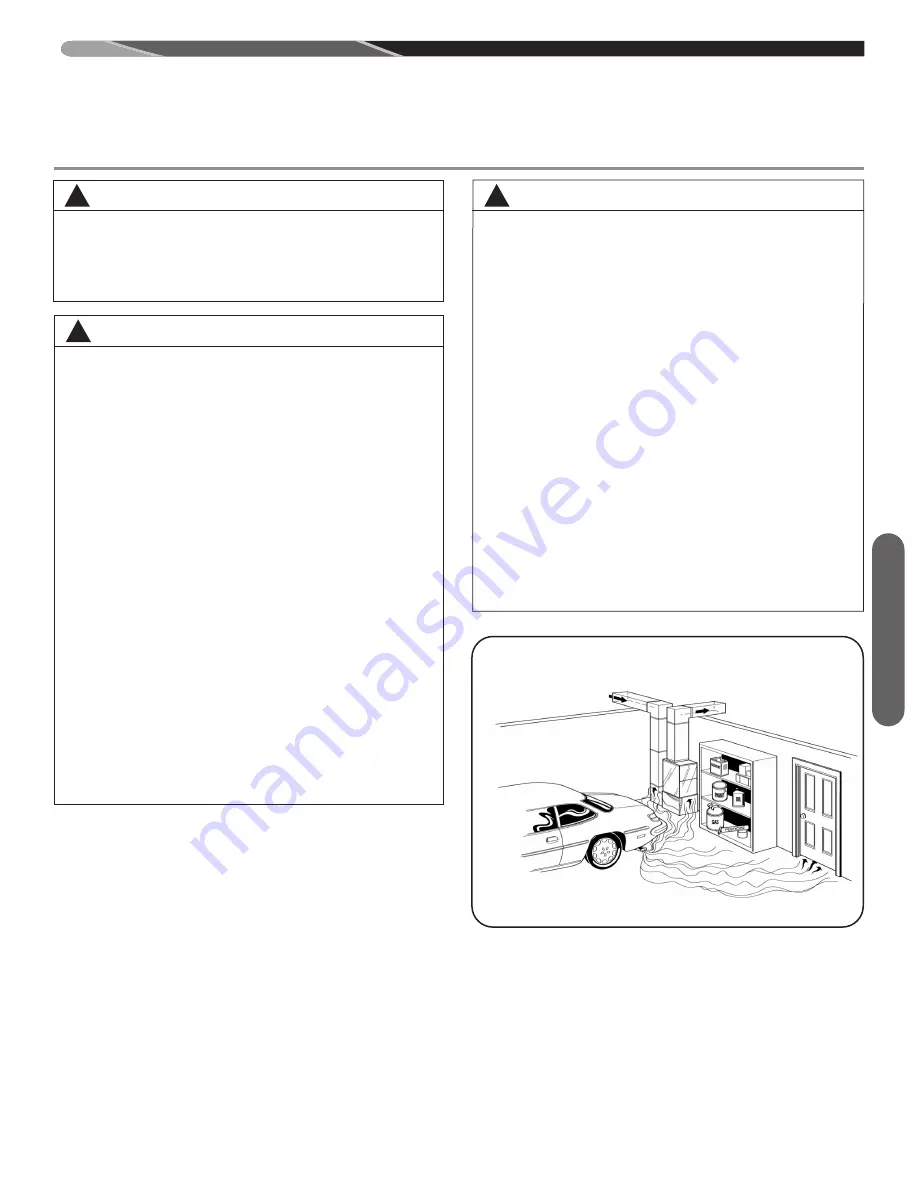
7
SAFETY
Sa
fet
y In
for
m
atio
n
IMPORTANT INFORMATION ABOUT
EFFICIENCY AND INDOOR AIR
QUALITY
Central cooling and heating equipment is only as efficient as the
duct system that carries the cooled or heated air. To maintain effi-
ciency, comfort and good indoor air quality, it is important to have
the proper balance between the air being supplied to each room
and the air returning to the cooling and heating equipment.
Proper balance and sealing of the duct system improves the effi-
ciency of the heating and air conditioning system and improves
the indoor air quality of the home by reducing the amount of air-
borne pollutants that enter homes from spaces where the duct-
work and / or equipment is located. The manufacturer and the
U.S. Environmental Protection Agency’s Energy Star Program
recommend that central duct systems be checked by a qualified
contractor for proper balance and sealing.
