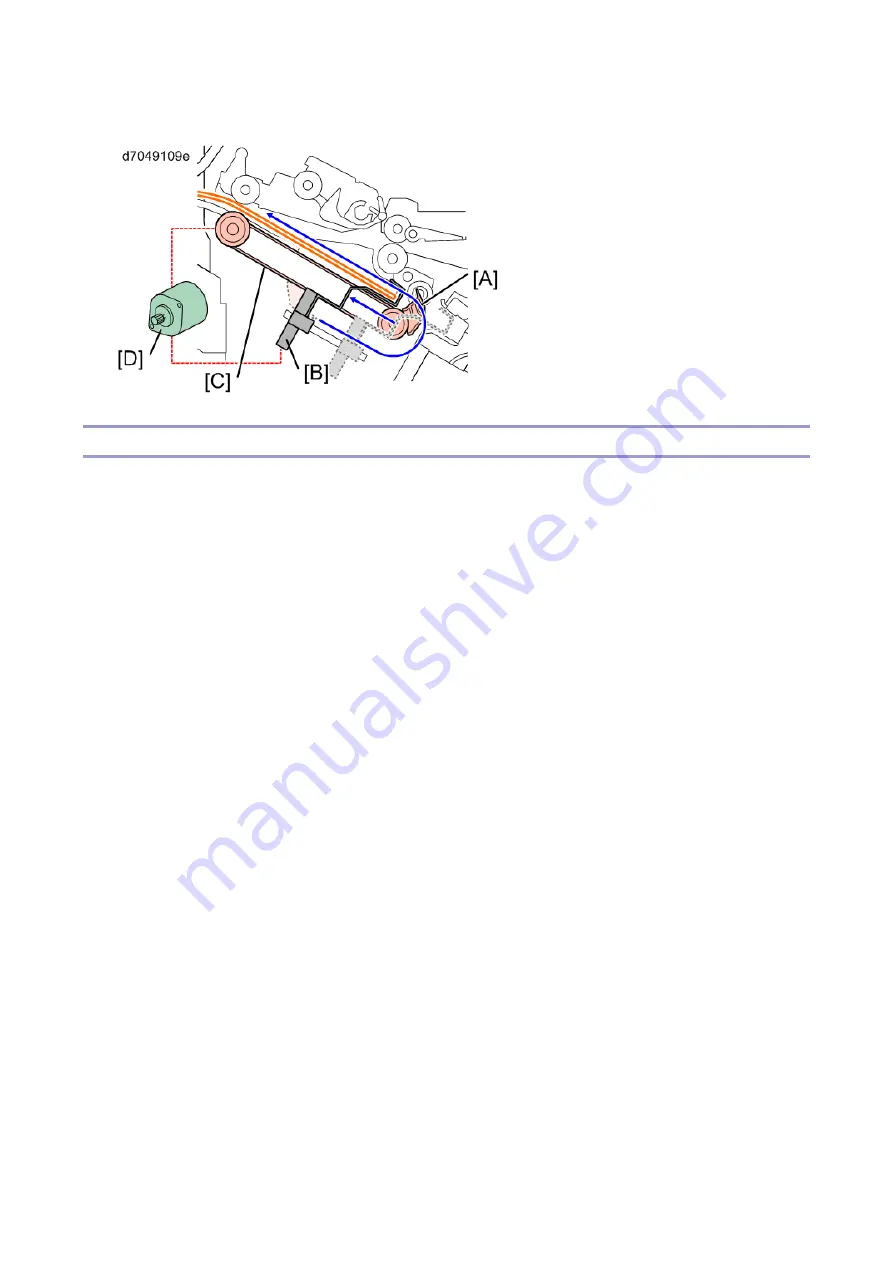
1.Detailed Descriptions
39
•
More than 11 sheets: Pawl, exit roller method
Staple Near-End Detection
A Staple Near-End Detection function has been added.
The finisher software counts the number of staples used. When the number of remaining staples drops
below the near-end threshold, a Near-End notification is sent to the machine and a banner prompting
staple replenishment appears on the operation panel.
You can check the remaining number of staples in [Mach./Applic. Stat] tab on the [Check Status]
screen.
Staple Use Counter
•
The staple use counter in the EEPROM counts the number of staples used. (Its initial value is 0.)
•
After the counter has detected that the staples have run out (End), it is reset when it detects
staples (= replenished).
•
Staples used in the End status are not counted.
Number of Remaining Staples [Maximum number - Counted Number of Staples Used]
The remaining number of staples is logged in SP6-795-002 / SP6-796-002 (Staple N.E. Setting: Staple
Remaining Setting). You can also change the remaining number of staples on this counter by changing
the value.
Near-End Threshold
The near-end threshold can be changed in SP6-795-001 / SP6-796-001 (Staple N.E. Setting: Near-End
Threshold). Depending on the model, the initial value is as follows:
•
SR3280/SR3290: 800 corner staples and 300 booklet staples
•
SR3270: 500 staples to be used for both corner and booklet stapling
•
SR3260: 500 corner staples
Control
If the remaining number of staples (SP6-795-002/SP6-796-002) drops below the near-end threshold,
Summary of Contents for SR3280
Page 2: ......
Page 6: ......
Page 9: ...3 ...
Page 91: ...2 Replacement and Adjustment 85 3 Remove the Booklet Jogger Motor STM11 A x 2 ...
Page 100: ...2 Replacement and Adjustment 94 ...