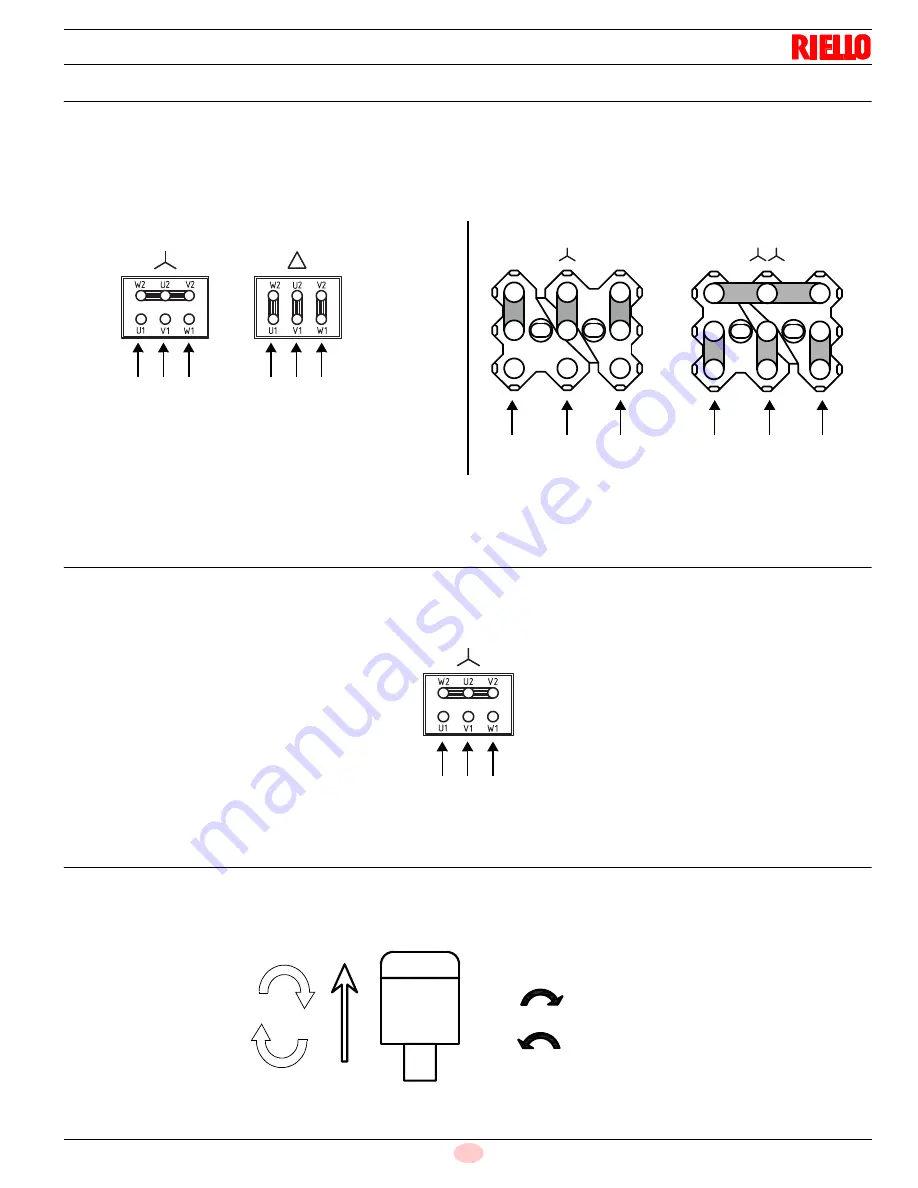
Installation
27
20140257
GB
4.15 Motor connection at 208-230 or 460V
WARNING
:
the motors, manufactured for 208-230/460
IE3/Nema Premium Efficiency
voltage, have a different connection than
IE1
motors, no more
star/delta but
star/double star.
Please, pay attention to the indications in case of modification of voltage, maintenance, or substitution.
4.16 Motor connection at 575V
WARNING
:
the motors, manufactured for 575V
IE3/Nema Premium Efficiency
voltage, have the same control box base of the IE1 motors.
Please pay attention to the indications in case of maintenance or substitution.
4.17 Reversible direction
WARNING
:
If it is necessary to reverse the direction then reverse the two main supply phases.
For example: L1 with L2, there is not difference between
IE1
and
IE3/Nema Premium Efficiency
.
D3686
IE1
IE3/Nema
U2
V2
W2
U3
V3
W3
U1
V1
W1
S8379
U2
V2
W2
U3
V3
W3
U1
V1
W1
S8380
~ ~ ~
~ ~ ~
460V
208-230V
~
~
~
~
~
~
460V
208-230V
Fig. 29
S8382
~ ~ ~
575V
Fig. 30
/ / /
/ / /
VKDIW
S8381
L1
L2
Fig. 31
Summary of Contents for RX 2500 S/E
Page 2: ...Original instructions ...