FIGURE 2
MIGRATION OF DANGEROUS SUBSTANCES, FUMES, AND ODORS INTO
LIVING SPACES
Adapted from
Residential Duct Diagnostics and Repair
, with permission of Air Conditioning
Contractors of America (ACCA).
!
WARNING
DUCT LEAKS CAN CREATE AN UNBALANCED SYSTEM
AND DRAW POLLUTANTS SUCH AS DIRT, DUST, FUMES
AND ODORS INTO THE HOME CAUSING PROPERTY
DAMAGE. FUMES AND ODORS FROM TOXIC, VOLATILE
OR FLAMMABLE CHEMICALS, AS WELL AS AUTOMO-
BILE EXHAUST AND CARBON MONOXIDE (CO), CAN BE
DRAWN INTO THE LIVING SPACE THROUGH LEAKING
DUCTS AND UNBALANCED DUCT SYSTEMS CAUSING
PERSONAL INJURY OR DEATH (SEE FIGURE 2).
• IF AIR-MOVING EQUIPMENT OR DUCTWORK IS LO-
CATED IN GARAGES OR OFF-GARAGE STORAGE
AREAS - ALL JOINTS, SEAMS, AND OPENINGS IN THE
EQUIPMENT AND DUCT MUST BE SEALED TO LIMIT
THE MIGRATION OF TOXIC FUMES AND ODORS IN-
CLUDING CARBON MONOXIDE FROM MIGRATING
INTO THE LIVING SPACE.
• IF AIR-MOVING EQUIPMENT OR DUCTWORK IS LO-
CATED IN SPACES CONTAINING FUEL BURNING AP-
PLIANCES SUCH AS WATER HEATERS OR BOILERS -
ALL JOINTS, SEAMS, AND OPENINGS IN THE EQUIP-
MENT AND DUCT MUST ALSO BE SEALED TO PRE-
VENT DEPRESSURIZATION OF THE SPACE AND
POSSIBLE MIGRATION OF COMBUSTION BYPROD-
UCTS INCLUDING CARBON MONOXIDE INTO THE LIV-
ING SPACE.
!
WARNING
BLOWER AND BURNERS MUST NEVER BE OPERATED
WITHOUT THE BLOWER DOOR IN PLACE. THIS IS TO
PREVENT DRAWING GAS FUMES (WHICH COULD CON-
TAIN HAZARDOUS CARBON MONOXIDE) INTO THE
HOME THAT COULD RESULT IN PERSONAL INJURY OR
DEATH.
!
WARNING
ALWAYS INSTALL THE FURNACE TO OPERATE WITHIN
THE FURNACE’S INTENDED TEMPERATURE-RISE
RANGE WITH A DUCT SYSTEM WHICH HAS AN EXTER-
NAL STATIC PRESSURE WITHIN THE ALLOWABLE
RANGE, AS SPECIFIED IN THE DUCTING SECTION OF
THESE INSTRUCTIONS. SEE ALSO FURNACE RATING
PLATE.
THE FURNACE MAY BE USED FOR HEATING OF BUILD-
INGS OR STRUCTURES UNDER CONSTRUCTION.
INSTALLATION MUST COMPLY WITH ALL INSTALLATION
INSTRUCTIONS INCLUDING:
PROPER VENT INSTALLATION;
-
FURNACE OPERATING UNDER THERMOSTAT
-
CONTROL;
RETURN AIR DUCT SEALED TO THE FURNACE;
-
AIR FILTERS IN PLACE;
-
SET FURNACE INPUT RATE AND TEMPERATURE
-
RISE PER RATING PLATE MARKINGS;
MEANS FOR PROVIDING OUTDOOR AIR RE-
-
QUIRED FOR COMBUSTION;
RETURN AIR TEMPERATURE MAINTAINED BE-
-
TWEEN 55°F (13°C) AND 80°F (27°C); AND
CLEAN FURNACE, DUCT WORK AND COMPO-
-
NENTS UPON SUBSTANTIAL COMPLETION OF
THE CONSTRUCTION PROCESS, AND VERIFY
THAT THE FURNACE OPERATING CONDITIONS
INCLUDING IGNITION, INPUT RATE, TEMPERA-
TURE RISE AND VENTING, ACCORDING TO THE
INSTRUCTIONS AND CODES.
Summary of Contents for (-)(-)80MSX050A30SA
Page 52: ...52 CM 0814 ...