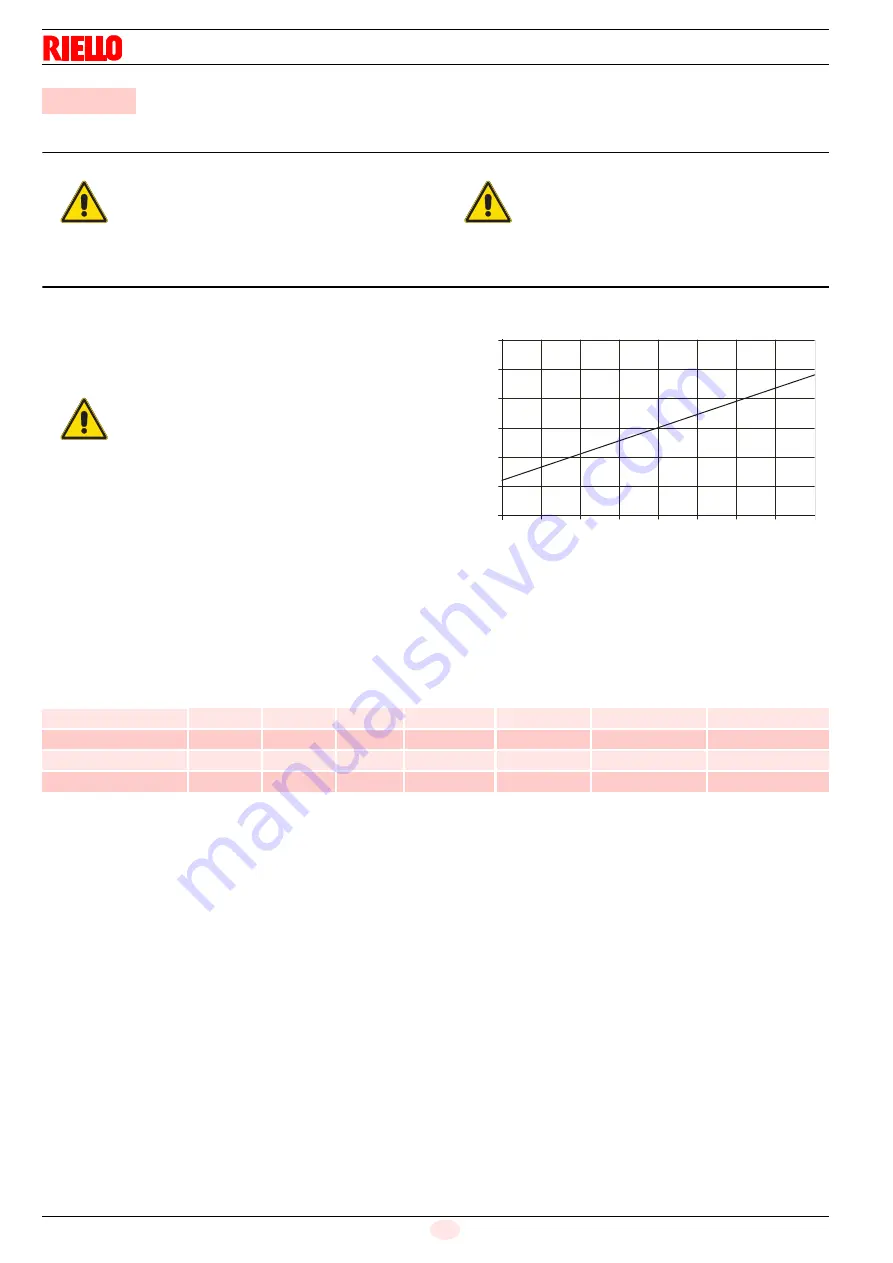
Start-up, calibration and operation of the burner
20153653
16
GB
6.1
Notes on safety for the first start-up
6.2
Combustion adjustment
In conformity with EN 267, the application of the burner on the
boiler, adjustment and testing must be carried out observing the
instruction manual of the boiler, including verification of the CO
and CO2 concentration in the flue gases, their temperatures and
the average temperature of the water in the boiler.
Settings carried out in factory
The values in Tab. F refer to 12.50 of CO
2
, at sea level and with
an ambient and light oil temperature of 20 °C.
Tab. F
(*)
Type-approval adjustment
6
Start-up, calibration and operation of the burner
WARNING
The first start-up of the burner must be carried out
by qualified personnel, as indicated in this manual
and in compliance with the standards and regula-
tions of the laws in force.
WARNING
Check the correct working of the adjustment, com-
mand and safety devices.
WARNING
The combustion air is sucked from outside, there-
fore, there can be sensitive temperature varia-
tions that can influence the percentage value of
the CO2. It is advisable to adjust the CO2 accord-
ing to the indicated diagram.
e.g. with a combustion air temperature of 10°C,
adjust the CO2 to 12.5% (± 0.2%).
Combustion air temperature (°C)
D4604
&2
Fig. 14
Model
Nozzle
Pump
pressure
(+/-0.5)
Burner
output
Combustion
head
adjustment (*)
(+/-0.5)
Air damper
adjustment
(+/-0.25)
Model
GPH
Angle
bar
kg/h ± 4%
mm
Set-point
RDB2.2 BX 15-20
Danfoss
0.50
80° EH
10.6
1.7
12.5
B/3.2
RDB2.2 BX 20-26
Danfoss
0.65
80° EH
8.7
2.0
13.5
C3.5
RDB2.2 BX 26-35
Danfoss
0.85
60° EH
9
2.6
16.5
4.75
RDB2.2 BX 35-41
Danfoss
1.10
60° EH
10
3.4
20.5
8.20