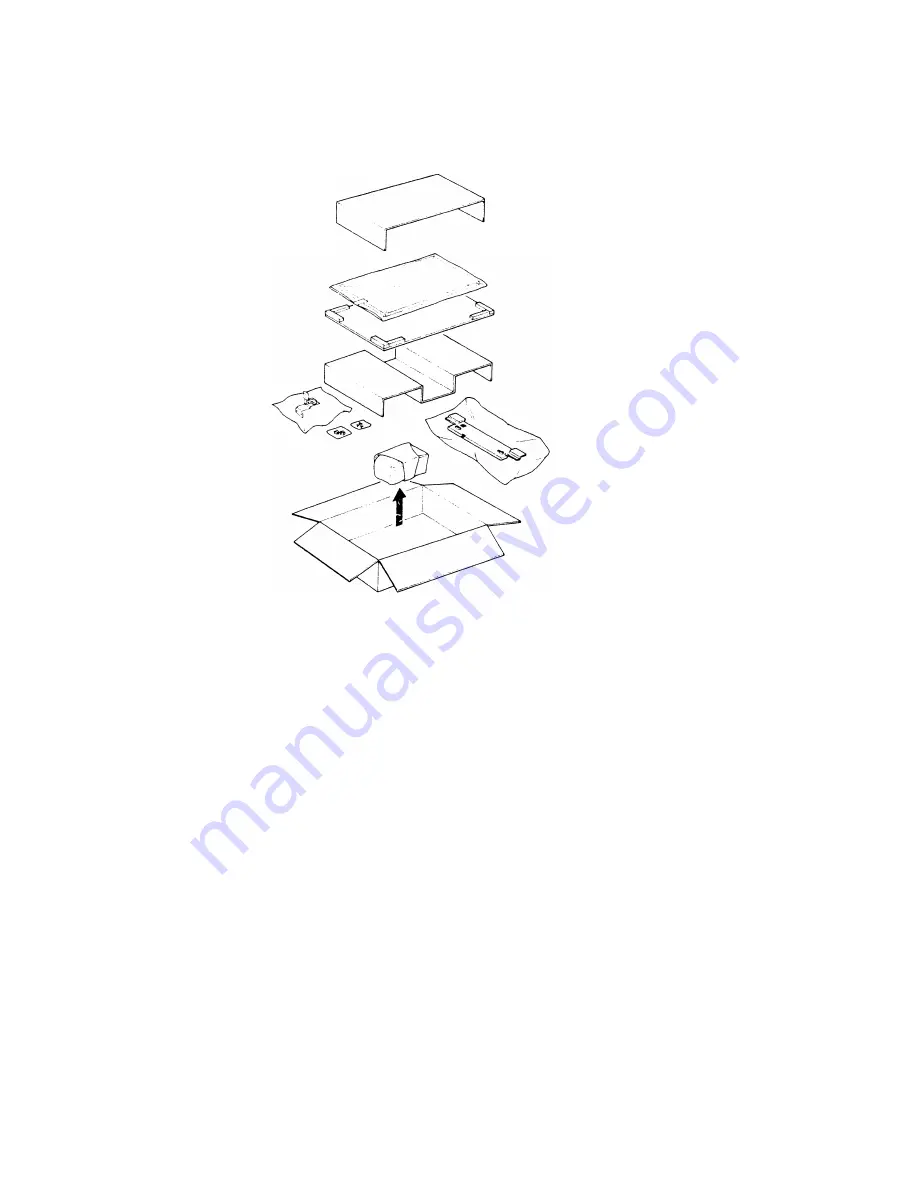
16 April ’88
2. Installation Set for RE 11
The installation set is required when using the editor as a pressure plate.
Open the box and check the parts according to following list:
1
●
2 .
3 .
4,
5.
6
7,
8,
Pressure Sheet
1
Left Hinge
1
Right Hinge
1
Pan Head Screw (M4
x 12)
12
Harness Clamp
2
Hinge Bracket (FT5560, - 115V only)
1
Mounting Stud (FT5560. - 115V only)
2
Pan Head Screw with Washer (M3 x 6)
2
(FT5560, - 115V only) ‘ ‘
NOTE: When installing the editor on this copier, the optional erase lamp
(Editing Interface Adapter Type A) is required..
10-2
Summary of Contents for FT4430
Page 1: ...RICOH FT4430 S E R V I C E M A N U A L RICOH COMPANY LTD...
Page 2: ...SECTION 1 OVERALL MACHINE INFORMATION...
Page 3: ...Table of Contents SPECIFICATIONS OPERATION PANEL SECTION A SECTION B...
Page 11: ......
Page 12: ......
Page 17: ...16 April 88 ELECTRICAL COMPONENT LAYOUT 1 14...
