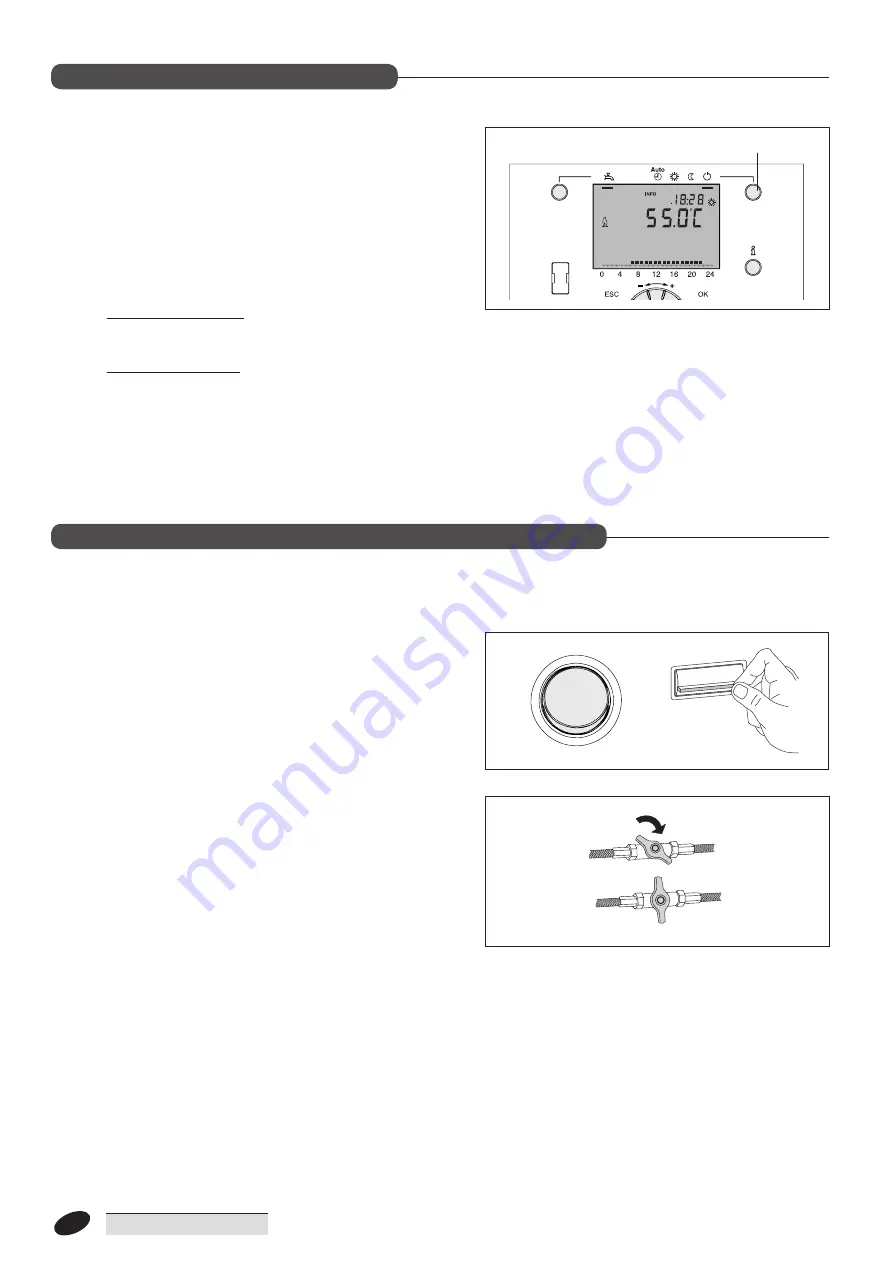
26
SYSTEM MANAGER
If you are going to be away for a short period of time like
a weekend or a short holiday, etc. proceed as follows.
- Press the central heating mode button (5) to select
"Protection" mode (
b
).
Power to the boiler remains switched on, and the display
remains active. The fuel feed also remains open so that
the
frost protection
function can protect the boiler
against freezing.
Boiler frost protection: if boiler temperature falls below
5°C, the burner starts up at full power until boiler tempe-
rature reaches 40°C.
Plant frost protection: This function is only active if an
outside temperature sensor is connected.
If outside temperature drops below -4°C the pumps are
switched on. If outside temperature is between -5° and
1.5°C, the pumps are switched on for 10 minutes at inter-
vals of 6 hours. If outside temperature is above 1.5°C the
pumps are switched off.
If the boiler is not going to be used for an extended period
of time, proceed as follows to prepare it for shut-down.
- Turn the control panel power switch OFF and make sure
that the display goes out.
- Turn the mains power switch OFF.
- Close the fuel shut off cock and the central heating and
DHW circuit shut off cocks.
b
Under these conditions the system is not pro-
tected against frost . Drain the central heating cir-
cuit and domestic hot water circuit if there is any
risk of freezing .
ON
OFF
5
Boiler temperature
Preparing for extended periods of disuse
PREPARING FOR EXTENDED PERIODS OF DISUSE
Temporary shutdown
TEMPORARY SHUTDOWN