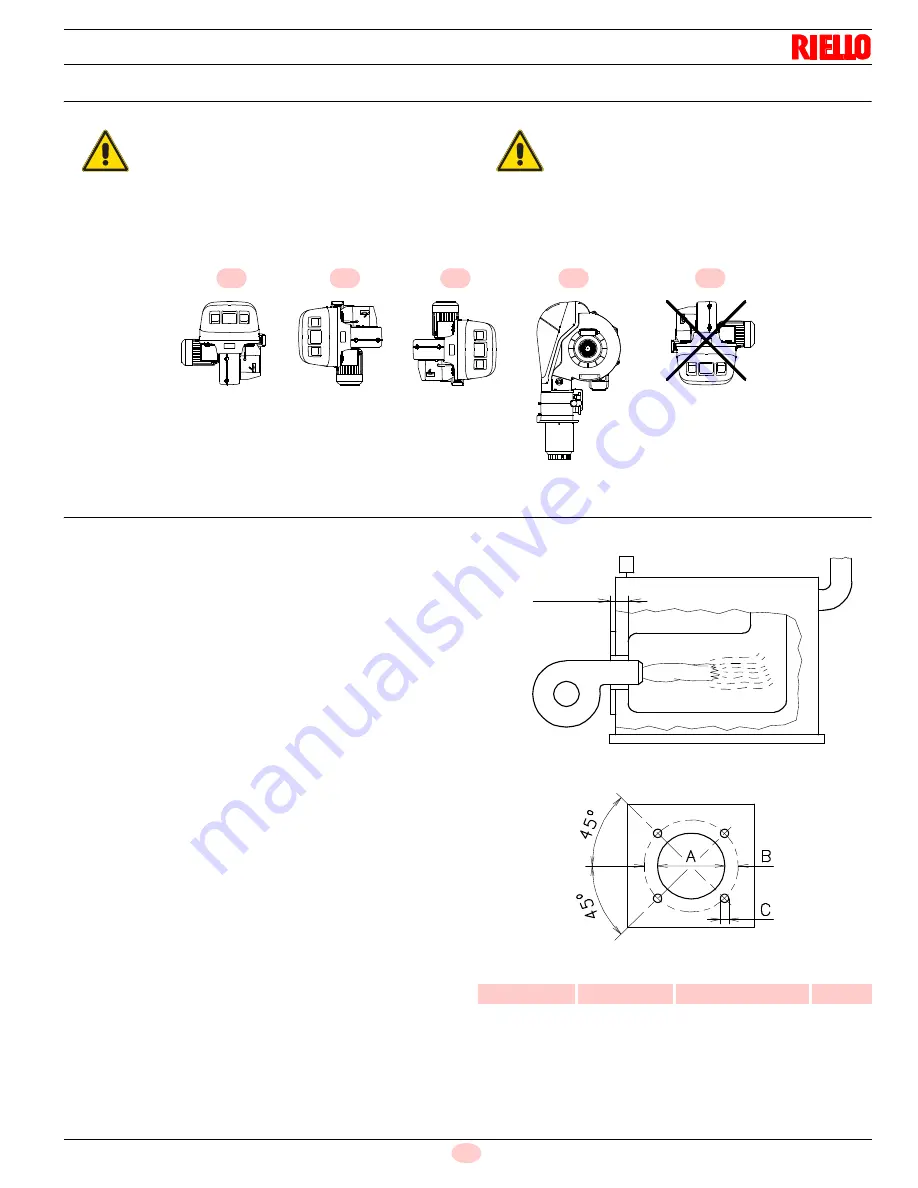
Installation
17
20102152
GB
4.4
Operating position
4.5
Preparing the boiler
4.5.1
Introduction
The burners are suitable for working on both flame inversion
boilers (
*
) (in this case the long head model is recommended) and
boilers with a combustion chamber with bottom runoff (three
flue gas circulations), from which the best results of low NO
x
emissions are obtained.
The maximum thickness of the front hatch of the boiler A)(Fig. 10),
complete with refractory, must not exceed 8” max.
(
*
) For flame inversion boilers, a kit is available to reduce the CO,
if necessary. See Accessories.
The kit consists of 5 gas tubes, identical to the other 5 already
present in the burner head. In standard conditions, the head of
the burner is fitted with a second group of tubes, from which
the gas emerges in a different direction compared with the oth-
ers.
With the kit, this second group of tubes is substituted so that all
the tubes are the same.
After assembling the kit, check its efficiency by measuring the
flue gases and CO.
4.5.2
Boiler plate
Make holes in the plate shutting off the combustion chamber, as il-
lustrated in Fig. 11.
The position of the threaded holes can be marked using the ther-
mal insulation screen supplied with the burner.
Tab. H
WARNING
The burner is designed to operate only in posi-
tions
1
,
2
,
3
and
4
Installation
1
is preferable, as it is the only one
that allows the maintenance operations as
described in this manual.
Installations
2
,
3
and
4
permit operation but
make maintenance and inspection of the com-
bustion head more difficult.
DANGER
Any other position could compromise the cor-
rect operation of the appliance.
Installation
5
is prohibited for safety reasons.
2
3
4
5
1
Fig. 9
D7739
inch
A
B
C
RS 120/EV
9
1
/
16
12
25
/
32
- 14
1
/
2
5
/
8
W
Fig. 10
8” max
D1079
Fig. 11
D455