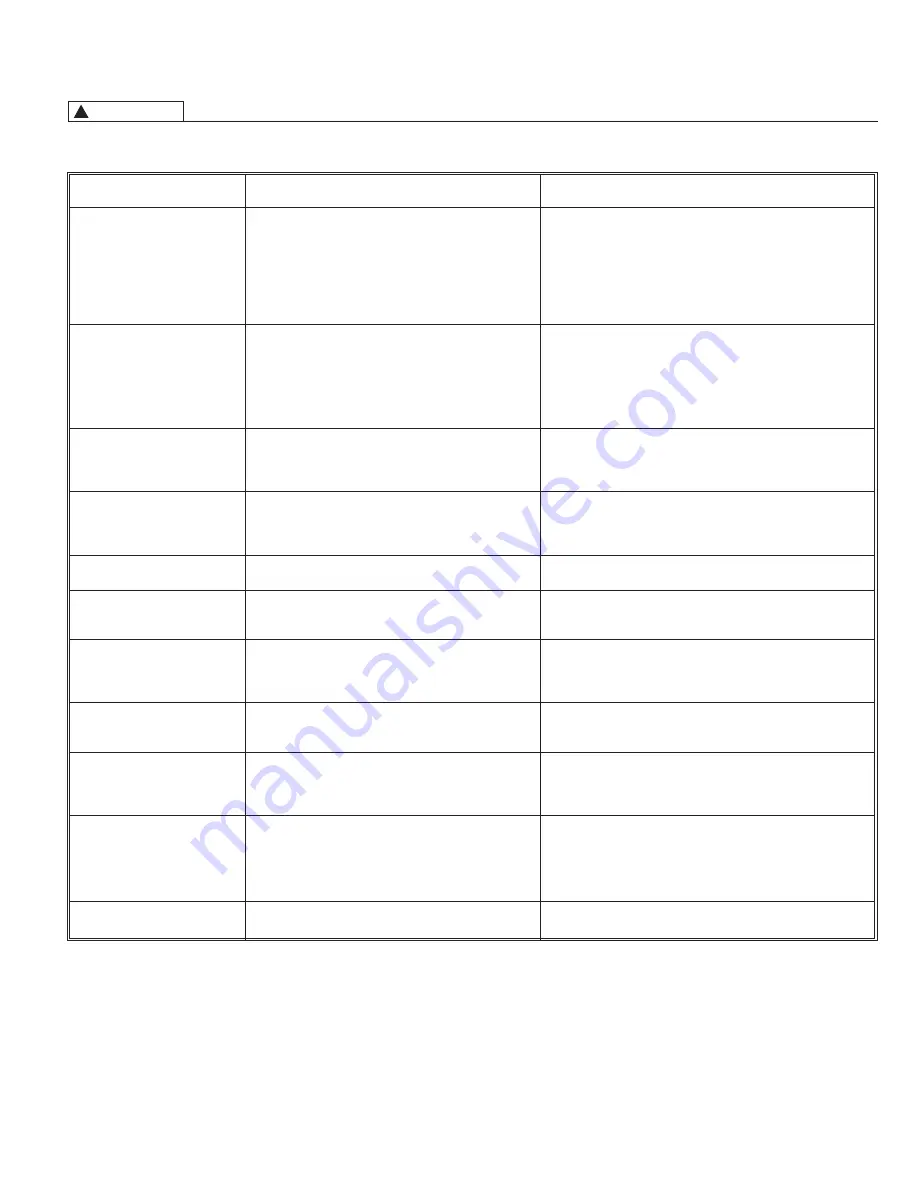
23
SYMPTOM
POSSIBLE CAUSE
REMEDY
Unit will not run
• Power off or loose electrical connection
• Check for correct voltage at contactor in condensing unit
• Thermostat out of calibration-set too high
• Reset
• Defective contactor
• Check for 24 volts at contactor coil - replace if contacts are
open
• Blown fuses / tripped breaker
• Replace fuses / reset breaker
• Transformer defective
• Check wiring-replace transformer
• High pressure control open (if provided)
• Reset-also see high head pressure remedy-The high pressure
control opens at 450 PSIG
Outdoor fan runs, compressor
• Run or start capacitor defective
• Replace
doesn’t
• Start relay defective
• Replace
• Loose connection
• Check for correct voltage at compressor -
check & tighten all connections
• Compressor stuck, grounded or open motor winding,
• Wait at least 2 hours for overload to reset.
open internal overload.
If still open, replace the compressor.
• Low voltage condition
• Add start kit components
Insufficient cooling
• Improperly sized unit
• Recalculate load
• Improper indoor airflow
• Check - should be approximately 400 CFM per ton.
• Incorrect refrigerant charge
• Charge per procedure attached to unit service panel
• Air, non-condensibles or moisture in system
• Recover refrigerant, evacuate & recharge, add filter drier
Compressor short cycles
• Incorrect voltage
• At compressor terminals, voltage must be ± 10% of
nameplate marking when unit is operating.
• Defective overload protector
• Replace - check for correct voltage
• Refrigerant undercharge
• Add refrigerant
Registers sweat
• Low indoor airflow
• Increase speed of blower or reduce restriction - replace air
filter
High head-low vapor pressures
• Restriction in liquid line, expansion device or filter drier
• Remove or replace defective component
• Flowcheck piston size too small
• Change to correct size piston
• Incorrect capillary tubes
• Change coil assembly
High head-high or normal vapor
• Dirty outdoor coil
• Clean coil
pressure - Cooling mode
• Refrigerant overcharge
• Correct system charge
• Outdoor fan not running
• Repair or replace
• Air or non-condensibles in system
• Recover refrigerant, evacuate & recharge
Low head-high vapor pressures
• Flowcheck piston size too large
• Change to correct size piston
• Defective Compressor valves
• Replace compressor
• Incorrect capillary tubes
• Replace coil assembly
Low vapor - cool compressor -
• Low indoor airflow
• Increase speed of blower or reduce restriction - replace air
iced indoor coil
filter
• Operating below 65°F outdoors
• Add Low Ambient Kit
• Moisture in system
• Recover refrigerant - evacuate & recharge - add filter drier
High vapor pressure
• Excessive load
• Recheck load calculation
• Defective compressor
• Replace
Fluctuating head & vapor
•
pressures
• Air or non-condensibles in system
• Recover refrigerant, evacuate & recharge
Gurgle or pulsing noise at
• Air or non-condensibles in system
• Recover refrigerant, evacuate & recharge
expansion device or liquid line
DISCONNECT ALL POWER TO UNIT BEFORE SERVICING. CONTACTOR MAY BREAK ONLY ONE SIDE. FAILURE
TO SHUT OFF POWER CAN CAUSE ELECTRICAL SHOCK RESULTING IN PERSONAL INJURY OR DEATH.
TROUBLE SHOOTING CHART
WARNING
!
• TEV hunting
Check TEV bulb clamp - check air distribution on coil - replace
TEV
Summary of Contents for 018J*Z
Page 24: ...24 FIGURE 4 SINGLE PHASE WIRING DIAGRAM ...
Page 25: ...25 FIGURE 5 THREE PHASE WIRING DIAGRAM C D Y VOLTAGES ...
Page 26: ...26 FIGURE 6 ...
Page 27: ...27 ...
Page 28: ...28 CM 0908 ...