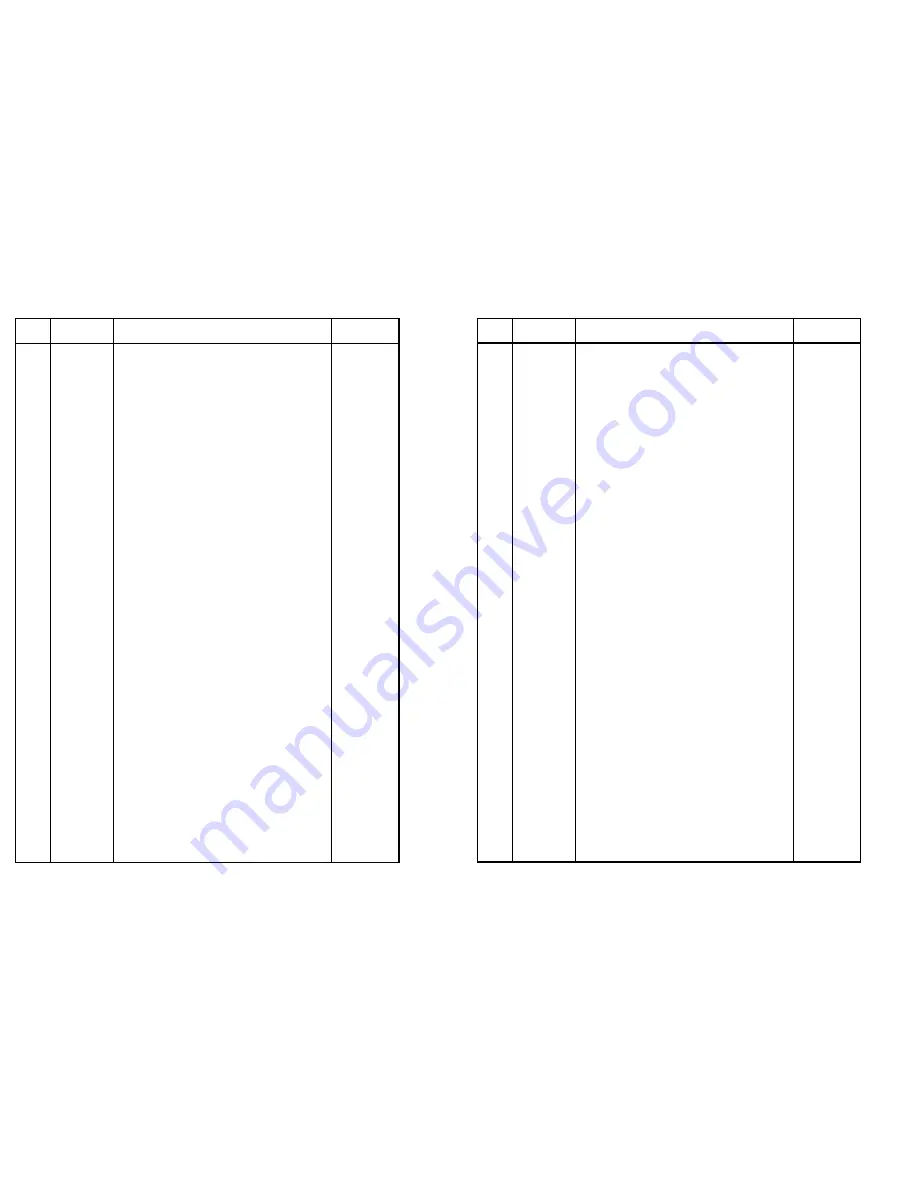
2. REGISTRATION AND 3RD PAPER FEED (A009)
May 1, ’87
Index
Parts No.
Description
Q’ty Per
No.
