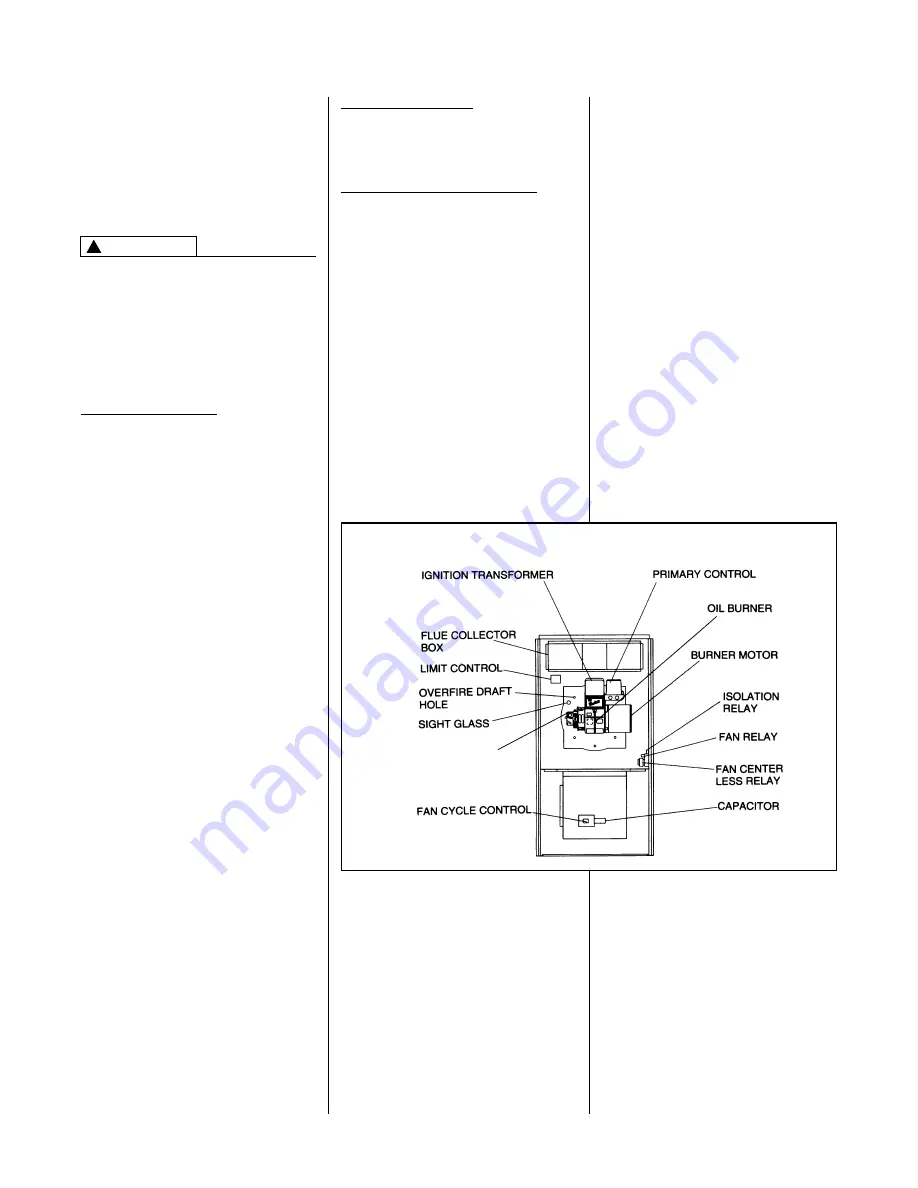
LIGHTING INSTRUCTIONS
This appliance is equipped with an
automatic electronic ignition device.
This device lights the oil burner each
time the room thermostat (closes) calls
for heat. See oil burner instructions
enclosed with furnace for further detail.
MAKE SURE THAT COMBUSTION
CHAMBER IS FREE OF OIL BEFORE
USING RESET BUTTON ON
PRIMARY CONTROL. FAILURE TO
DO SO CAN CAUSE FLASH FIRE OR
EXPLOSION RESULTING IN
PROPERTY DAMAGE, PERSONAL
INJURY OR DEATH.
TO START FURNACE
1. Set room thermostat to highest
setting.
2. Open shut-off valve in oil supply line.
3. Close line switch. Burner should
start automatically.
4. Bleed the fuel pump as soon as the
burner motor starts rotating. To
bleed the fuel unit, attach a clear
plastic hose over the bleed plug.
Loosen the plug and catch the oil in
an empty container. Tighten the plug
when all air is purged.
5. Reset room thermostat to desired
temperature setting.
11
WARNING
!
TO STOP FURNACE
1. Set the room thermostat to lowest
temperature setting.
2. Turn “Off” line switch to the furnace.
IF BURNER DOES NOT START
1. Check fuse or breaker in the furnace
circuit.
2. Assure room thermostat is set above
room temperature.
3. Check oil level in the tank.
4. Make sure that oil line shut-off
valves are open.
5. Wait five minutes to allow the control
to cool, so that it will recycle. Reset
the button on the primary control.
6. Depress manual reset button on the
motor.
NOTE: Do not expose cad cell to
direct electric bulb light or sunlight.
Light may enter through the air control
band slot and upset the electric circuit
of this device.
OPERATING INSTRUCTIONS
FIGURE 11. COMPONENT LOCATION
I421
OIL PROP
Summary of Contents for LX2000 Series
Page 27: ...27 PARALLEL WIRING UPFLOW OIL FURNACES SCHEMATIC...
Page 28: ...28 HEATING AND COOLING CONTINUOUS LOW SPEED BLOWER SCHEMATICFIGURE 38...
Page 29: ...29 FIGURE 38 FOR MODELS WITH UTEC 1012 925 INTEGRATED FURNACE CONTROL...
Page 30: ...30...
Page 31: ...31...
Page 32: ...32 CM 898...