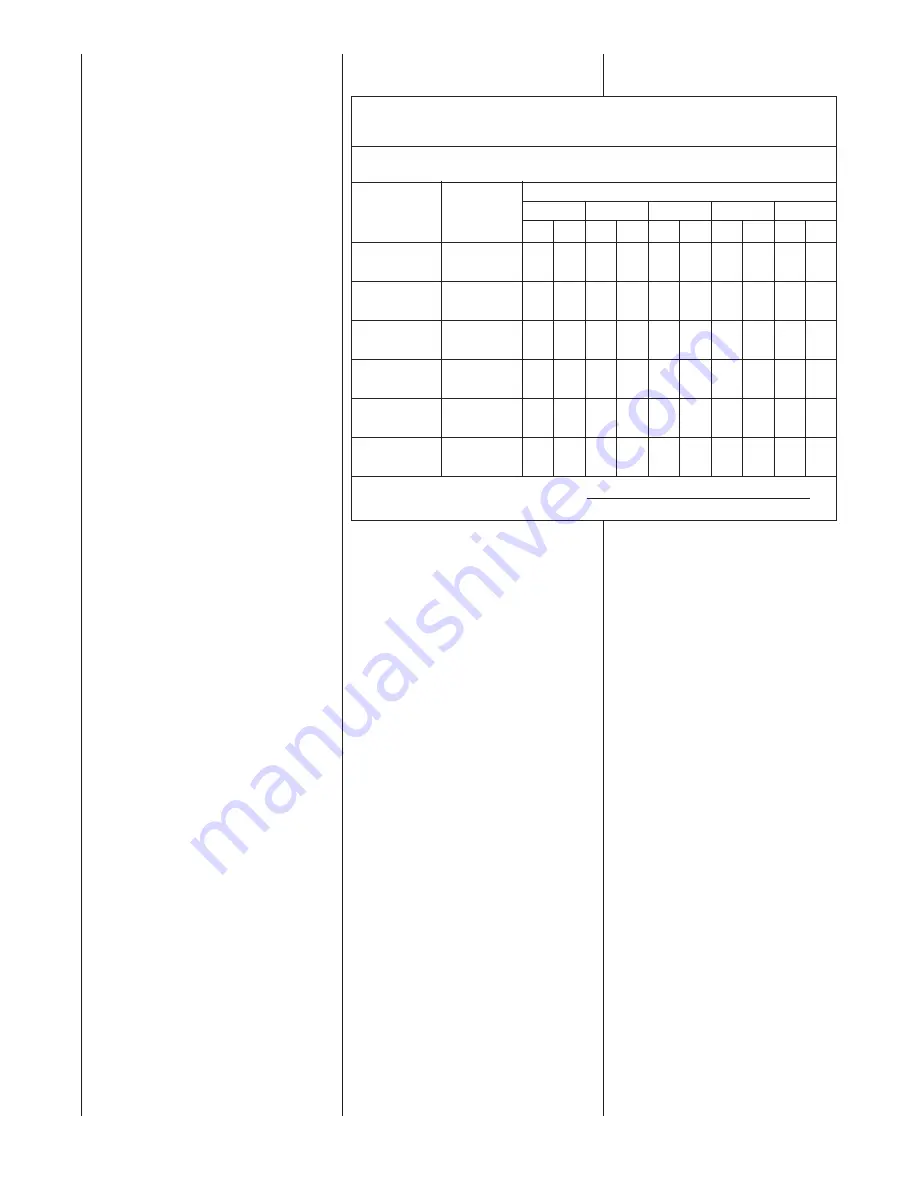
53
ADJUSTING OR CHECKING
FURNACE INPUT
A properly calibrated manometer or
gauge is required for accurate gas
pressure readings.
NATURAL GAS
1. When adjusting the furnace input,
the high fire input should be
checked. The high fire manifold
pressure should be 3.5’ W.C.
Follow these steps to be sure the
furnace is high fire mode:
a. With a single stage thermostat, the
furnace runs for 12 minutes on low
fire before shifting to high fire. To
be certain that it is on high fire,
jump terminals “W” and “W2” on
the control board in the blower
compartment.
b. With a two stage thermostat, set
the thermostat to its highest setting
to keep the furnace operating in the
high fire mode.
