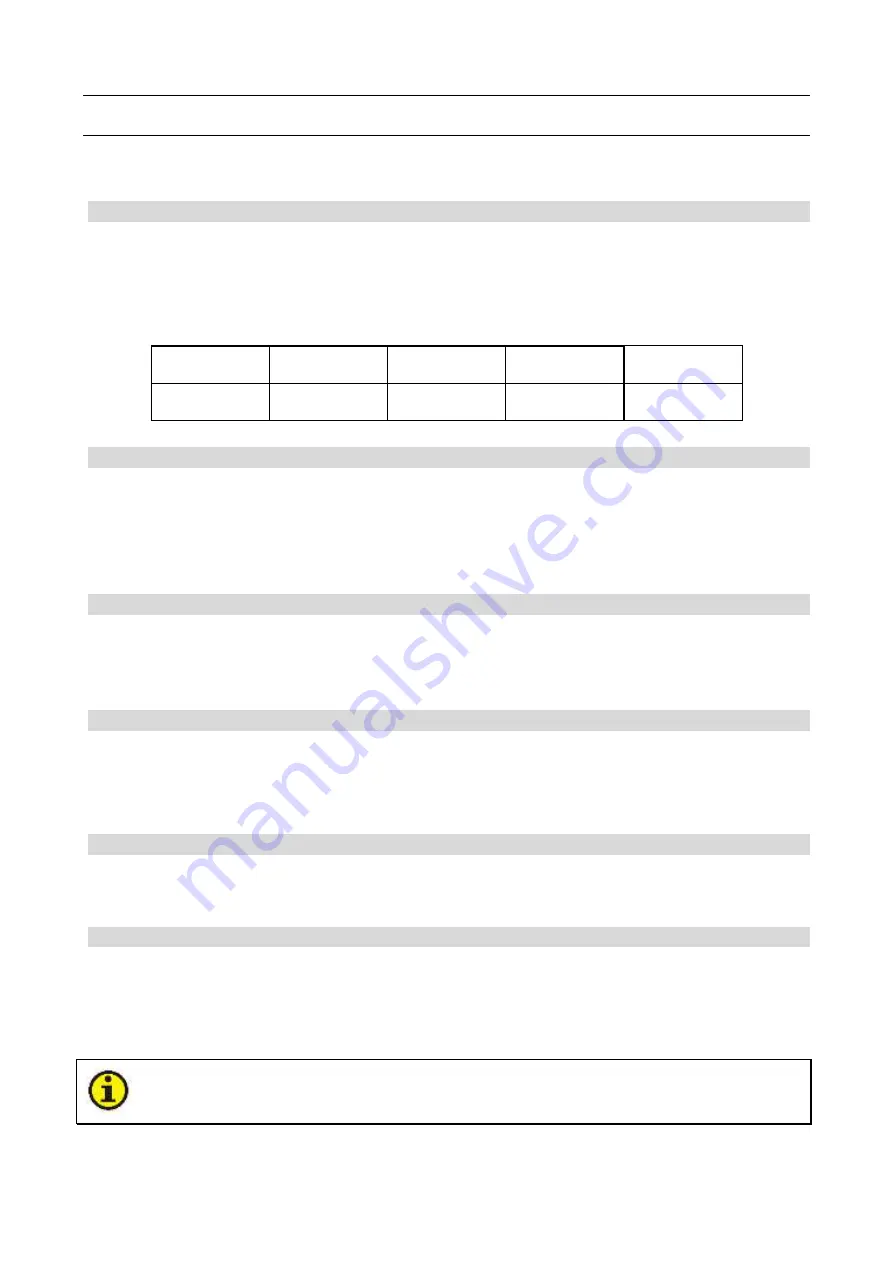
17
QUESTIONS TO BE RUN INTO DURING CUTTING
Fittings, cutting materials, environment factor, supply powers maybe have something to do with cutting.
User must try to improve cutting environment.
A.
Cutting surface is rough, poor cutting result.
The machine may be not well operated. You can check it as follow:
1.
Make sure the compressed air supply has enough pressure which is not less than 0.3MPa
(
3Kg/cm
2
)
,
and its range is±0.05Mpa.
2.
Electrode and nozzle are not matched with current. Check as follow:
Current
10-30A
30-40A
60-100A
100-160A
Nozzle
¢
1.0mm
¢
1.2mm
¢
1.4mm
¢
1.7mm
B.
Arc-striking is difficult and easy to pause.
1.
Make sure quality of tungsten electrode is high.
2.
Cutting current is too small and air flow is too big. And if cooling effect is too strong, it will lead to arc
pause.
3.
Power net voltage is low and input cable is too long.
C.
Output current is not up to the rated value.
When power voltage departs from the rated value, it will make the output current not matched with
rated value; when voltage is lower than rated value, the max output may be also lower than rated
value.
D.
Current is not stabilizing when machine is being operated.
It has something to do with factors as following:
1.
Electric wire net voltage has been changed.
2.
There is harmful interference from electric wire net or other equipment.
E.
Electrode or nozzle burnt often.
1.
Current is too big or nozzle is too small.
2.
Air pressure is low and cooling effect is weak and nozzle is too hot.
F.
Arc can not cut into the steel plate fully, or too much spatter.
1.
Maybe the machine capacity can not meet the demand of that thickness, please use bigger machine.
2.
Electrode or nozzle is burnt, please change it.
For normal operation you should cut from the edge of the work piece, in this way you can
protect the torch from damage by spatter conglutination.