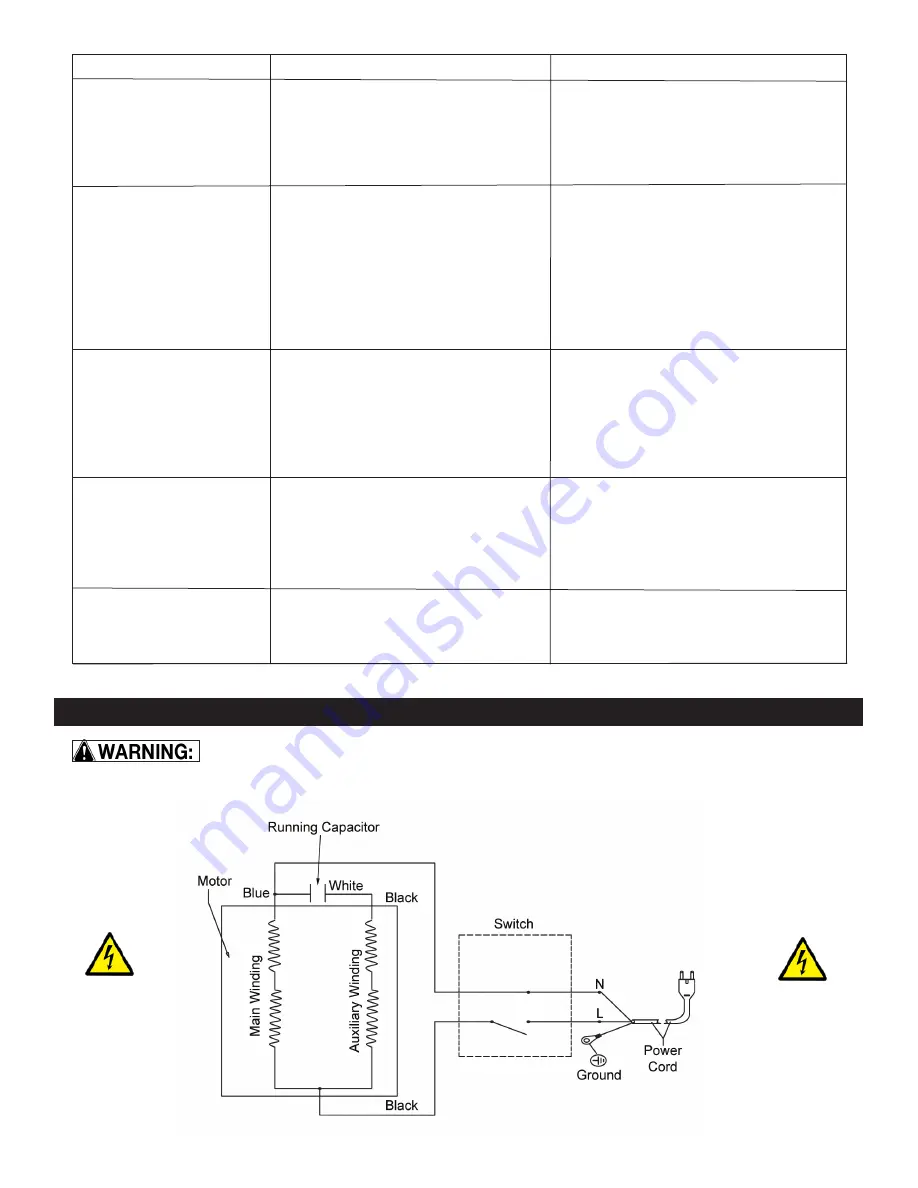
SYMPTOM
PROBABLE CAUSE
CORRECTIVE ACTION
Burn marks on workpiece.
1. Using a sanding grit that is too
fine.
2. Using too much pressure.
3. Work held still for too long
against the sandpaper.
1. Use a coarser-grit sandpaper.
2. Reduce work piece pressure on
the sandpaper while sanding.
3. Do not keep the work piece sand-
ing in one place for too long.
Deep sanding grooves or
scars in work piece.
1. Sanding belt/disc grit is too
coarse for the desired finish.
2. Work piece is being sanded
across the grain.
3. Too much sanding force on the
work piece.
4. Work piece held still against the
belt-disc for too long.
1. Use a finer-grit sanding belt or
disc.
2. Sand with the grain of the wood.
3. Reduce pressure on workpiece
while sanding.
4. Keep work piece moving while
sanding.
Sanding surface clogs
quickly.
1. Too much pressure against the
belt or disc.
2. Sanding softwood or highly
resinous woods.
1. Reduce pressure on work piece
while sanding.
2. Use different stock, sandpa-
per grits, or accept that this will
happen and plan on cleaning or
replacing belts & discs frequently.
Sanding grains easily rub
off the belt or disc.
1. Sandpaper has been stored in
an incorrect environment.
2. Sandpaper has been damaged
or folded.
1. Ensure sandpaper is stored
away from extremely hot & dry
or damp/humid conditions.
2. Store sanding accessories flat –
not bent or folded.
Workpiece lifts up from the
sanding disc-table.
1. Sanding on the “up” , right side
of the disc, where rotation is
up and away from the table.
1. Sand on left side of sanding disc,
where the disc rotates down
towards the table.
WIRING DIAGRAM
This machine must be grounded. Replacement of the power supply cable should only be
done by a qualified electrian. Read the Electrical Safety Information on pages 5 and 6 for further information.
16
Summary of Contents for 50-151
Page 17: ...PARTS EXPLOSION 17...
Page 19: ...WARRANTY 19 WARRANTY...