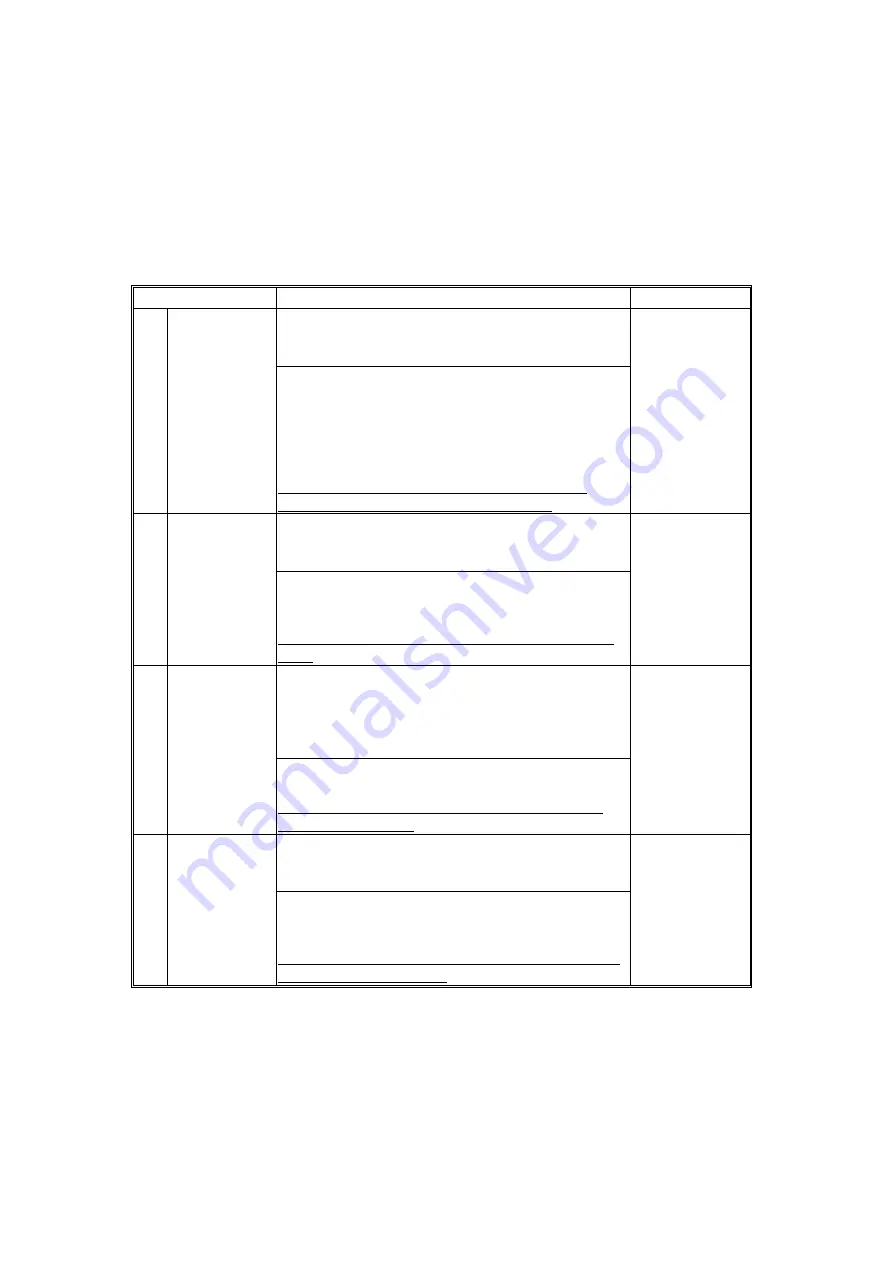
2.5 SERVICE PROGRAM MODE TABLE
1. In the
Function column, comments (extra information) are in italics.
2. In the
Settings column, the default value is printed in bold letters.
3. If there is a
✝
mark in the Mode No. column, copies can be made within
this SP Mode.
Mode No.
Function
Settings
4
Forced Start
(Free Run)
Performs a free run with a forced start.
Press the
key to start the free tun.
Press the
key to stop the free run.
If this mode is switched on, the copier starts the free
run even if the fusing temperature has not reached
the required value yet.
This mode is performed with the selected paper size
and magnification ratio without the paper feed clutch
or total counter increment.
Normally, use SP7 to prevent fusing-related
service call conditions from occurring.
5
Free Run with
Exposure
Lamp Off
A free run is performed without exposure.
Press the
key to start the free run.
Press the
key to stop the free run.
This mode is performed with the selected paper size
and magnification ratio without the paper feed clutch
or total counter increment.
Normally, use SP7 to reduce the cleaning blade
load.
6
Misfeed
Detection Off
✝
Copies are made without misfeed detection by the
registration, exit sensors, and sorter paper sensor.
Press the
key to make a copy. It stops when
reaching the set count, or when the
key is
pressed.
Use this mode to check whether a paper misfeed
was caused by a sensor malfunction.
The total counter increments when copies are
made in this mode.
7
Free Run
Performs a free run with the exposure lamp on.
Press the
key to start the free run.
Press the
key to stop the free run.
This mode is performed with the selected paper size
and magnification ratio without the paper feed clutch
or total counter increment.
Before starting, close the platen cover to reduce
the cleaning blade load.
PROGRAM MODES
20 December 1996
4-10
Summary of Contents for FT 4015
Page 2: ...SECTION 1 OVERALL MACHINE INFORMATION...
Page 14: ...SECTION 2 DETAILED DESCRIPTIONS...
Page 71: ...SECTION 3 INSTALLATION...
Page 90: ...SECTION 4 SERVICE TABLES...
Page 118: ...SECTION 5 PREVENTIVE MAINTENANCE...
Page 126: ...SECTION 6 REPLACEMENT AND ADJUSTMENT...
Page 190: ...SECTION 7 TROUBLESHOOTING...
Page 222: ...SECTION 8 OPTIONS...
Page 223: ...SECTION 9 APPENDIX TIMING CHART...
Page 225: ...COPIER A219 ELECTRICAL COMPONENT LAYOUT 4 2 3 1 5 6 A219S500 wmf...
Page 226: ...10 15 14 13 12 11 9 8 7 18 17 16 A219S501 wmf...
Page 227: ...24 40 23 28 27 26 25 19 20 21 22 29 39 31 32 33 34 35 36 38 37 30 A219S502 wmf...