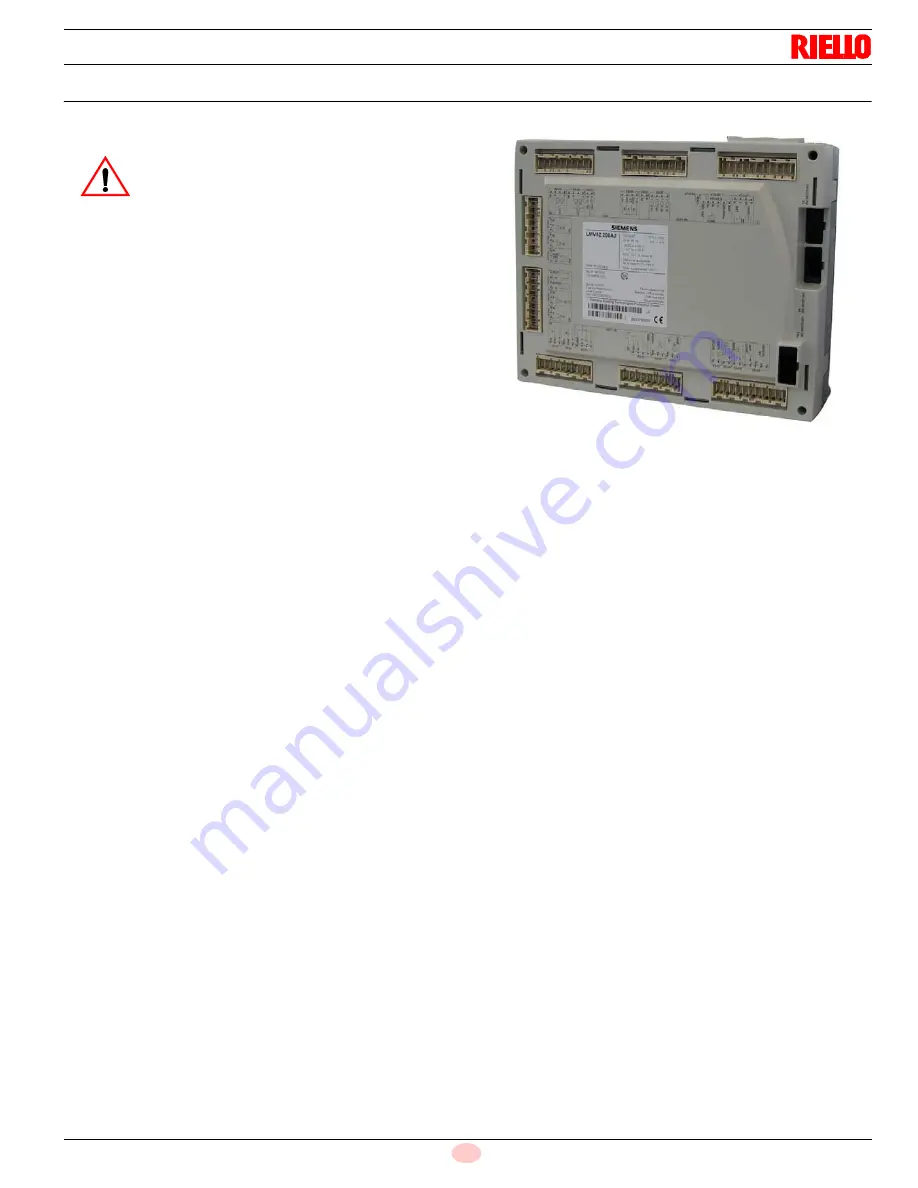
Technical description of the burner
11
20035606
GB
3.9
Control box for the air/fuel ratio (LMV51...)
Warning notes
All activities (mounting, installation and service work, etc.)
must be performed by qualified staff.
Before making any wiring changes in the connection area of
the LMV5..., completely isolate the plant from mains supply
(all-polar disconnection). Ensure that the plant cannot be
inadvertently switched on again and that it is indeed dead. If
not observed, there is a risk of electric shock hazard.
