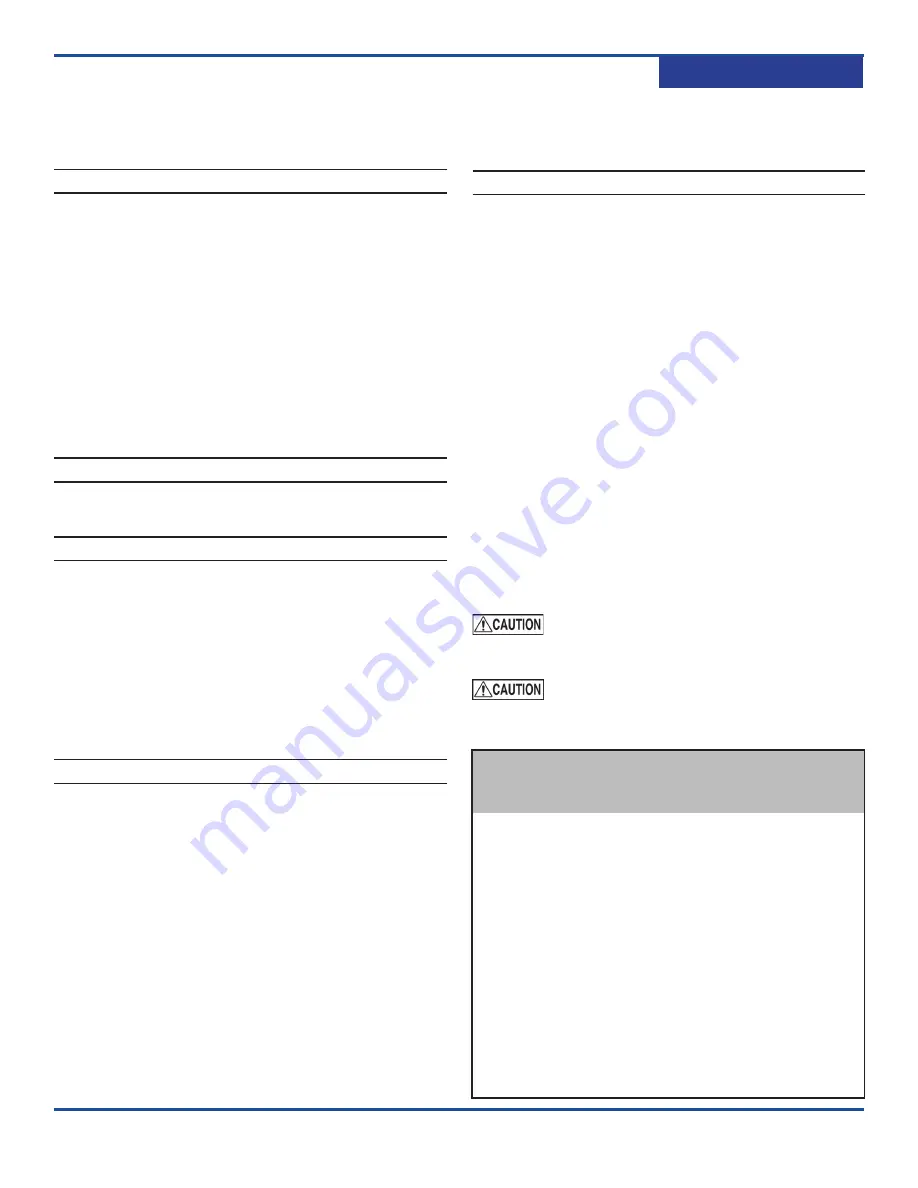
233-Truck-20K-ISM-RevB-07-06-18
Page 7
ENG
MAINTENANCE
A visual inspection of the suspension structure should be performed during each pre-trip/safety inspection.
Ridewell Suspensions recommends the following minimum service intervals for standard duty, on-highway
usage applications. More frequent intervals are recommended for heavier duty applications.
Daily/Pre-Trip Inspections
___ Check tires for proper inflation, damage or
excessive wear.
___ Check wheel-ends for obvious signs of lubricant
leakage. Check for missing components.
___ Visually inspect suspension structure for signs
of damage or excessive wear.
___ Check for loose or missing bolts/nuts. Check for
irregular movement in suspension components.
___ Make sure air controls are operating properly.
Drain all moisture from air reservoirs.
First 6,000 miles of use
___ Torque all suspension bolts/nuts to specifica
-
tions (torque values chart in Appendix).
Every 12,000 miles of use
___ Lubricate Brake Cam and Slack Adjuster.
___ Inspect kingpins and upper/lower kingpin
bushings for wear. Grease thrust bearings.
___ Inspect steering damper for damage/wear.
___ Inspect air springs for any damage or
excessive wear. Torque air spring bolts/nuts
to specifications (Appendix).
___ Check air system for leaks.
First 50,000 miles of use
___ Torque all suspension bolts/nuts to specifica
-
tions (Appendix).
___ Check wheel ends for excessive play.
___ Check suspension pivot bushings for wear.
___ Check operation of (reverse) steering lock
(if equipped).
___ Verify operation of manual/automatic lift-in-
reverse control (if equipped).
___ Inspect tie-rod and tie-rod ends for damage and
wear. Lubricate tie-rod ends. Check that the tie-
rod boot is in place and completely over the end
of the tie-rod. Replace entire tie-rod end if boot
is damaged.
Annually/100,000 miles of use
___ Inspect pivot connections for worn pivot
bushings and replace, if necessary. Torque pivot
hardware and component bolts/nuts to specifi
-
cations (Appendix).
___ Check
suspension hanger and air spring mount-
ing plate connections to frame.
___ Check lubrication level in wheel ends:
1) Oil-Filled Wheel Ends: Refill/Replace lubri
-
cant as needed (Refer to TMC RP 631 “100K/
Annual Inspection”).
2)
Semi-Fluid Grease: Pull outer bearing and vi
-
sually inspect lubrication level. Refill/Replace as
needed (Refer to TMC RP 631 “Level 3 Lubrica-
tion Level Inspection” and TMC RP 618 “Wheel
Bearing Adjustment Procedure”).
___ Check air system for leaks.
___ Test air system pressure protection valve
(if equipped).
___ Check brake chambers and brakes for damage
and proper function.
Failure to exhaust all pressure from the
air system before working on the vehicle can cause
serious injury.
Failure to torque bolts/nuts of suspension
components to specifications can result in failure of
the suspension and void the warranty.
Refer to the following Technology &
Maintenance Council (TMC) publications
for additional maintenance information.
TMC RP 609 Self-Adjusting and Manual Brake
Adjuster Removal, Installation
and Maintenance
TMC RP 618 Wheel Bearing
Adjustment Procedures
TMC RP 619 Air System Inspection Procedure
TMC RP 622 Wheel Seal and Bearing Removal,
Installation, and Maintenance
TMC RP 631 Recommendations for
Wheel End Lubrication
TMC RP 643 Air Ride Suspension
Maintenance Guidelines
TMC RP 645 Tie Rod End Inspection
and Maintenance Procedure
TMC RP 651 Steer Axle
Maintenance Guidelines