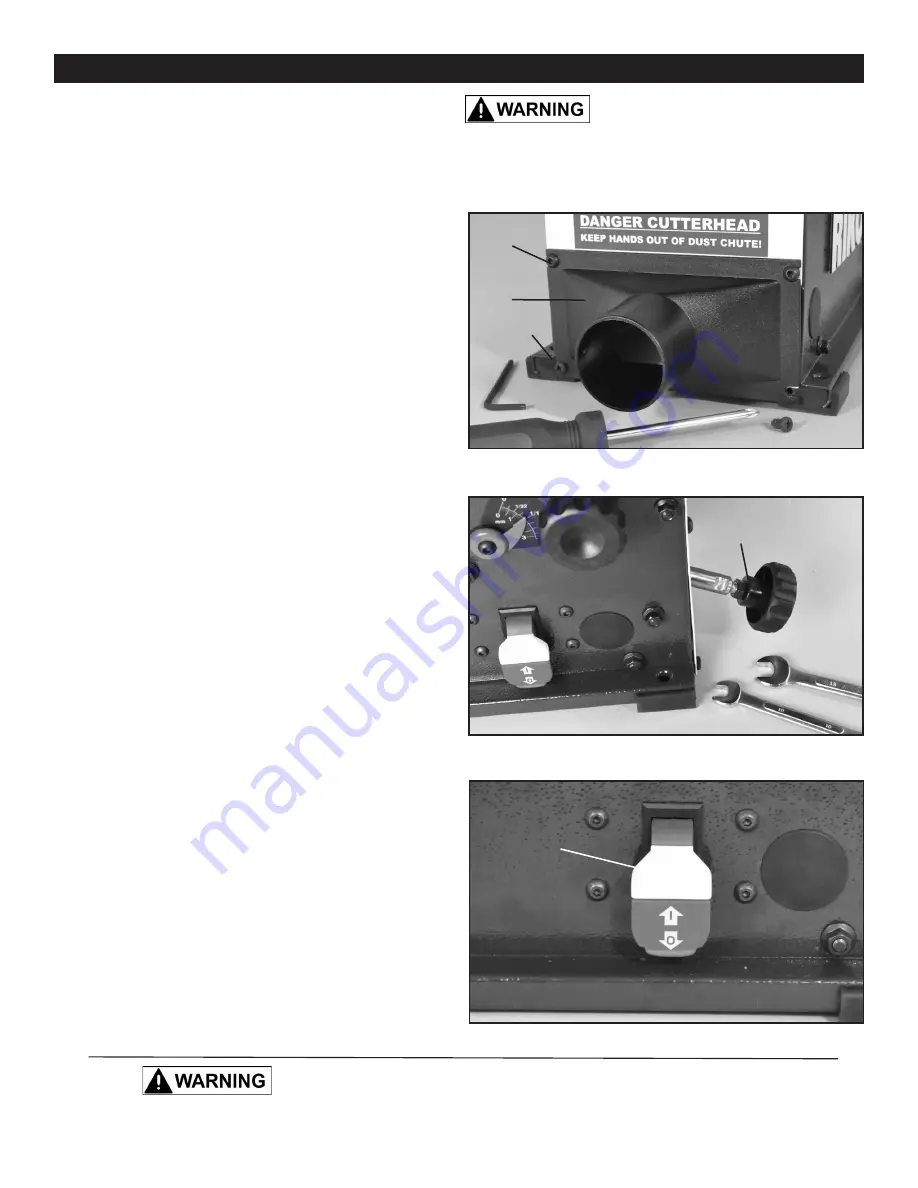
11
ASSEMBLY
FIG. 9
FIG. 10
FIG. 11
DUST PORT ASSEMBLY
A Dust Port (A) is supplied with the jointer to help
connect it to a standard 2-1/2 inch vacuum hose.
1. Tighten the two upper Screws (B) with a 4 mm hex
wrench, and tighten the two lower Screws (C) with a
Phillips screwdriver when the dust port is in proper
location. FIG. 9.
NOTE:
It is extremely important that a dust collection
system is used with this jointer to eliminate harmful
airborne dust, prevent the build-up of chips that may
jam the cutterhead, and to keep the working area
clean of debris. Make sure all connections are secure
and your dust collector is turned on before any milling
of lumber is done.
However, if you do not plan to use a dust collector,
then there is no need to attach this dust port to the
jointer. Chips ejected from the operating machine
should be collected and disposed of immediately to
keep the area clean and to avoid accidents.
TABLE ADJUSTMENT KNOB ASSEMBLY
Attach the infeed table’s Adjustment Knob (A) to the
jointer by tightening the hex nut (B) with a 10 mm and
13mm open end wrenches. FIG. 10.
SWITCH ASSEMBLY
The jointer is turned on by flipping the switch into the
up position, and it is turned off by flipping the switch in
the down position.
This jointer is also equipped with a special lockout
toggle switch that prevents unauthorized use. To
prevent unauthorized use of the jointer, simply pull out
the yellow key (A) located on the face of the switch.
FIG. 11
.
CAUTION:
DO NOT continuously use the jointer at
the maximum depth of cut, 1/8 in. (3mm), as it will put
excessive stress on the motor which will damage it.
Before turning on the machine, review the safety precautions
listed on pages 3 to 6. Make sure that you fully understand the features, adjustments
and capabilities of the machine that are outlined throughout this manual.
THE MACHINE MUST NOT BE
PLUGGED IN AND THE POWER SWITCH MUST BE IN
THE OFF POSITION UNTIL ALL ADJUSTMENTS ARE
COMPLETE.
A
B
C
A
B
A
C
B
Summary of Contents for 20-600H
Page 23: ...23 WARRANTY...