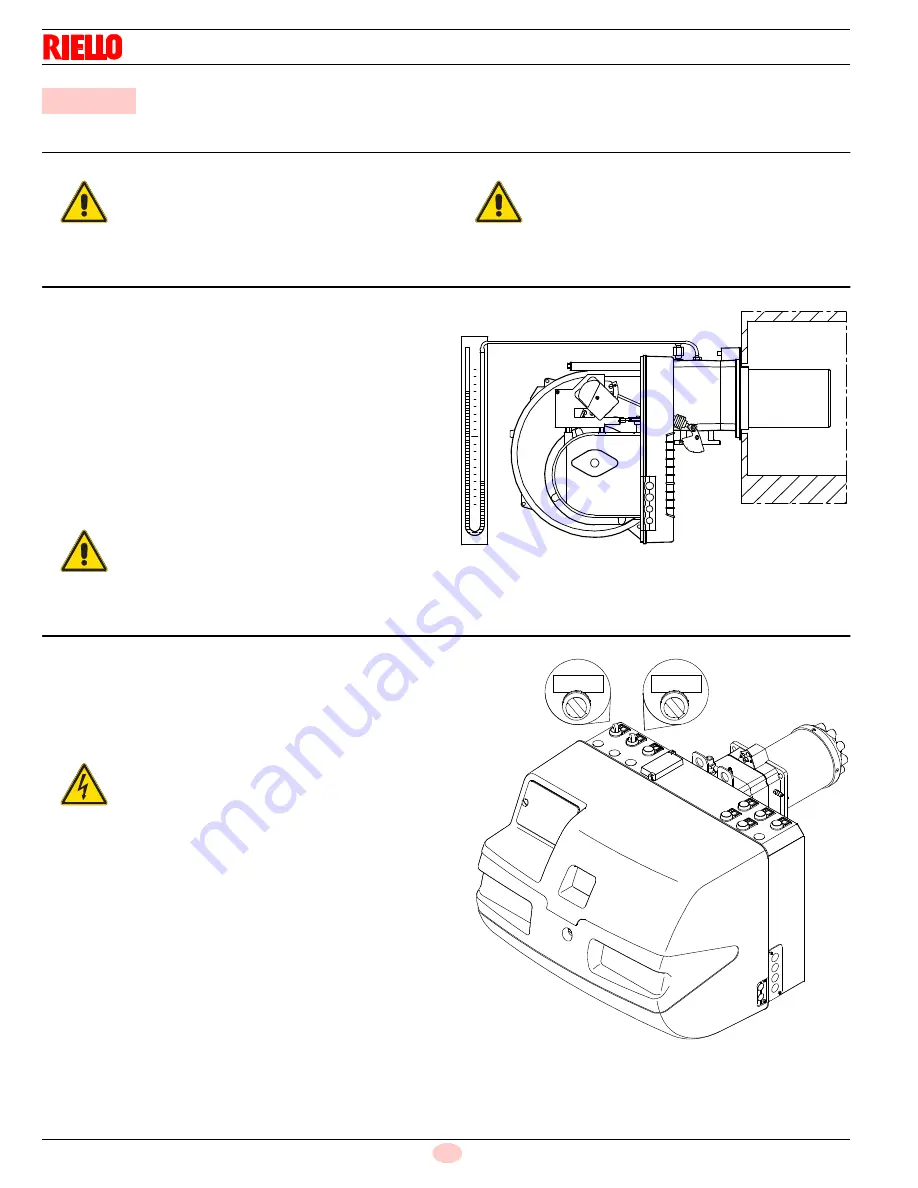
20040407
22
GB
Start-up, calibration and operation of the burner
5.1
Notes on safety for the first start-up
5.2
Operations before start-up
➤
Ensure that the gas supply company has carried out the sup-
ply line vent operations, eliminating air or inert gases from the
piping.
➤
Slowly open the manual valves situated upstream of the gas
train.
➤
Adjust the minimum gas pressure switch (Fig. 29) to the start
of the scale.
➤
Adjust the air pressure switch (Fig. 28) to the start of the scale.
➤
Purge the air from the gas line.
Fit a U-type manometer (Fig. 25) to the gas pressure test point
on the sleeve.
The manometer readings are used to calculate the MAX.
burner power.
5.3
Burner start-up
Feed electricity to the burner via the disconnecting switch on the
boiler panel.
➤
Close the thermostats/pressure switches.
➤
Turn the switch to position “ON” (Fig. 26).
➤
Turn the switch to position “MAN” (Fig. 26) (for manual opera-
tion) or “AUTO” for automatic operation.
NOTE
For further information, please refer to the specific instruction of the
control box.
5
Start-up, calibration and operation of the burner
WARNING
The first start-up of the burner must be carried out
by qualified personnel, as indicated in this manual
and in compliance with the standards and regula-
tions of the laws in force.
WARNING
Check the correct working of the adjustment, com-
mand and safety devices.
WARNING
Before starting up the burner it is good practice to
adjust the gas train so that ignition takes place in
conditions of maximum safety, i.e. with gas delivery
at the minimum.
D2265
Fig. 25
DANGER
Make sure that the lamps or testers connected to
the solenoids, or indicator lights on the solenoids
themselves, show that no voltage is present. If volt-
age is present, stop the burner immediately and
check the electrical wiring.
ON
OFF
AUTO
MAN
Fig. 26
D11905