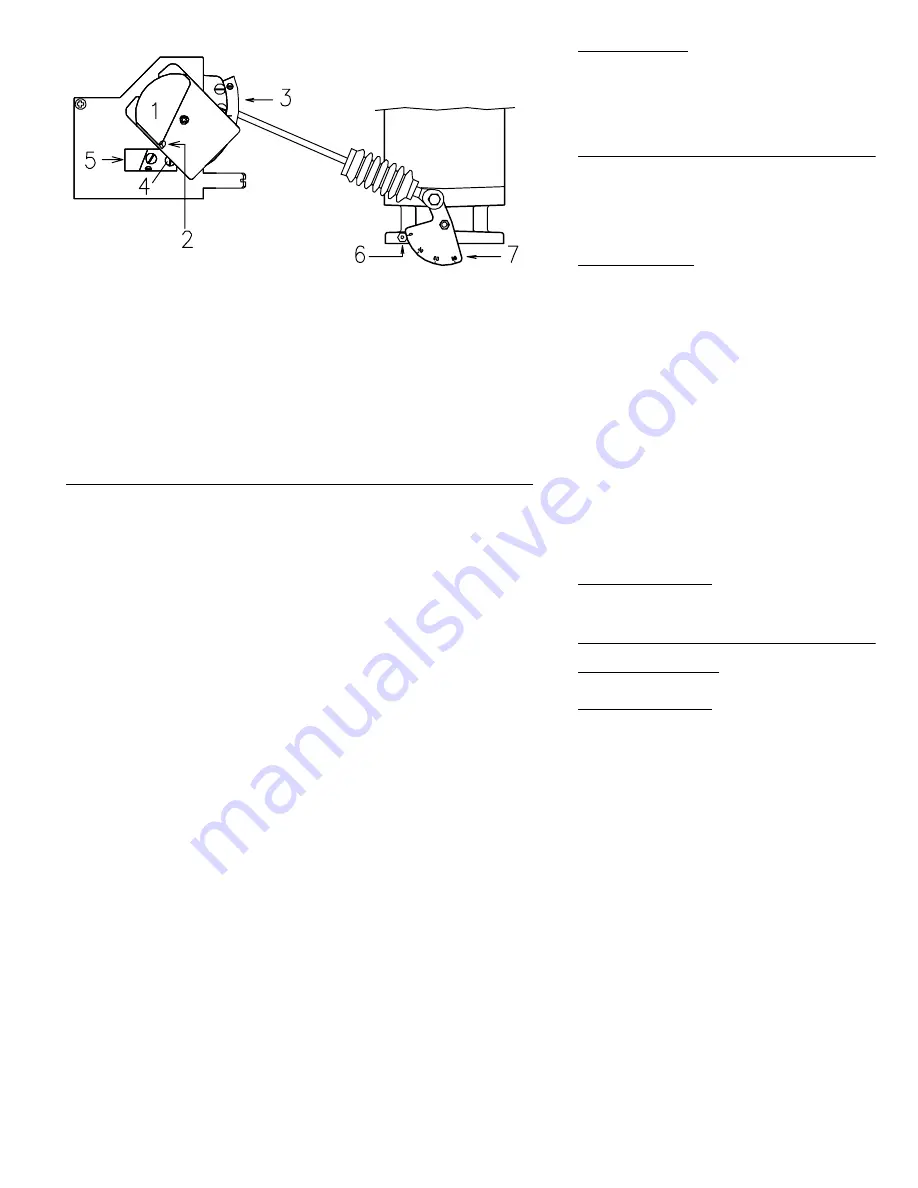
12
Adjusting air delivery
Progressively adjust the end profile of cam 4)(A) by turn-
ing the cam adjustment screws as they appear through
the access opening 6)(A).
- Turn the screws clockwise to increase air delivery.
- Turn the screws counter-clockwise to reduce air deliv-
ery.
3 - MINIMUM OUTPUT
Minimum output must be selected within the firing rate
range shown on page 5.
Press switch 2)(A)p.11 “output reduction” until the servo-
motor has closed the air damper and the gas butterfly
valve to 15° (factory set adjustment).
Adjusting gas delivery
Measure the delivery of gas from the gas meter.
- If this value is to be reduced, decrease the angle of
orange cam (B) slightly by proceeding a little at a time
until the angle is changed from 15° to 13° or 11°....
- If it has to be increased press the switch “output
increase” 2)(A)p.11 (i.e. open the gas butterfly valve
by 10-15°), increase the orange cam angle (B) with
small successive movements, i.e. take it from angle
15° to 17° - 19°....
Then press the switch “output decrease” until the ser-
vomotor is taken to the minimum opening position and
measure the gas delivery.
Note
The servomotor follows the adjustment of cam only
when the cam angle is reduced. If it is necessary to
increase the cam angle, first increase the servomotor
angle with the switch “output increase”, then increase
the orange cam angle, and at the end bring the servo-
motor back to the MIN output position with the switch
”output decrease”.
Adjustment of air delivery
Progressively adjust the starting profile of cam 4)(A) by
turning the screws working throught the access hole
6)(A).
4 - INTERMEDIATE OUTPUTS
Adjustment of gas delivery
No adjustment of gas delivery is required.
Adjustment of air delivery
With the switch 1)(A) page 11 move in intermediate out-
puts and set the variable profile cam 4) by turning the
screws 5).
- If the burner operation is low-high it is sufficient to set
only minimum and maximum firing rates
- If the burner operation is modulating, all the points of
modulation should be adjusted.
When the adjustment is complete, release the servomo-
tor and manually check there is no binding of the cam.
(A)
1 Servomotor
2 Lever, push to engage, push to release
3 Adjustable profile cam
4 Cam profile adjustment screws
5 Opening for access to screws 5
6 Index for graduated sector 8
7 Graduated sector for gas butterfly valve
D2267