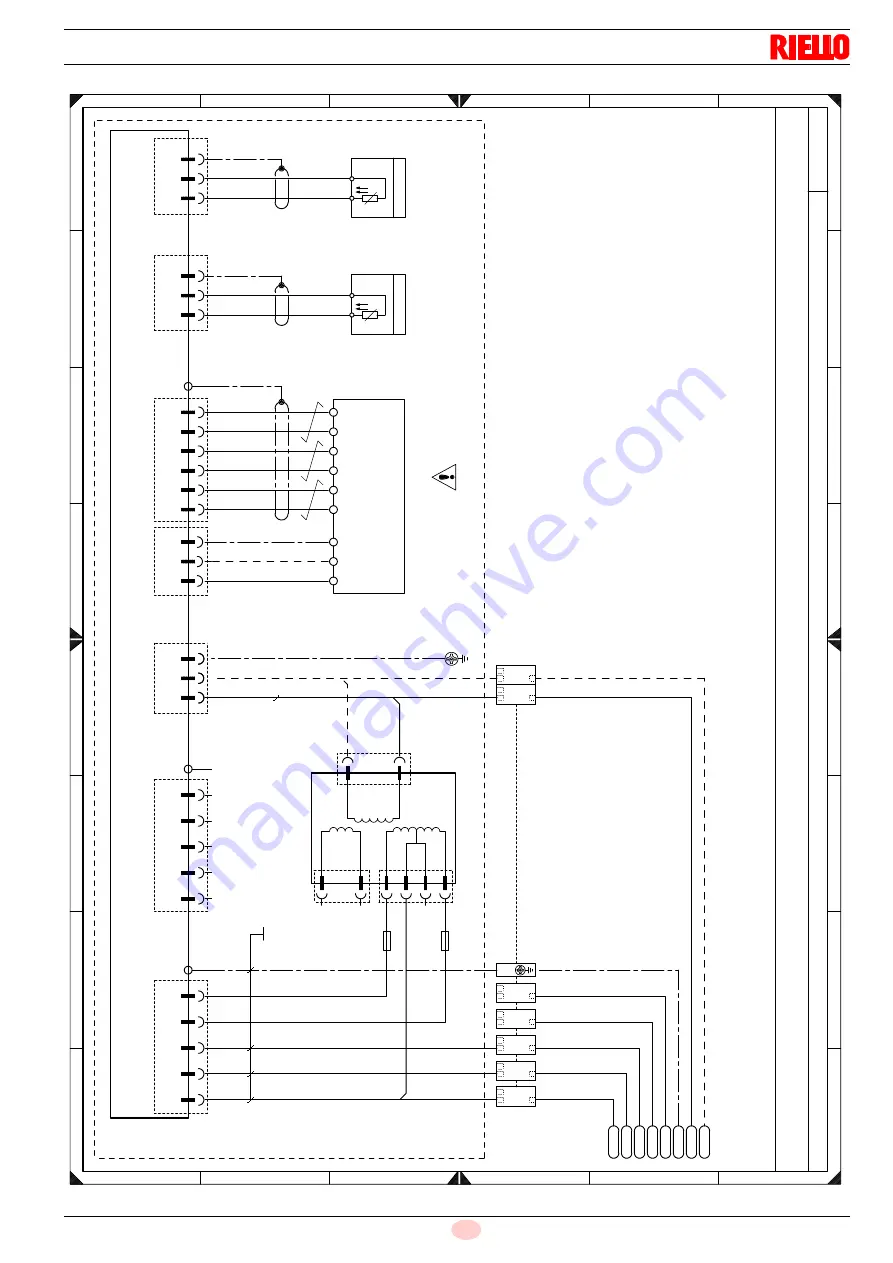
53
20175134
GB
Appendix - Electrical panel layout
!"
#!$$$
!
!
% &'
%&
&%%(
"
"
%
%
%& )$$$*#!$$$%'
$$$*#!$$$+ &'
%&$$$*#!$$$
'
%&%$$$*#!$$$,%'
!!$*
'
!
+
-.
"
"
!
"
#!$$$
+
!
#!$$
!
!
%
%
%
%
&&
,
,
,
,
%
%
%
%
+
",%
$$$$
,%
"
'
'
%&
!
,%
,%
*$
*$
*$
*$
*$
*$
/01
!
%&
%
,%
,%
*$
*$
2%
!
"
#
#
2%
2%
%&
%
2
2
3 * * *
'3*%'**%&)
+3!*+*4 *!
!3,*!*,*!5
3** !*
&3%*&*%*
!3%*!*!*!
,3,*,*,*,
!+3!!*!+*!*!
'3*'**
!3*!**!
#3 %&* # * # * '
3!*,*!*
!+3!*,*+*!*4 *,*!*!
3***
-.
-.
-/01
-/01
-/01
,%
,%
,%
!!$
*!/
*!/
Summary of Contents for 20166004
Page 2: ...Translation of the original instructions ...
Page 46: ...20175134 44 GB Appendix Electrical panel layout ...
Page 49: ...47 20175134 GB Appendix Electrical panel layout ...
Page 50: ...20175134 48 GB Appendix Electrical panel layout ...
Page 51: ...49 20175134 GB Appendix Electrical panel layout 0 ...
Page 52: ...20175134 50 GB Appendix Electrical panel layout 0 0 0 1 0 2 0 0 0 0 0 0 0 30 3 3 0 0 1 0 ...
Page 53: ...51 20175134 GB Appendix Electrical panel layout 0 1 1 1 2 ...
Page 59: ......