Page 25: ...SECTION 2 DETAILED SECTION DESCRIPTIONS...
Page 103: ...SECTION 3 INSTALLATION...
Page 123: ...SECTION 4 SERVICE TABLES...
Page 133: ...16 April 88 SERVICE PROGRAM MODE TABLE 4 8...
Page 134: ...16 April 88 4 9...
Page 135: ...16 April 88 4 10...
Page 145: ...SECTION 5 REPLACEMENT AND ADJUSTMENT...
Page 225: ...SECTION 7 DOCUMENT FEEDER...
Page 263: ...SECTION 8 SORTER...
Page 281: ...SORTER CONTROL BOARD SCHEMATIC IOOV AC s 1 0 2 1 b 4 16 April 88 A024...
Page 282: ...SECTION 9 LARGE CAPACITY TRAT...
Page 301: ...SECTION 10 EDITOR BOARD...
Page 302: ...CONTENTS...
Page 312: ...SECTION 11 TROUBLESHOOTING...
Page 344: ...RICOH FT4430 A024 P A R T S C A T A L O G First Edition April 1988 RICOH COMPANY LTD...
Page 346: ...1 EXTERIOR A024 April 30 88 2...
Page 349: ...2 REGISTRATION A024 April 30 88...
Page 351: ...3 PLATEN COVER AND CASSETTE A024 April 30 88...
Page 353: ...4 PAPER FEED A024 April 30 88 8...
Page 357: ...5 OPERATION PANEL A024 10 April 30 88...
Page 359: ...6 FRAME A024 April 30 88 12...
Page 361: ...7 OPTICS 1 A024 April 30 88...
Page 363: ...8 OPTICS 2 A024 April 30 88 16 1...
Page 365: ...9 AROUND DRUM A024 April 30 88 18...
Page 368: ...10 35 CLEANING UNIT A024 April 30 88 20...
Page 370: ...11 DEVELOPMENT UNIT A024 April 30 88 22...
Page 373: ...I April 30 88 24...
Page 375: ...13 PAPER TRANSPORT A024 April 30 88 26...
Page 377: ...14 FUSING UNIT A024 April 30 88 28...
Page 380: ...15 PAPER EXIT A024 April 30 88 10 6 30...
Page 382: ...16 ELECTRICAL SECTION 1 A024 April 30 88 32...
Page 384: ...17 ELECTRICAL SECTION 2 A024 April 30 88...
Page 386: ...INDEX NO SYMBOL NO...
Page 387: ......
Page 390: ...19 FUSING LAMP DRIVE BOARD A024 April 30 88 38...
Page 396: ...22 AC MAIN HARNES A024 April 30 88 113 118 103 44...
Page 398: ...23 DC MAIN HARNESS A024...
Page 400: ...24 FUSING UNIT HARNESS A024 2 101 104 April 30 88...
Page 402: ...25 COUNTER HARNESS A024 50...
Page 405: ...26 HARNESS PAPER FEED A024 1 J 52...
Page 407: ...27 SPECIAL TOOL A024 April 30 88...
Page 409: ...28 DECAL AND DOCUMENT April 30 88...
Page 410: ...o BI 12 15 8 1 6 WARNING HIGH TEMP 9...
Page 412: ...DF 39 A419...
Page 414: ...1 DOCUMENT FEEDER I A419 April 30 88 2...
Page 417: ...2 DOCUMENT FEEDER II A419 April 30 88 4...
Page 420: ...3 DOCUMENT FEEDER Ill A419 April 30 88 6...
Page 425: ...5 DF HARNESS A419 April 30 88 10...
Page 427: ...CS 2070 A414...
Page 428: ...1 Mini Sorter A414 2 2 Bin Motor Board A414 4 3 Sorter Harness A414 6 Parts lndex 9...
Page 429: ...1 MINI SORTER A414 April 30 88 2...
Page 434: ...RT 15 A912...
Page 436: ...1 LCT I A912 April 30 88...
Page 438: ...2 LCT II A912 4...
Page 440: ...3 LCT Ill A912 April 30 88...
Page 442: ...3 SORTER HARNESS A414 April 30 88 120 115...
Page 447: ...5 LCT HARNESS A912 April 30 88 110 122 10...
Page 449: ...RE 11 A906...
Page 450: ......
Page 451: ...1 RE 11 A906 April 30 88 2 5 2 4 _ _ _ 2...
Page 453: ...PARTS INDEX...
Page 456: ...INTERFACE BOARD TYPE E A426...
Page 457: ...1 interface Board A426 2 Parts Index 5...
Page 460: ...PARTS INDEX...
Page 462: ...SORTER ADAPTER TYPE E A918...