2. To adjust high fire manifold
pressure, remove the adjustment
cover screw on the outlet end of
the gas valve and turn the
adjustment screw clockwise to
increase the pressure and
counterclockwise to reduce the
pressure. Replace the cover screw
securely. See Figure 38.
3. The low fire manifold pressure
should be 1.7” W.C. As mentioned
above, the furnace remains in the
low fire mode for 12 minutes upon
a heat call with a single stage
thermostat. With a two stage
thermostat, disconnect the
thermostat lead to the “W2”
terminal on the IFC and the furnace
will remain in the low fire mode. To
adjust the pressure, remove the
regulator cover, on top of the valve,
and adjust as noted under Step 2,
above. After the adjustment
replace the screw cover securely.
NOTE:
Use a 3/32” allen wrench or
small-blade screwdriver for making
the pressure adjustment.
LP GAS
On furnaces using LP gas, the LP gas
supply pressure must be set between
11.0" and 13.0" W.C. by means of the
tank or branch supply regulators. Set
the furnace manifold pressure at 10"
W.C. on high fire and 4.8" W.C. on
low fire at the gas control valve. For
elevations up to 8,000 feet, rating
plate inputs apply. For high altitudes
(elevations 5,000 ft. and over), the
orifice spud must be changed.
SETTING INPUT RATE
The furnace is shipped from the
factory with #50 orifices. With -278
option code, furnaces will be shipped
with #51 orifice for elevations of 5000
ft. They are sized for natural gas
having a heating value of 1075
BTU/cu. ft. and a specific gravity of
.60.
Since heating values vary geo-
graphically, the manifold pressure
and/or gas orifice size may need to
be changed to adjust the furnace to
its nameplate input. Consult the local
gas utility to obtain the yearly average
heating value and orifice size required
to fire each individual burner at
15,000 BTU/HR.
Proper input is important to prevent
over firing of the furnace beyond its
design-rated input.
NEVER SET
INPUT ABOVE THAT SHOWN ON
THE RATING PLATE.
To check furnace input:
1. Make certain that all other gas
appliances are shut off, with the
exception of pilot burners.
2. Start the furnace
3. Time the meter to measure the
time required to burn one cubic foot
of gas. See Table 14.
TABLE 14
METER TIME
METER TIME IN MINUTES AND SECONDS FOR NORMAL INPUT RATING OF FURNACES
EQUIPPED FOR NATURAL OR LP GAS
HEATING VALUE OF GAS BTU PER CU. FT.
METER
900
1000
1040
1100
2500 (LP)
INPUT
SIZE
BTU/HR
CU. FT.
MIN.
SEC.
MIN.
SEC.
MIN.
SEC.
MIN.
SEC.
MIN.
SEC.
ONE
1
12
1
20
1
23
1
28
3
20
45,000
TEN
12
0
13
20
13
50
14
40
33
20
ONE
0
54
1
0
1
3
1
6
2
30
60,000
TEN
9
0
10
0
10
24
11
0
25
0
ONE
0
44
0
48
0
50
0
53
2
0
75,000
TEN
7
12
8
0
8
19
8
48
20
0
ONE
0
36
0
40
0
42
0
44
1
40
90,000
TEN
6
0
6
40
7
0
7
20
16
40
ONE
0
31
0
34
0
36
0
38
1
26
105,000
TEN
5
10
5
40
6
0
6
20
14
20
ONE
0
27
0
30
0
31
0
33
1
15
120,000
TEN
4
30
5
0
5
10
5
30
12
30
Heating Value of Gas (BTU/FT
3
) x 3600 x correction factor
Formula: Input BTU/HR =
Time in Seconds (for 1 cu. ft.) of Gas
Summary of Contents for RGRK SERIES
Page 41: ...41 FIGURE 39 TYPICAL MANIFOLD PRESSURE READING...
Page 45: ...45 FIGURE 43 UT Electronic Controls 1095 201 IFC TWINNING CONNECTION SINGLE STAGE OPERATION...
Page 60: ...60 FIGURE 53 TROUBLESHOOTING CHART or IFC not properly grounded Go To Next Page...
Page 61: ...61 FIGURE 53 TROUBLESHOOTING CHART CONTINUED...
Page 62: ...62 FIGURE 54 WIRING DIAGRAM...
Page 63: ...63...
Page 64: ...64 CM 0510...