Protection against electrical shock hazard on the LMV5... and
on all connected electrical components must be ensured
through appropriate mounting.
Each time work has been carried out (mounting, installation
and service work, etc.), check to ensure that wiring is in an
orderly state, that the parameters have been correctly set and
make the safety checks.
Fall or shock can adversely affect the safety functions.
Such units must not be put into operation even if they do not
exhibit any damage.
In programming mode, the position check of actuators and
VSD (checking electronic fuel / air ratio control) is different
from the check during automatic operation.
Like in automatic operation, the actuators are still jointly
driven to their required positions. If an actuator does not
reach the required position, corrections are made until that
position is reached.
However, in contrast to automatic operation, there are no time
limits to these corrective actions.
The other actuators maintain their positions until all actuators
have reached the positions currently required.
This is essential for setting fuel /air ratio control. This means
that during the time the fuel / air ratio curves are programmed,
the person making the plant settings must continuously moni-
tor the quality of the combustion process (e.g. by means of a
flue gas analyzer).
Also, if combustion levels are poor, or in the event of danger-
ous situations, the commissioning engineer must take appro-
priate action (e.g. switching off manually).
To ensure the safety and reliability of the LMV5... system, the
following points must also be observed:
– Condensation and ingress of humidity must be avoided. Should
such conditions occur, make sure that the unit will be completely
dry before switching on again!
– Static charges must be avoided since they can damage the
unit’s electronic components when touched.
Mechanical design
The LMV5... is a microprocessor-based burner management sys-
tem with matching system components for the control and supervi-
sion of forced draft burners of medium to large capacity.
The following components are integrated in the basic unit of the
LMV5...:
• Burner control with gas valve proving system
• Electronic fuel / air ratio control with a maximum of 4 (LMV51…)
or 6 (LMV52…) actuators
• Optional PID temperature / pressure controller (load controller)
• Optional VSD moduleMechanical design
Installation notes
• Ensure that the electrical wiring inside the boiler is in compliance
with national and local safety regulations.
• Do not mix up live and neutral conductors.
• Make certain that strain relief of the connected cables is in com-
pliance with the relevant standards (e.g. as per DIN EN 60730
and DIN EN 60 335).
• Ensure that spliced wires cannot get into contact with neighbor-
ing terminals. Use adequate ferrules.
• Always run high-voltage ignition cables separately while observ-
ing the greatest possible distance to the unit and to other cables
• The burner manufacturer must protect unused AC 230 V termi-
nals with dummy plugs (refer to sections Suppliers of other ac-
cessory items).
• When wiring the unit, ensure that AC 230 V mains voltage ca-
bles are run strictly separate from extra low-voltage cables to
warrant protection against electrical shock hazard.
WARNING
To avoid injury to persons, damage to prop-
erty or the environment, the following warn-
ing notes must be observed!
The LMV51... is a safety device!
Do not open, interfere with or modify the
unit.
The manufacturer will not assume responsi-
bility for any damage resulting from unau-
thorized interference!
Risk of explosion!
Incorrect configuration can lead to excessive
fuel supply which might cause an explosion!
Operators must be aware that incorrect set-
tings made on the AZL5… display and operat-
ing unit and incorrect settings of the fuel and /
or air actuator positions can lead to danger-
ous burner operating conditions.
D9301
Fig. 7
Summary of Contents for RL 300
Page 2: ......
Page 33: ...Appendix Spare parts 31 20035606 GB A Appendix Spare parts ...
Page 38: ...20035606 36 GB Appendix Electrical panel layout ...
Page 39: ...Appendix Electrical panel layout 37 20035606 GB ...
Page 41: ...Appendix Electrical panel layout 39 20035606 GB ...
Page 42: ...20035606 40 GB Appendix Electrical panel layout ...
Page 43: ...Appendix Electrical panel layout 41 20035606 GB 0 1 0 ...
Page 44: ...20035606 42 GB Appendix Electrical panel layout 0 0 0 1 0 2 0 0 0 0 0 0 0 30 3 3 0 0 1 0 ...