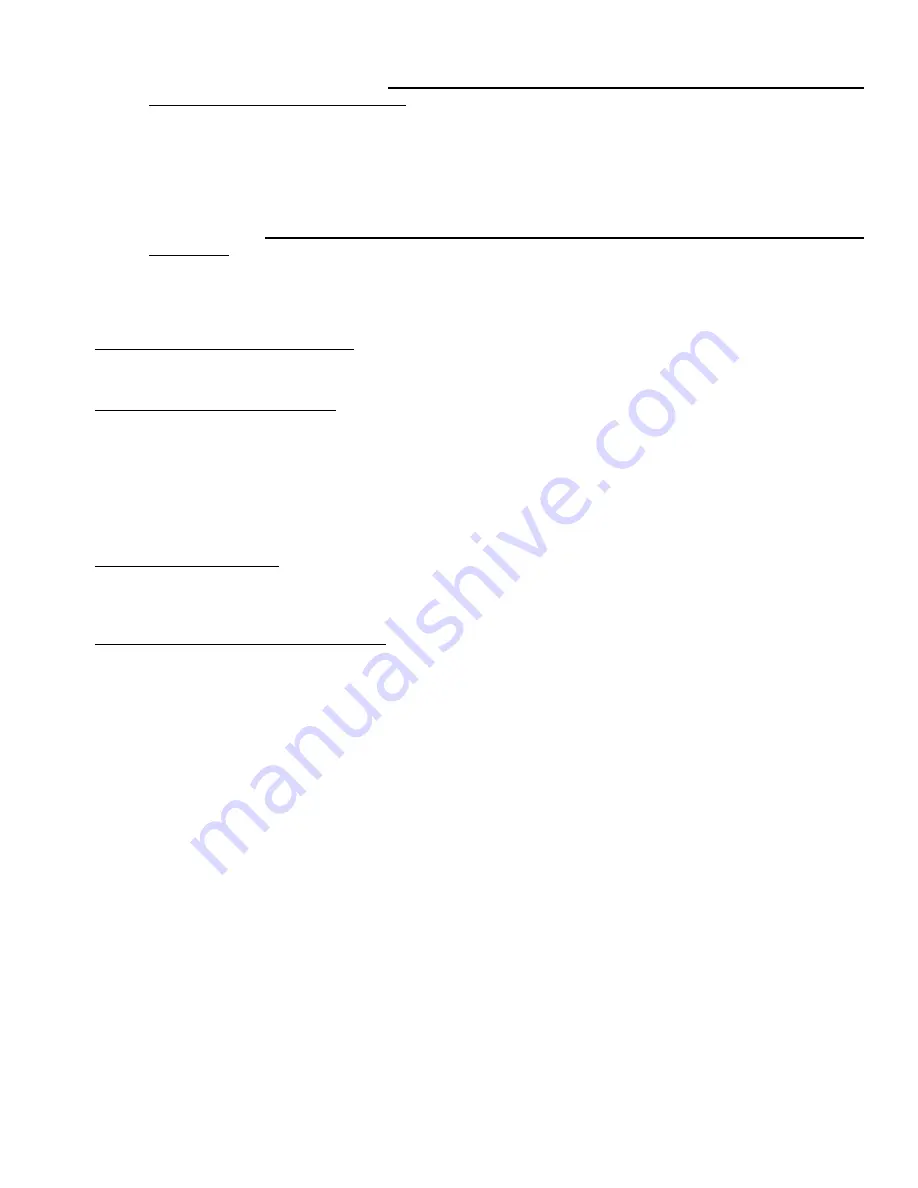
HeatStation™ CONDENSING WATER BOILER
47
34-1161 05/17
Automation System during startup. Remember to reconnect the communication cable to the digital control
display board after startup is complete.
Visually check that all components are intact and no damage has occurred during transit and installation.
Also check to ensure all wire connections within the control cabinet are tight. A loose connection could cause
sporadic shutdowns and malfunctions.
Check to see if terminals
R1
and
R2
are jumped. If they are, nothing more needs to be done. If the terminals
are not jumped but have wires connected to them, this indicates that a remote on/off relay is controlling the
boiler from the Building Automation System. These wires must be removed prior to startup and the terminals
must be jumped. Remember to remove the jumper and reconnect the remote controlling wires after startup
is complete.
Once again, visually check to ensure that all components are intact in this area and that all wire connections
are tight.
Leave the front cover off until the start-up is complete.
CHECK CONNECTIONS FOR LEAKS
Be sure all connections into the tank are tight, as leaks at tank fittings will damage the insulation.
CHECK THE CONDENSATE TRAP
A condensate trap assembly ships with the unit and must be installed on the condensate drain to prevent flue gasses
from escaping and creating a hazardous condition in the installed space. The condensate drain is located at the
bottom rear of the boiler near the flue outlet.
Connect the condensate trap assembly to the CPVC fitting on the condensate drain pipe. Then rotate the trap so that
it contacts the floor. Connect 3/4" ID clear vinyl tubing, rated for 170 degrees or higher, or an optional Condensate
Neutralization System to the barbed hose connection at the end of the condensate trap.
CONFIRM THE GAS TYPE
Heatstation Boiler will require
Natural
gas. If the available gas type is not correct, contact Rverside Hydronics for
instructions.
CONFIRM THE SUPPLY GAS PRESSURE
WARNING: If you smell gas: Do not try to light any appliance. Do not try to touch any electrical switch or use
a phone in your building. Immediately call your gas supplier and follow their instructions.
For
Natural Gas
, the maximum inlet static gas pressure must not exceed
14.0
inches water column and must not
drop below
3.5
inches water column during operation.
To check the supply gas pressure:
1. First, shut off the main gas supply to the boiler.
2. Remove the cover plate at the top of the boiler to access the burner and gas train components.
3. Ensure that both the manual gas valve at the burner, and the manual gas valve at the inlet of the gas train is
closed.
4.
Attach a 1/8” NPT pilot shutoff test valve and tube to the test port on the manual shutoff gas valve at the inlet of
the gas train. Attach a second 1/8” NPT pilot shutoff test valve and tube to the manual shutoff gas valve
downstream of the gas train at the burner. Close both test valves.
5. Attach U-tube manometers or gas pressure gauges to both of the pilot shutoff test valves.
6. Open the main gas supply to the boiler and check for gas leaks on all joints upstream of the manual shutoff gas
valve at the inlet of the gas train.
7.
Now open the 1/8” pilot shut-off test valve at the inlet of the gas train and measure the supply gas pressure.
IMPORTANT:
If the supply gas pressure is outside of the allowable range, notify the building maintenance
personnel or installer to reduce the gas pressure to the boiler!
8. Now open the manual gas shut off valve, at the inlet of the gas train, and check the gas train for leaks using a
soap solution. If any bubbles are detected, close the manual gas valve, tighten the leaking connection, then open
the manual gas shutoff valve again and check for leaks.
9.
Now open the 1/8” pilot shut-off test valve connected to the manual shutoff gas valve, downstream of the gas
train closest to the burner, and note the gas pressure measured by the monometer. Check the gas pressure again