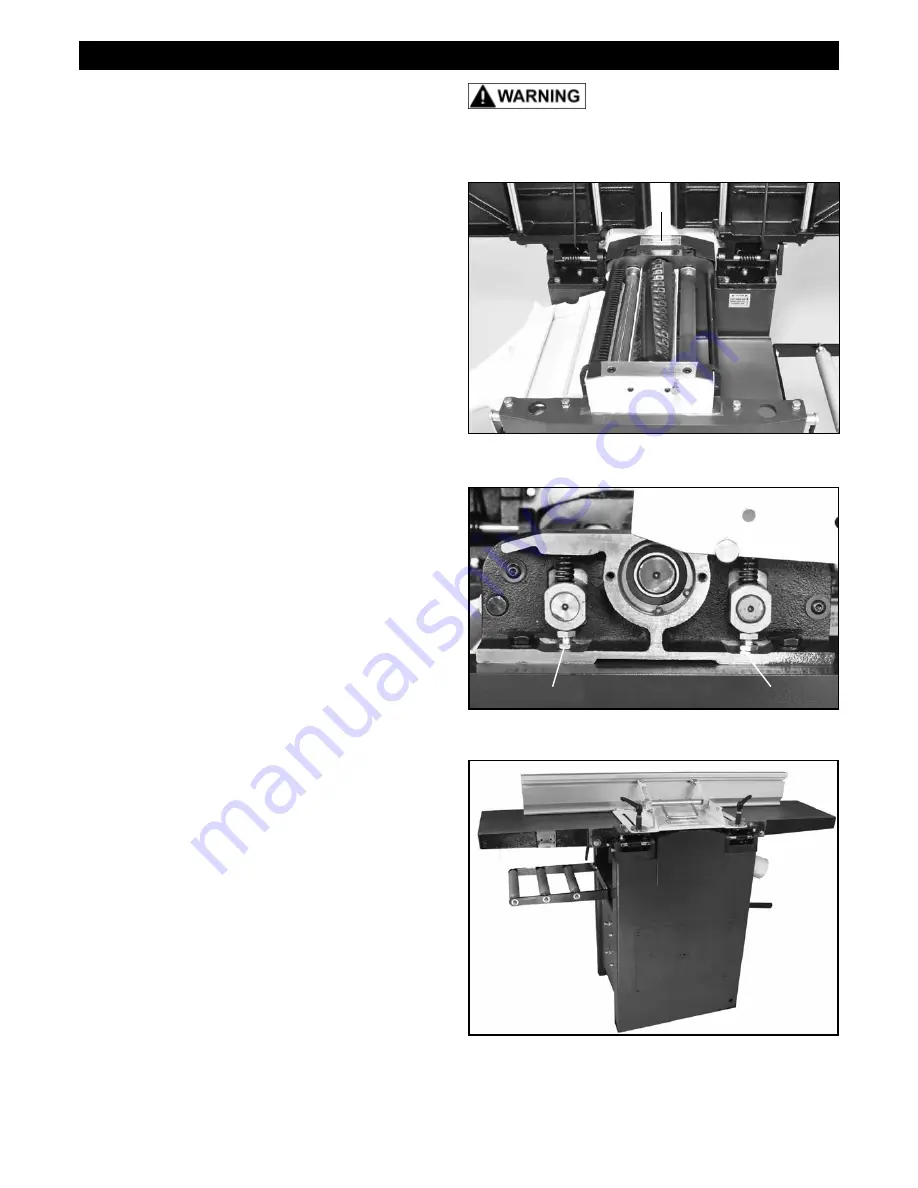
16
ADJUSTMENTS
THE MACHINE MUST NOT BE
PLUGGED IN AND THE POWER SWITCH MUST BE IN
THE OFF POSITION UNTIL ALL ADJUSTMENTS ARE
COMPLETE.
ADJUSTING THE CUTTERHEAD
The Cutterhead that holds the knife inserts is fastened to
the machine's cabinet, and is not adjustable. Based on
the position of this main component of the machine, all of
the other parts - rollers and tables - are then pre-set by
the factory to align with the cutterhead. Should any of the
tables or rollers get out of parallel with the cutterhead, they
can be adjusted separately following the instructions in this
manual.
ADJUSTING THE FEED ROLLERS
The Infeed (#78) and Outfeed (#61) Rollers are pre-set by
the factory to align parallel with the cutterhead and knife
inserts. These spring loaded rollers are set just below the
cutterhead, so that they engage the lumber and move it
through the planer. Should an adjustment be required to
increase or decrease the amount of downward pressure
they exert on the lumber, the following steps are needed.
1. Make sure that the planer/jointer's switch is turned off,
and the plug is disconnected from the power source.
2. The jointer table, with the fence and cutterhead guard,
needs to be lifted up and back into a vertical position. See
page 21, steps 1 & 2, for full details on this process.
3. With the jointer table up, the Front Guard (#53, A) and
Rear Guard (#91, B) must be removed to access the bolts
that will adjust the feed rollers' pressure. FIG. 27.
NOTE:
The Front Guard with the 2 screws (#52) removed,
can be rotated out of the way, leaving the dust collector's
spring-loaded Locating Pin (#51, P) in place. FIG. 28.
The Rear Guard can be removed once the 2 locating
screws are removed, by lowering the jointer table then
removing the fence assembly.
4. Under the Cutterblock Brackets (#57 & 69), the Tight-
ening Screws (#73) hold the compression Springs (#72) in
place on the brass Shaft Sleeves (#59). The bottom Hex
Bolts (#67, FIG. 28, N) can be tightened or loosened with a
wrench to adjust the feed rollers. FIG. 28.
- By raising the hex bolts UP, the spring is compressed
and the downward pressure of its roller is increased upon
the lumber being fed through the planer.
- By lowering the hex bolts DOWN, the spring compres-
sion is reduced, and its rollers exert less pressure down
onto the lumber.
5. Once the rollers are set, secure the Bolts (#67) in place
with the Nuts (#64), re-install the guards, lower the jointer
table with fence & guard, and the machine is ready for use.
FIG. 27
FIG. 28
ADJUSTING DRIVE BELTS
The cutterhead drive belt and the feed gear drive belt need
to be checked periodically and re-tightened if necessary.
Belts will stretch with use, especially when they are new
FIG. 29
Continued on page 17
A
B
N
N
A
B
and are breaking in. Both drive belts are located behind the
machine's rear cover and side panel. FIG. 29, A & B.
P