Assembly
1
A009 5211
PTL/ID Sensor Board
1
2
A009 2771
PTL Guide
1
3
A009 5253
Regist Sensor Board
1
4
A008 2284
Paper Guide
1
5
A009 5274
Harness - PTL
1
6
AX21 0005
1
Relay Roller Clutch
7
AA00 0009
Decal - A3
1
8
A009 2751
Registration Roller Knob
1
9
AA00 0008
Decal - A2
1
10
AA00 0010
Decal - A4
1
11
A009 1324
Inner Cover - Paper Feed
1
12
A009 2697
1
Relay Roller Knob
13
5215 2670
Upper Regist Roller
1
14
5215 2671
Lower Regist Roller
1
15
5215 2612
Regist Guide Plate
1
16
A009 2705
Guide Plate Knob - Lower
1
17
A009 2702
Left Guide Plate - 3rd Feed
1
18
A009 2704
Holder - Left Guide Plate
1
19
A009 2672
3rd Paper Feed Stay
1
20
5443 2668
Bushing
1
21
A009 2678
Paper End Feeler
1
22
A009 2673
Paper Feed Shaft Bracket
1
23
A009 2674
3rd Feed Shaft
1
24
A009 2677
Exit Guide Plate Holder - 3rd Feed
1
25
A009 2687
Balance Wheel - 3rd Paper Feed
1
26
5215 2618
Feed Roller Hub
1
27
5215 2619
Feed Roller
1
28
A009 2675
Front Exit Guide - 3rd Feed
1
29
A009 2676
Rear Exit Guide - 3rd Feed
1
30
A009 2694
1
Relay Driven Roller
31
A009 2699
Right Guide Plate - 3rd Feed
1
32
A009 2693
Relay Drive Roller
1
33
5215 5230
Photointerruptor - L Type
1
34
5203 2679
Pinion Tightening Screw - M4 x 5
2
35
AX21 0006
Paper Feed Clutch - 3rd Feed
1
Index
Parts No.
Description
Q’ty Per
No.
Assembly
36
5205 5313
Registration Clutch
1
37
5205 2866
Magnetic Clutch Collar
1
38
5215 2672
Bushing
2
39
5205 2697
Bushing - Upper Registration Roller
4
40
5205 2698
Relay Roller Spring
2
41
A009 2695
Bushing Holder
1
42
A009 2680
Ac tuator - Paper End Sensor
1
43
5442 2754
Spring - Registration Roller
2
44
5446 2901
Collar - 8mm
1
45
5053 0223
Bushing - 8mm
2
46
AB01 7035
Gear and Sprocket - 19T/20T
1
114
0314 0060W
Philips Pan Head Screw - M4 x 6
117
0314 0100W
Philips Pan Head Screw - M4 x 10
135
0344 0060W
Philips Truss Head Screw - M4 x 6
141
0434 0080W
Tapping Screw - M4 x 8
150
0575 0060E
Hexagon Headless Set Screw - M5 x 6
163
0720 0030E
Retaining Ring - M3
165
0720 0040E
Retaining Ring - M4
168
0720 0050E
Retaining Ring - M5
170
0720 0060E
Retaining Ring - M6
174
0725 0120E
Retaining Ring C - M12
183
0802 5085
Tapping Screw - M4 x 8
185
0802 5094
Tapping Truss Head Screw - M4 x 8
197
0805 3291
Ball Bearing - 8 x 16 x 5mm
215
0951 4008W
Philips Screw with Flat Washer - M4 x 8
220
0964 4008W
Tapping Screw with Flat Washer - M4 x 8
226
0965 4008W
Tapping Screw with Flat Washer - M4 x 8
5
Summary of Contents for FT4480
Page 1: ...FT4480 F I E L D S E R V I C E M A N U A L RICOH COMPANY LTD ...
Page 4: ...SECTION 1 INSTALLATION ...
Page 26: ...SECTION 2 SERVICE TABLES ...
Page 48: ...SECTION 3 REPLACEMENT AND ADJUSTMENT ...
Page 140: ...SECTION 4 ELECTRICAL DATA ...
Page 142: ...4 PAPER FEED CONTROL BOARD SCHEMATIC 15 March 87 A 0 0 9 ...
Page 143: ...5 DC POWER SUPPLY BOARD SCHEMATIC ...
Page 144: ...9 SORTER CONTROL BOARD SCHEMATIC 15 March 87 A 0 0 9 ...
Page 145: ...10 LCT CONTROL BOARD SCHEMATIC Main Control ...
Page 146: ...SECTION 5 DOCUMENT FEEDER ...
Page 171: ...SECTION 6 SORTER ...
Page 181: ...SECTION 7 LARGE CAPACITY TRAY ...
Page 195: ...SECTION 8 EDITOR BOARD ...
Page 204: ...S E C T I O N 9 ...
