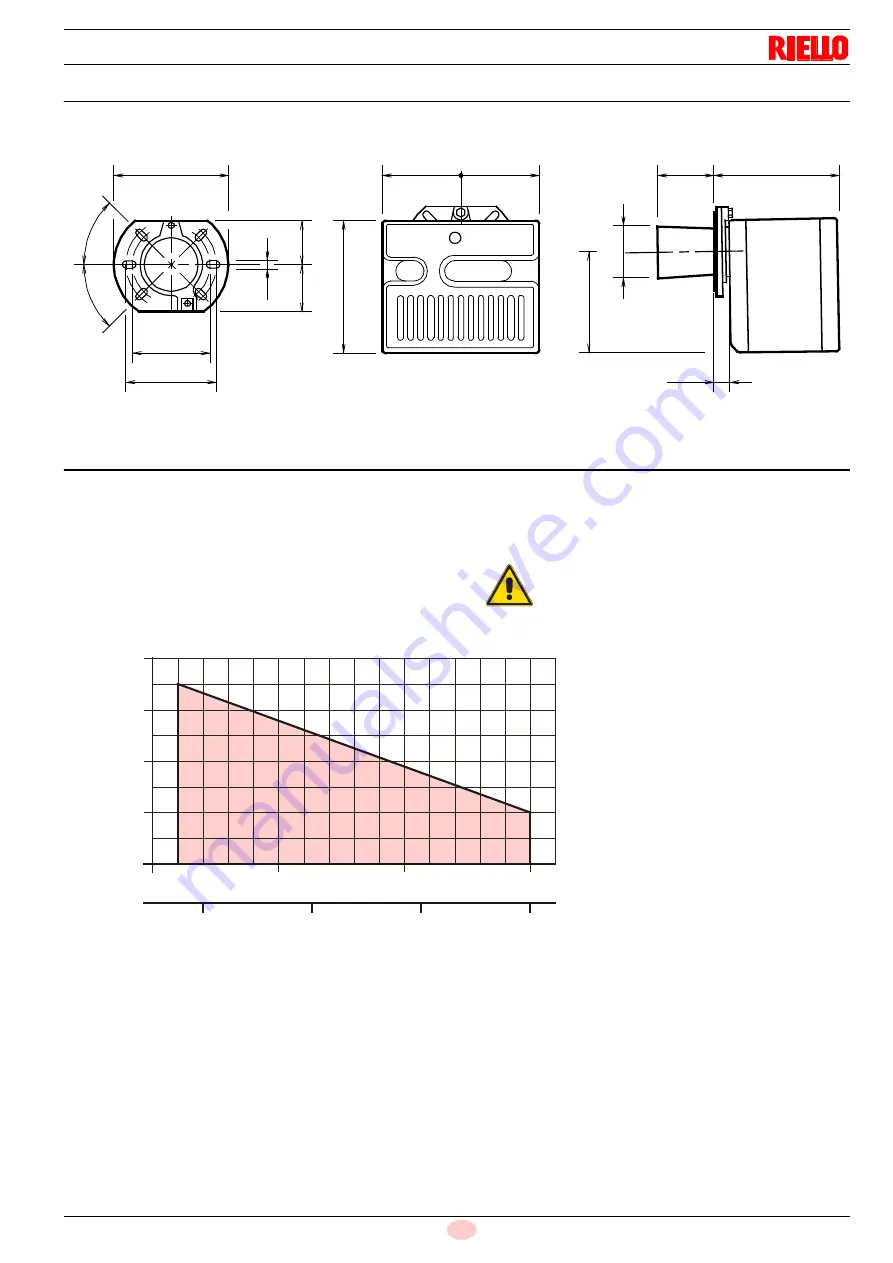
9
20032173
GB
Technical description of the burner
4.4
Burner dimensions
4.5
Firing rate
The
MAXIMUM OUTPUT
is chosen from within the diagram area
(Fig. 3).
The
MINIMUM OUTPUT
must not be lower than the minimum
limit of the diagram.
The burner delivery must be selected within area of the diagrams
(Fig. 3). This area is called firing rate and provides the maximum
delivery of the burner in relation to the pressure in the combustion
chamber.
The work point may be found by plotting a vertical line from the
desired delivery and a horizontal line from the pressure in the
combustion chamber. The intersection of these two lines is the
work point which must lie within the firing rates.
Fig. 2
Flange
Burner
252
93
203
130
=
19
4
5
°
215
11
16
4
D5509
=
180
75
72
150
4
5
°
ø
90
WARNING
The firing rate area values have been obtained
considering a surrounding temperature of 20 °C,
and an atmospheric pressure of 1013 mbar (ap-
prox. 0 m above sea level).
Fig. 3
Pressure in the combustion
ch
amber –
mba
r
0.8
0
0.2
0.4
1.5
2.0
2.5
3.0
Fuel output -
kg/h
20
25
30
35
Thermal power -
kW
D5223
0.6