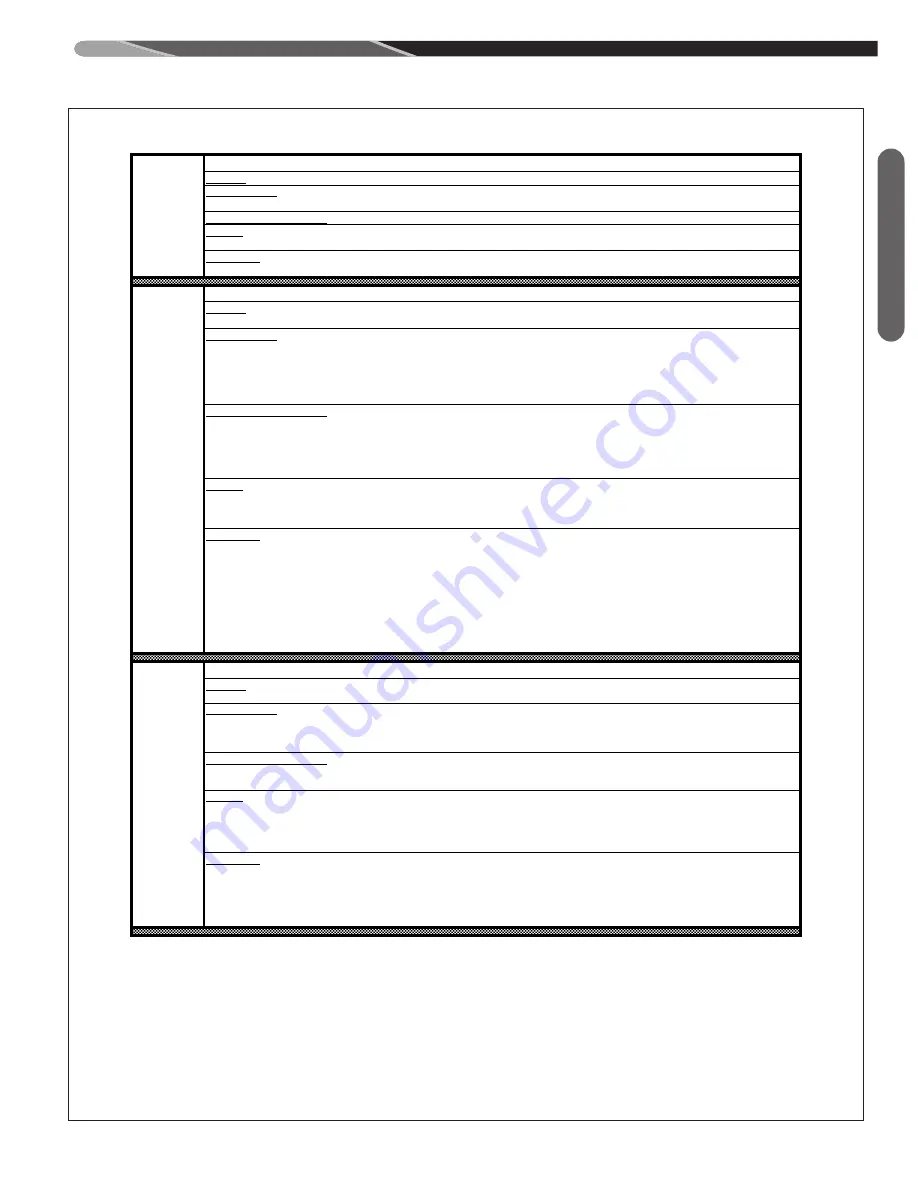
99
TABLE 19 (continued)
R97V FAULT CODES WITH DESCRIPTIONS AND SOLUTIONS
44
LOW PRESSURE SWITCH CLOSED, INDUCER OFF
STATUS:
This is a critical fault. The furnace will not operate in gas heat modes but all other modes (e.g. cooling) should
function if present simultaneously with a heating call (e.g. defrost call in dual-fuel mode).
DESCRIPTION:
The low pressure control (or switch) should not be closed when the inducer is not running. If it is, this is a sign
of a serious condition. The switch may be welded closed or purposely bypassed in the field. Before any heat cycle can begin,
the pressure switch is tested to make sure that it is opened. The switch is ignored except in gas heating modes.
(3) Check wiring and connections. Replace and/or repair as necessary.
CAUSE:
(1) Faulty switch.
(3) Loose or faulty wiring.
(4) Abnormally high negative pressure present on vent system without inducer running.
SOLUTION:
(1) Insufficient venting through either the inlet or exhaust.
(2) Check wiring and connections. Replace and/or repair as necessary.
OVER-TEMPERATURE SWITCH (ROLL-OUT) OPEN
STATUS:
This is a critical fault. The furnace will not operate in gas heat modes but all other modes (e.g. cooling) should
function.
DESCRIPTION:
The Manually Reset Limit Control (M.R.L.C.) is also known by the name "Rollout Limit". There can be several
on any given furnace. When one or more of these limits open, they must be manually pushed back to the closed position
(hence the name;
Manually
Reset) to force the acknowledgement of a critical fault. This fault will occur when flames have rolled
out of the normal area in the heat exchanger and into the burner compartment. This fault should rarely (if ever) be seen in the
field and indicates a very serious problem that must be repaired before furnace operation can continue.
(1) Check that the pressure switch(es) have not been welded closed or bypassed. Check that the inducer is operating at the
proper rpm. Insure that the venting does not exceed the maximum specified lengths. Check for obstructions in combustion
venting. Check that all gaskets between the inducer and center panel / heat exchanger are properly installed and sealed.
(3) Unstable flame pattern.
CAUSE:
(2) Loose or faulty wiring.
SOLUTION:
(1) Replace low pressure control (switch).
(4) Check for proper venting and terminations as defined in the furnace installation instructions.
33
(3) Check that all burner assembly components are properly installed. Check that all seals between the burner and blower
compartments are tight. Insure that the door seals are in place and that the burner door is properly installed and does not leak.
Check to make sure that the heat exchanger has not been damaged; i.e.: crushed tubes, breached collector box and etc.
SOLUTION:
Repair the short circuit condition and replace fuse.
(2) Pressure switch physically bypassed in the field.
(2) Remove bypass and restore correct operation. Determine reason for bypass (e.g. vent length too long) and correct issue.
Notify homeowner and proper authorities of illeagle tampering if necessary.
30
DESCRIPTION:
The fuse has been opened. This usually occurs when there is a 24VAC short to common or ground on the low-
votage side of the transformer.
EXPECTED OPERATION:
The fault code is displayed and no other operation can take place.
CAUSE:
An electrical short from low voltage (24VAC) to ground or common has occurred.
OPEN FUSE
STATUS:
This is a critical fault. The furnace will not operate in any mode.
EXPECTED OPERATION:
When the MRLC (Manually Reset Limit Control) circuit has been opened, the IBM (Indoor Blower
Motor) is energized at maximum heating speed. The gas valve circuit is de-energized (if it was energized) and the IDM (Induced
Draft Motor) is energized at high speed. Response to thermostat cooling calls will take place as normal with IBM energizing at
the higher of the two blower speeds (high heat or cool) when a call for cooling is also present. When the fault is cleared, the
IDM will remain energized for a 20 second post-purge and the IBM will remain energized for the user-selected blower off-delay
period.
EXPECTED OPERATION:
There will be no other operation than displaying of the fault code and diagnostic messages to the
homeowner and technician. The fault code is only present during a heat call
before
pre-purge begins.
Dia
gn
ost
ics