Page 237: ...RICOH FT4480 A009 PARTS CATALOG First Edition May 1987 RICOH COMPANY LTD ...
Page 239: ...1 EXTERIOR A009 May 1 87 ...
Page 241: ...2 REGISTRATION AND 3RD PAPER FEED A009 May 1 87 4 ...
Page 243: ...3 PLATEN COVER AND CASSETTE A009 May 1 87 6 ...
Page 245: ...4 1ST AND 2ND PAPER FEED A009 May 1 87 8 ...
Page 247: ...5 3RD PAPER LIFT A009 May 1 87 10 ...
Page 249: ...6 CASSETTE TRAY A009 May 1 87 12 ...
Page 251: ...7 FRAME A009 May 1 87 14 ...
Page 253: ...8 OPTICS 1 A009 May 1 87 16 ...
Page 255: ...9 OPTICS 2 A009 May 1 87 18 ...
Page 257: ...10 AROUND DRUM A009 May 1 87 20 ...
Page 259: ...11 CLEANING UNIT A009 May 1 87 22 ...
Page 261: ...12 DEVELOPMENT UNIT A009 May 1 87 ...
Page 263: ...13 DRIVE SECTION A009 May 1 87 26 ...
Page 265: ...14 PAPER TRANSPORT A009 May 1 87 28 ...
Page 267: ...15 FUSING UNIT A009 May 1 87 30 ...
Page 269: ...16 PAPER EXIT A009 May 1 87 ...
Page 271: ...17 ELECTRICAL SECTION 1 A009 May 1 87 34 ...
Page 273: ...18 ELECTRICAL SECTION 2 A009 May 1 87 36 ...
Page 275: ...19 MAIN BOARD A009 May 1 87 3 8 ...
Page 277: ...20 DC POWER SUPPLY BOARD A009 May 1 87 40 ...
Page 279: ...21 FUSING LAMP DRIVE BOARD A009 May 1 87 42 ...
Page 281: ...22 POWER RELAY BOARD A009 May 1 87 ...
Page 283: ...23 PAPER FEED CONTROL BOARD A009 May 1 87 46 ...
Page 285: ...24 AC MAIN HARNESS A009 May 1 87 48 ...
Page 287: ...25 DC MAIN HARNESS A009 May 1 87 50 ...
Page 289: ...26 HARNESS 3RD FEED A009 May 1 87 52 ...
Page 291: ...27 FUSING UNIT HARNESS A009 5 4 ...
Page 293: ...28 CONTROL HARNESS A009 May 1 87 5 6 ...
Page 295: ...29 HARNESS PAPER FEED A009 May 1 87 5 8 ...
Page 297: ...30 SPECIAL TOOL A009 May 1 87 60 ...
Page 299: ...PARTS INDEX 63 ...
Page 322: ...CS2070 A414 ...
Page 323: ...l Mini Sorter A414 2 2 Bin Motor Board A414 4 3 Sorter Harness A414 6 Parts Index 9 1 ...
Page 324: ...1 MINI SORTER A414 May 1 87 2 ...
Page 326: ...2 BIN MOTOR BOARD A414 May 1 87 4 ...
Page 328: ...3 SORTER HARNESS A414 May 1 87 6 ...
Page 330: ...PARTS INDEX 9 ...
Page 334: ...DF39 A419 ...
Page 336: ...1 DOCUMENT FEEDER I A419 May 1 87 2 ...
Page 338: ...2 DOCUMENT FEEDER II A419 May 1 87 4 ...
Page 340: ...3 DOCUMENT FEEDER Ill A419 May 1 87 6 ...
Page 342: ...4 DF MAIN BOARD A419 May 1 87 8 ...
Page 344: ...5 DF HARNESS A419 May 1 87 10 ...
Page 346: ...PARTS INDEX 13 ...
Page 353: ...RT15 A912 ...
Page 355: ...1 LCT A912 May 1 87 2 ...
Page 357: ...2 L C T A 9 1 2 May 1 87 4 ...
Page 359: ...3 LCT Ill A912 May 1 87 ...
Page 361: ...4 LCT BOARD A912 May 1 87 8 ...
Page 363: ...5 LCT HARNESS A912 May 1 87 10 ...
Page 365: ...PARTS INDEX 13 ...