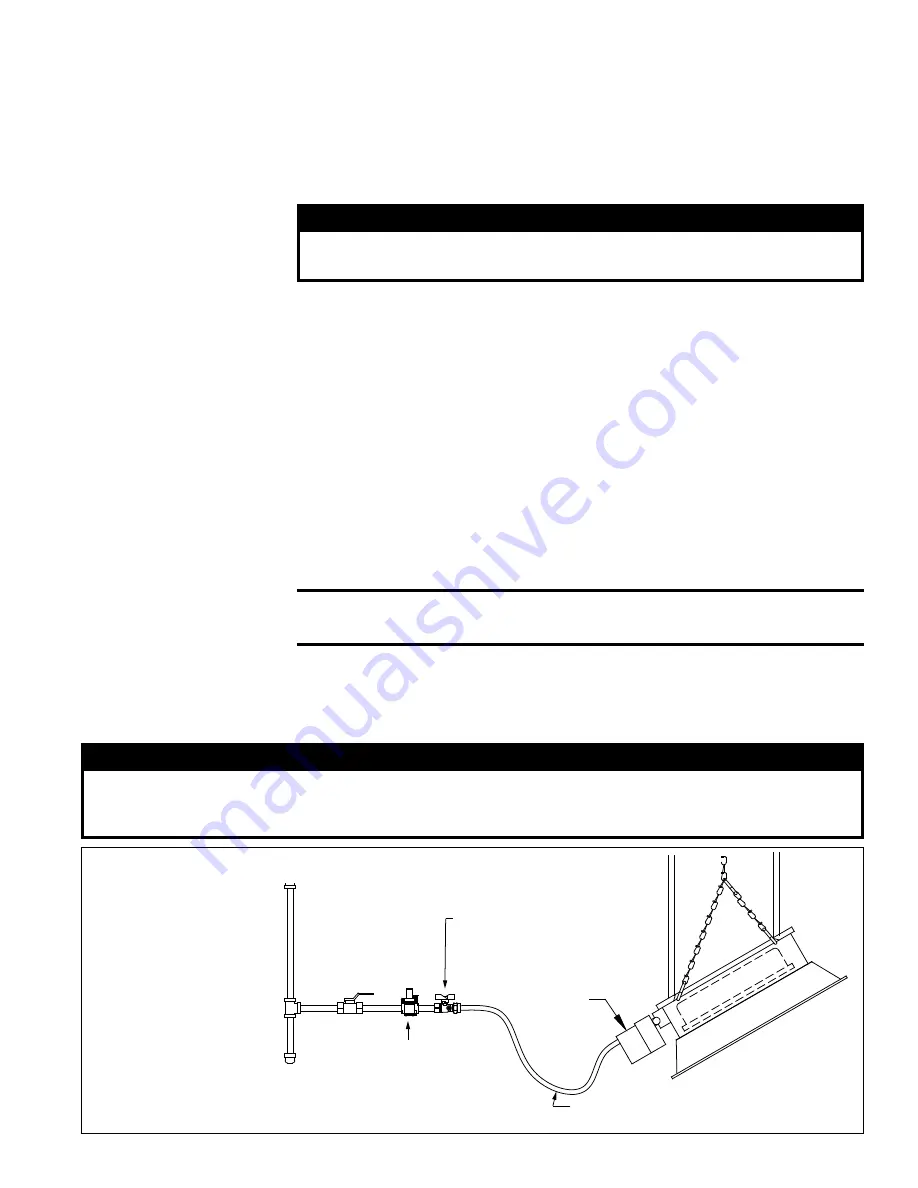
If a heater is located in an aircraft hangar or near overhead doors, it should be rigidly
mounted to prevent swinging.
The installer is responsible for suspension of the heater.
Under no circumstances
should either the gas supply line or electrical supply line to the unit be used to
provide assistance in suspension. Do not run any gas or electric service lines
above or below the heater or near the path of the flue products.
Gas
Supply
6” (15mm)
Drip Leg
Manual
Gas Valve
Pressure regulator
required when supply
pressure exceeds
14” (35cm) w.c.
Gas Cock with plugged
pressure tap
(component
of the agency-approved
flexible connector shown
here)
Agency-approved Flexible Connector
(if permitted by local code)
Gas Valve
with manifold
pressure tap
FIGURE 5 -
Gas Supply
Connections -
All components
upstream of the
gas valve on the
unit are field-
supplied.
6.0 Gas Supply
6.1 Gas Supply Line
(Refer to
FIGURE 6
.)
WARNINGS
DO NOT install any gas piping in heat zones.
DO NOT use gas supply piping to support the heater.
•
All piping must be installed according to local codes. Use new clean pipe. Inspect
and clean out any chips or debris before installing the pipe and fittings.
•
Piping joint compound must be resistant to the action of liquefied petroleum gases.
•
An agency-approved flexible connection between the supply line and the heater
may only be used if permitted by local code. It is recommended that either the
piping or the mounting be flexible to prevent fatigue failure from vibration and/or
thermal expansion.
•
A first-stage pressure regulator is required when gas supply pressure exceeds 14"
(35cm) w.c. If a pressure regulator is required, be sure that it is installed in the gas
line with the arrow indicating gas flow pointing in the proper direction.
•
An over-pressure protection device may be required in some jurisdictions.
•
Install a 6" (152mm) drip-leg trap at the inlet connection.
•
Install a 1/8" (32mm) NPT plugged tap, accessible for text gauge connection
immediately upstream of the gas supply connection to the heater.
•
Do not subject gas pressure regulators, flex connectors, and gas cocks on the
heater to test pressures over 14" w.c. while checking supply piping for leaks.
CAUTION: Isolate the heater from the gas supply line during high
pressure leak testing of gas supply piping.
•
All piping joints must be tested for leaks with a non-corrosive leak detecting
solution.
•
Always use two wrenches when mating pipe connections to the heater. Excessive
torque on the manifold may misalign gas orifices causing heater to malfunction.
•
Purge all gas supply lines of air completely before attempting to ignite the heater.
WARNING
All components of a gas supply system must be leak tested prior to placing equipment
into service. Use a non-corrosive leak detecting solution. Never test for leaks with an open
flame. See Hazard Levels, page 2.
Form I-RIH, P/N 131793R8, Page 9