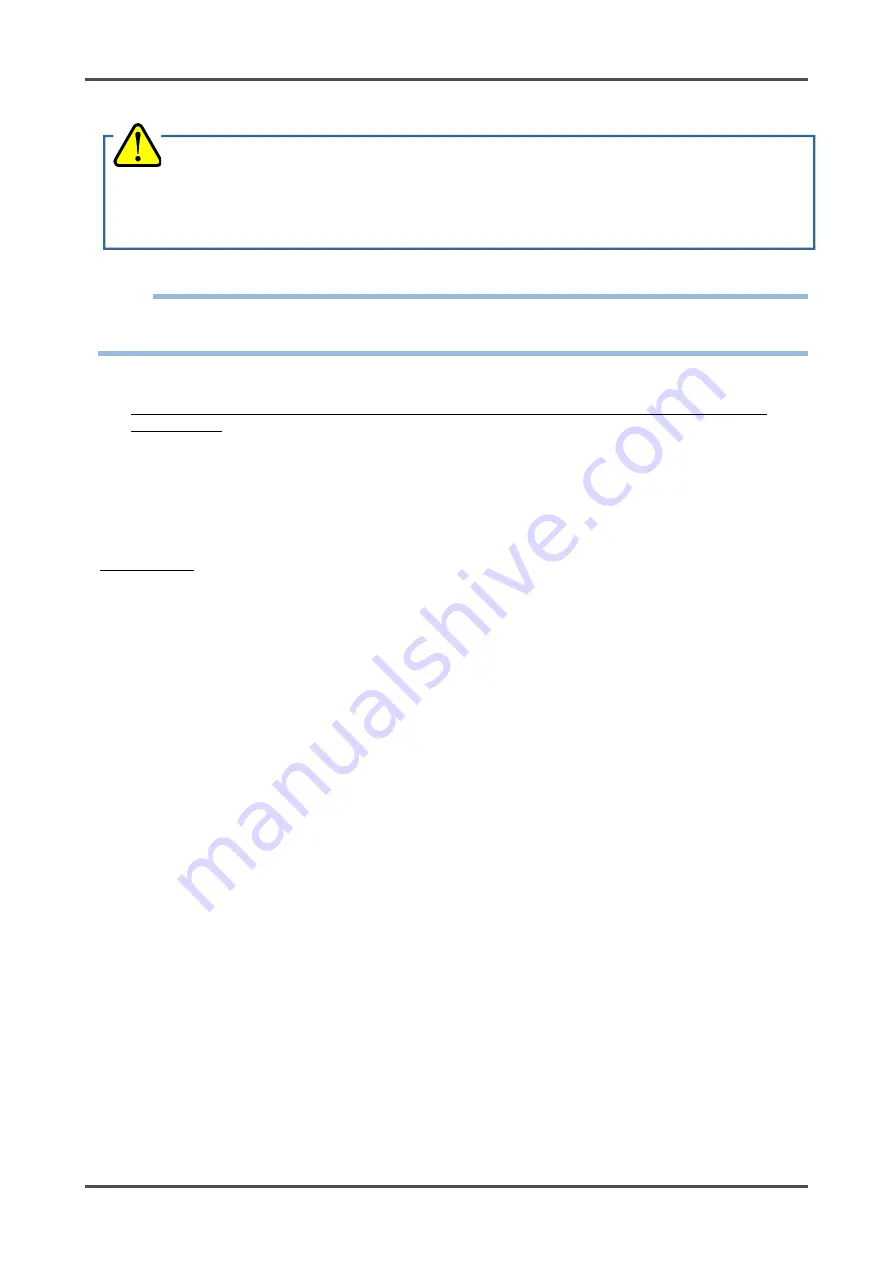
6 Maintenance
6-1. Maintenance intervals and items
- 23 -
NOTE
Before starting alarm test or span adjustment, be sure to provide a notification to the related sections
and block external signals.
<About Maintenance Services>
We provide services on regular maintenance including span adjustment, other adjustments and
maintenance.
To make the calibration gas, dedicated tools, such as a gas cylinder of the specified concentration and
gas sampling bag must be used.
Our service engineers have expertise and knowledge on the dedicated tools used for services, along
with other products. To maintain the safety operation of the detector, please use our maintenance
service.
Typical maintenance services are listed as follows. For more information, please contact RIKEN KEIKI.
Main Services
Power supply
check
*
: Checks the power supply voltage.
Verifies that the power lamp lights up.
Status check
*
: Verifies that the fault lamp does not light up.
Concentration
display check
*
: Verifies that the concentration display value is zero by using the zero gas.
Performs zero adjustment if the reading is incorrect.
Alarm test
*
: Inspects the alarm circuit by using the alarm test function.
Checks the alarm lamp. (Checks ALM activation.)
Checks the external alarm. (Checks the activation of the external alarm, such as a
buzzer.)
Span adjustment
*
: Performs the span adjustment by using the calibration gas.
Gas alarm check
*
: Checks the gas alarm by using the calibration gas.
Checks the alarm. (Checks triggering of alarm when the alarm setpoint is reached.)
Checks the delay time. (Checks time to delay until the alarm is triggered.)
Checks the alarm lamp. (Checks ALM activation.)
Checks the external alarm. (Checks the activation of external alarms, such as a
buzzer and reset signal.)
Cleaning and repair
of the unit
(visual diagnosis)
: Checks dust or damage on the surface, cover or internal parts of the unit, and cleans
or repairs such parts as needed.
Replaces parts which are cracked or damaged.
Unit operation
check
*
: Uses the keys to check the operation of functions and parameters.
Replacement of
consumable parts
: Replaces consumable parts, such as a sensor, filter and pump.
* Check and adjustment are performed at the indicator/alarm unit side.
WARNING
Since this is a safety unit, be sure to perform maintenance at least once every six months to
ensure safety.
Continuing to use the detector without performing maintenance will compromise the sensitivity
of the sensor of the detector head, thus resulting in inaccurate detection.