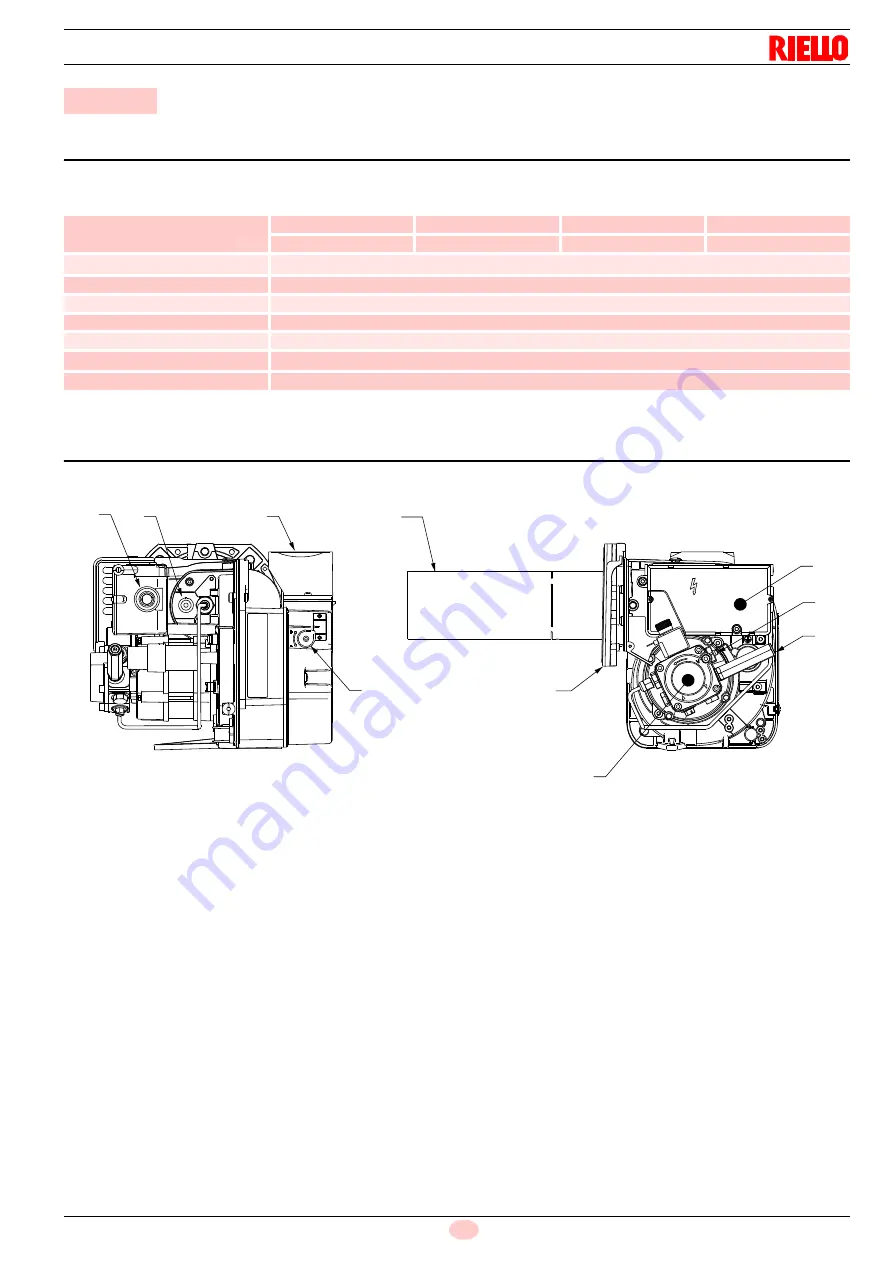
7
20115639
GB
Technical description of the burner
4.1
Technical data
Tab. A
4.2
Burner description
1 Pump
2 Control
box
3
Reset push-button with lock-out lamp
4
Flange with insulating gasket
5
Air damper adjustment screw
6 Snorkel
(BF)
7
Pump pressure adjustment screw
8 Pressure
gauge
port
9 UV
sensor
10 Blast
tube
4
Technical description of the burner
TYPE
RDB2.2 BG1 BLU
16
RDB2.2 BG1 BLU
21
RDB2.2 BG1 BLU
26
RDB2.2 BG3 BLU
36
Output Thermal power
(with air at 20 °C)
kg/h
1.3
1.8
2.2
3.0
kW
16
21
26
36
Fuel
Kerosene, viscosity 1.6 - 6 mm
2
/s at 20 °C (Hi = 11.97 kWh/kg)
Electrical supply
Single phase,
~ 50Hz 230V ± 30%
Motor
Run current 0.85A - 2700 rpm - 283 rad/s
Capacitor
4.5 mF
Ignition transformer
Secondary
18 kV - 25 mA
Pump
Kerosene, maximum pressure 11 bar (160psi)
Absorbed electrical power
kW
0.15
10
4
1
7
8
2
3
9
5
6
20116940
Fig. 1