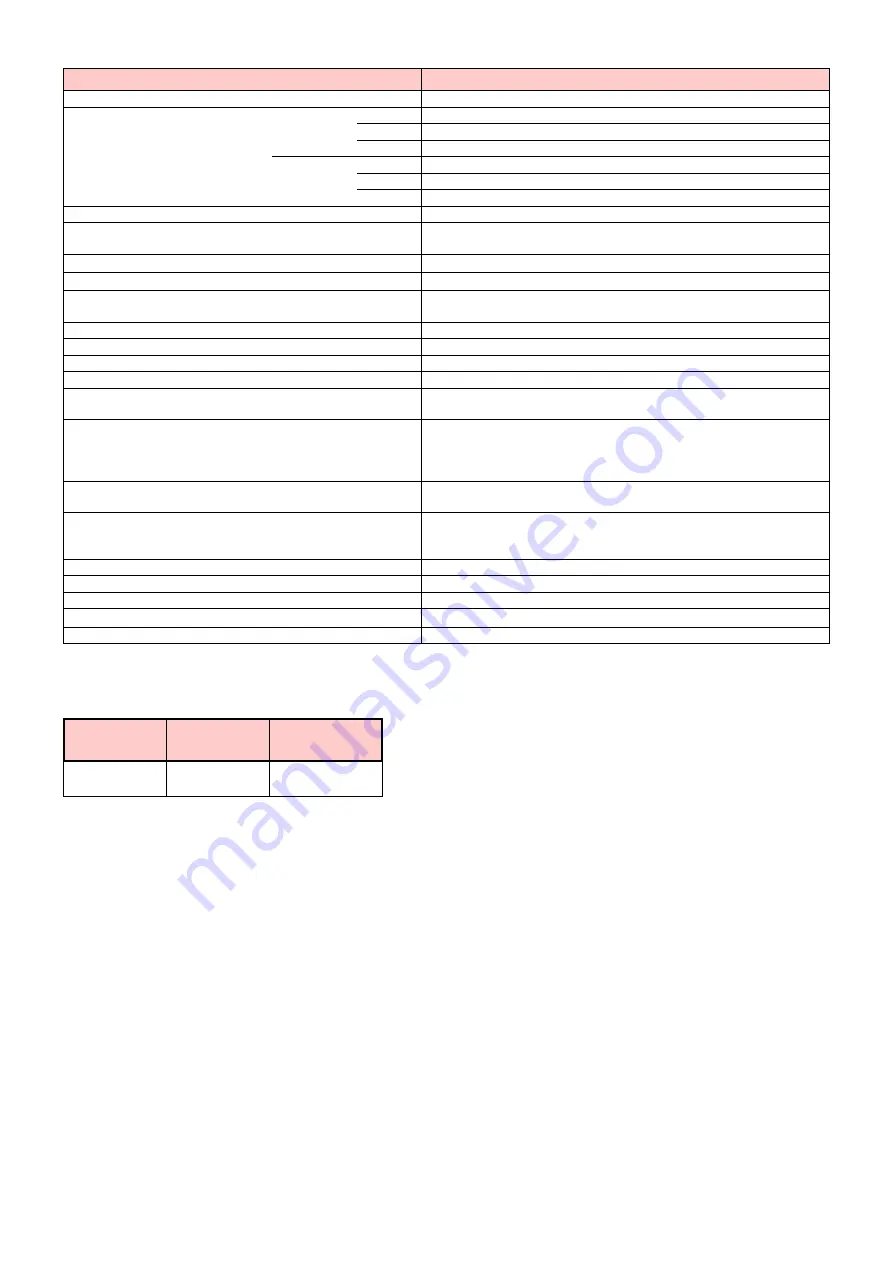
2
TECHNICAL DATA
(1) Reference conditions: Ambient temperature 20°C - Barometric pressure 1000 mbar - Altitude 100 m a.s.l.
(2) Sound pressure measured in manufacturers combustion laboratory, with burner operating on test boiler and at maximum rated output.
VARIANTS
MODEL
RL 64 MZ
TYPE
974 T
OUTPUT
(1)
DELIVERY
(1)
2nd stage
kW
391 - 830
Mcal/h
336 - 714
kg/h
33 - 70
1st stage
kW
206 - 391
Mcal/h
177 - 296
kg/h
17,4 - 33
FUEL
LIGHT OIL
- Net calorific value
kWh/kg
Mcal/kg
11.8
10.2 (10,200 kcal/kg)
- Density
kg/dm
3
0.82 - 0.85
- Viscosity at 20 °C
mm
2
/s max 6 (1.5 °E - 6 cSt)
OPERATION
• Intermittent (min. 1 stop in 24 hours).
• Two-stage (high and low flame) and single-stage (all - nothing).
NOZZLES
number
2
STANDARD APPLICATIONS
Boilers: water, steam, diathermic oil
AMBIENT TEMPERATURE
°C
0 - 40
COMBUSTION AIR TEMPERATURE
°C max
60
ELECTRICAL SUPPLY
V
Hz
230 - 400
with neutral
~ +/-10%
50 - three-phase
ELECTRIC MOTOR
rpm
W
V
A
2800
1500
220/240 - 380/415
4.7 - 2.7
IGNITION TRASFORMER
V1 - V2
I1 - I2
230 V - 2 x 12 kV
0,2 A - 30 mA
PUMP
delivery (at 20 bar)
pressure range
fuel temperature
kg/h
bar
° C max
107
10 - 20
60
ELECTRICAL POWER CONSUMPTION
W max
1400
ELECTRICAL PROTECTION
IP 44
IN CONFORMITY WITH EEC DIRECTIVES
89/336 - 2004/108 - 73/23 - 2006/95 - 92/42 - 2006/42
NOISE LEVELS
(2)
dBA
76
APPROVAL
CE
0036 0382/07
Model
Code
Blast tube
lenght mm
RL 64MZ
3470410
3470411
250
385