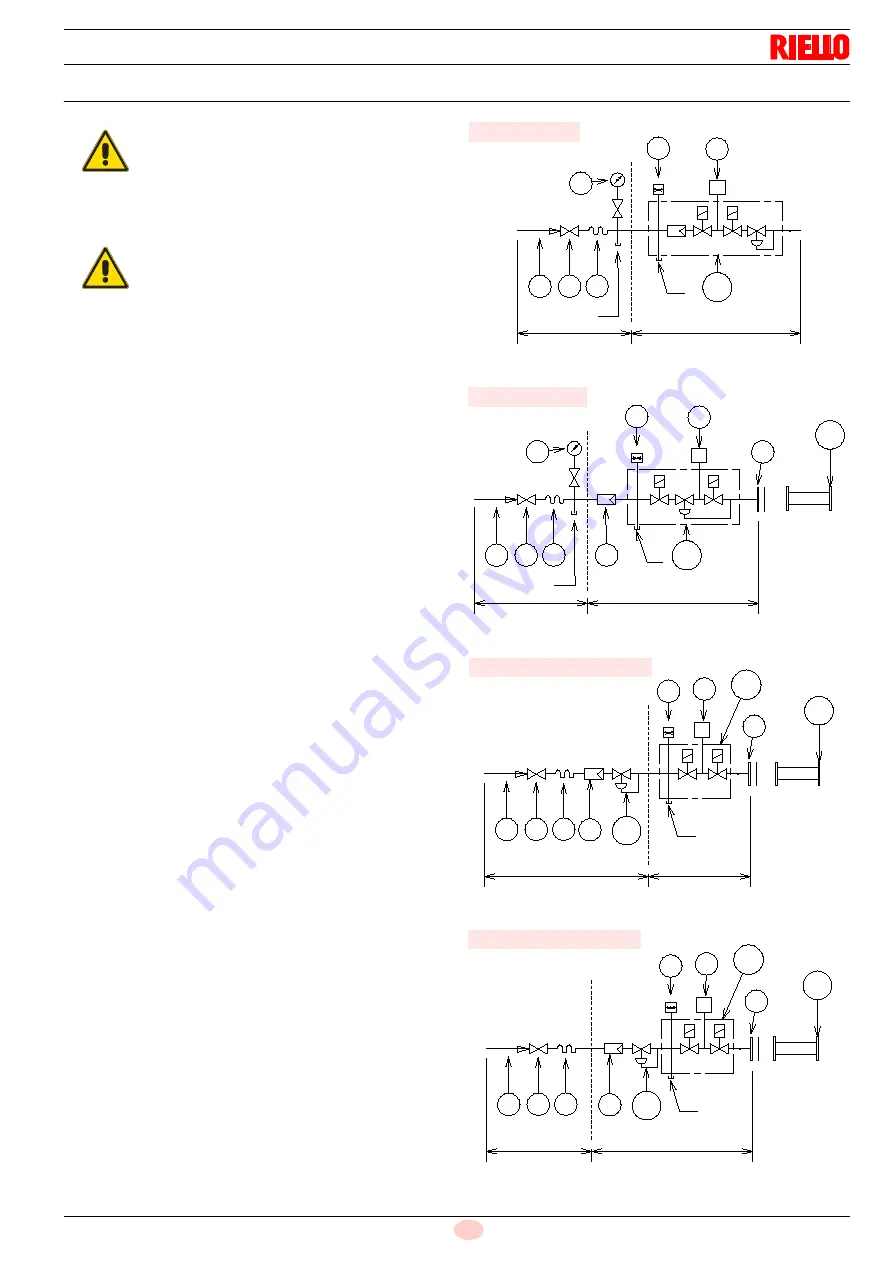
25
20148049
GB
Installation
5.12
Gas supply
5.12.1 Gas feeding line
Key (Fig. 28 - Fig. 29 - Fig. 30 - Fig. 31)
1
Gas input pipe
2
Manual valve
3
Vibration damping joint
4
Pressure gauge with button cock
5
Filter
6A Includes:
– filter
– working valve
– safety valve
– pressure adjuster
6B Includes:
– working valve
– safety valve
– pressure adjuster
6C Includes:
– safety valve
– working valve
6D Includes:
– safety valve
– working valve
7
Minimum gas pressure switch
8
Leak detection control, supplied as an accessory or built-in,
based on the gas train code. In compliance with the EN 676
standard, gas valve leak detection control devices are
compulsory for burners with maximum outputs over 1200
kW.
9
Gasket, for “flanged” versions only
10 Pressure adjuster
11 Train-burner adaptor, supplied separately
P2 Pressure upstream of valves/adjuster
P3 Pressure upstream of the filter
L
Gas train, supplied separately
L1 Responsibility of the installer
DANGER
Explosion danger due to fuel leaks in the
presence of a flammable source.
Precautions: avoid knocking, attrition, sparks and
heat.
Make sure the fuel shut-off valve is closed before
performing any operation on the burner.
ATTENTION
The fuel supply line must be installed by qualified
personnel, in compliance with current standards
and laws.
L1
L
6A
P2
7
4
P3
3
2
1
8
Fig. 28
D11854
MBC “threaded”
L
L1
P2 6B
7
9
8
4
P3
3
2
1
5
11
Fig. 29
D11855
MBC “flanged”
L
L1
5
6C
P2
7
3
2
1
8
10
11
9
Fig. 30
D11856
DMV “flanged or threaded”
L
L1
5
6D
P2
7
3
2
1
8
10
11
9
Fig. 31
D11857
CB “flanged or threaded”