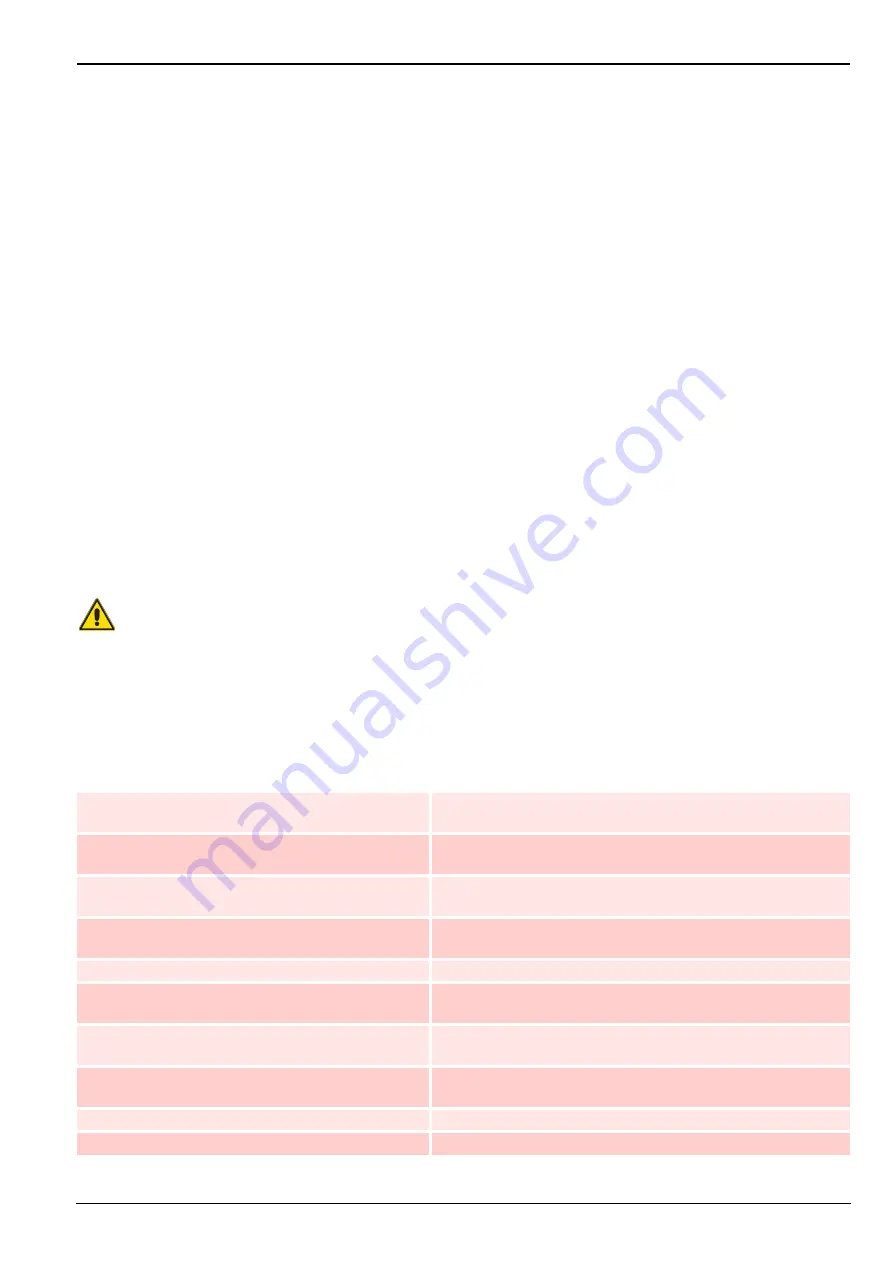
3159
9
SAFETY TEST - WITH GAS BALL VALVE CLOSED
It is fundamental to ensure the correct execution of the electrical connections between the gas solenoid valves
and the burner to perform safely the commissioning.
For this purpose, after checking that the connections have been carried out in accordance with the burner's elec-
trical diagrams, an ignition cycle with closed gas ball valve -dry test- must be performed.
1 The manual ball gas valve must be closed
2 The electrical contacts of the burner limit switch need to be closed
3 Ensures closed the contact of the low gas pressure switch
4 Make a trial for burner ignition
The start-up cycle must be as follows:
– starting the fan for pre-ventilation
– Performing the gas valve seal control, if provided
– Completion of pre-ventilation
– Arrival of the ignition point
– Power supply of the ignition transformer
– Electrical Supply of solenoid gas valves
Since the manual gas ball valve is closed, the burner will not light up and its control box will go to a safety lockout
condition.
The actual electrical supply of the solenoid gas valves can be verified by inserting a tester, Some valves are
equipped with light signals (or close/open position indicator) that turn on at the same time as their power supply.
IF THE ELECTRICAL SUPPLY OF THE GAS VALVES OCCURS AT UNEXPECTED TIMES. DO NOT
OPEN MANUAL GAS BALL VALVE, SWITCH OFF POWER LINE; CHECK THE WIRES; CORRECT
THE ERRORS AND REPEAT THE COMPLETE TEST.
SAFETY COMPONENTS
The safety components must be replaced at the end of their life cycle indicated in Tab. The specified life cycles
do not refer to the warranty terms indicated in the delivery or payment conditions.
Safety component
Life cycle
Flame control
10 years or 250,000
operation cycles
Flame sensor
10 years or 250,000
operation cycles
Gas valves (solenoid)
10 years or 250,000
operation cycles
Pressure switches
10 years or 250,000
operation cycles
Pressure adjuster
15 years
Servomotor (electronic cam) (if present)
10 years or 250,000
operation cycles
Oil valve (solenoid)
(if present)
10 years or 250,000
operation cycles
Oil regulator (if present)
10 years or 250,000
operation cycles
Oil pipes / couplings (metallic) (if present)
10 years
Fan impeller
10 years or 500,000 start-ups