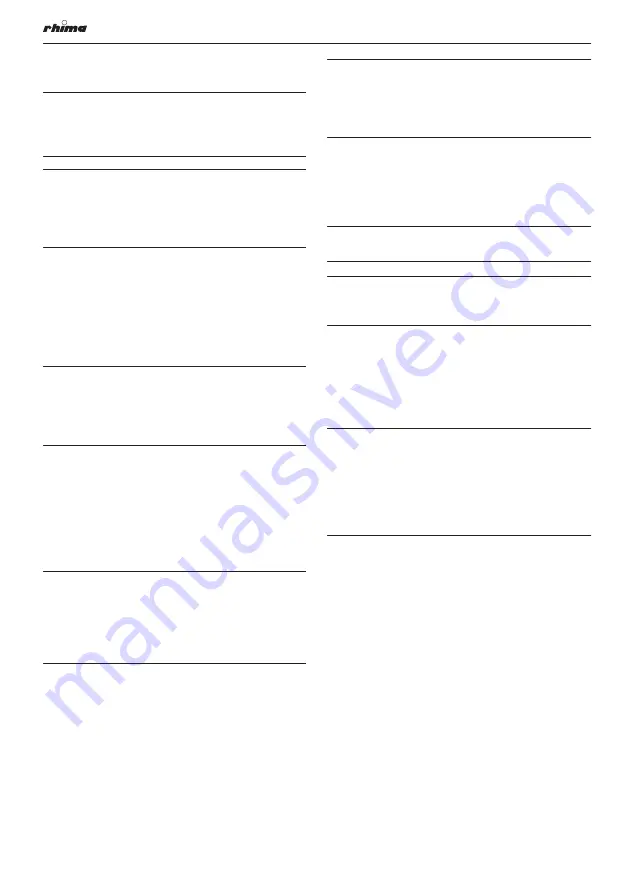
Operative Instructions
28
observance of what is reported in this manual.
a
WARNING! The bedpan washer maintenance
operations must be carried out with the
machine completely switched off (turn off
the main circuit breaker).
a
WARNING!
To
prevent
bacterial
proliferation, the machine is equipped
with a Self Disinfection System (S.D.S.)
that automatically perform a disinfection
program 24 hours after the last cycle.
The routine maintenance operations and the frequency
of maintenance are described in the Maintenance
Logbook.
The Maintenance Logbook is an integral part of this
manual. If the Maintenance Logbook is missing, contact
your dealer or distributor.
a
WARNING
! it is the user's obligation to
fill in and keep updated the Maintenance
Logbook. The incorrect or incomplete
compilation of the Maintenance Logbook
will void the warranty.
9.1.1 Periodic maintenance request
After a certain time or a certain number of operating
hours, the display shows «MAINTENANCE», if enable.
This signal has no influence on the machine operation,
contact the customer service or the dedicated technical
assistance for periodic maintenance.
a
WARNING! Periodic maintenance is carried
out by the technician under guarantee only if
the uilizer has correctly and regularly carried
out all ordinary maintenance operations and
if the uilizer has filled out and kept up-to-
date the Maintenance Logbook.
9.1.2 Personal Protective Equipment (PPE)
The operator engaged in this type of intervention must
wear PPE and must be sure that no other unauthorised
person is present in the operating area of the machine.
Before maintenance, start a program to wash the
washing chamber.
9.1.3 Cleaning products
Clean the outside of the machine with products
suitable for stainless steel, glass and plastic materials.
b
HAZARD!
Products
unsuitable
for
cleaning stainless steel, glass and plastic
materials may irreparably damage non-
interchangeable parts of the appliance and
render the machine unusable.
If a suitable cleaning liquid is not available, a mixture of
water (75%) and alcohol (25%) may be used. Cleaning
should be carried out with a smooth (non-scratchy)
cloth moistened with the appropriate liquid.
a
WARNING! Do not spray the machine or near
it with water jets, or with pressure devices.
c
HAZARD! DO NOT SOAK THE CLOTH
to prevent excess liquid from entering
electrically hazardous areas for the operator.
The keypad and display should be cleaned with a
mixture of water and alcohol or with mild detergents.
The washing chamber is automatically cleaned. In case
of need, for an extra cleaning of the washing chamber,
run a rinse cycle without introducing instruments.
a
WARNING! Do not use steel wool, steel
brushes, bleach (bleach cause the oxidation
of the stainless steel surface and consequent
change of color) or any cleaning agent
containing bleach or anything abrasive to
cleaning the device. Doing so will damage
the device!
9.2 Weekly checks
9.2.1 Anti-scale
Periodically check the level of anti-scale product
contained in the drum located in the compartment
below the wash basin. A label near the cap indicates
the type of liquid contained in the drum. A message
on the display warns when the liquid is getting low and
when it is totally finished.
Moreover, the machine has a volumetric meter, which
controls the quantity of passing liquid. This is another
control system: the meter stops the working cycle
and the display will show an alarm every time that
the dispenser pump doesn’t work well or the liquid is
totally finished.
9.2.2 Detergent
Periodically check the level of detergent liquid
contained in the drum (when present) located in the
compartment below the wash basin. A label near the
Summary of Contents for DVS
Page 40: ...Operative Instructions 40 Notes ...
Page 41: ...Operative Instructions 41 Notes ...