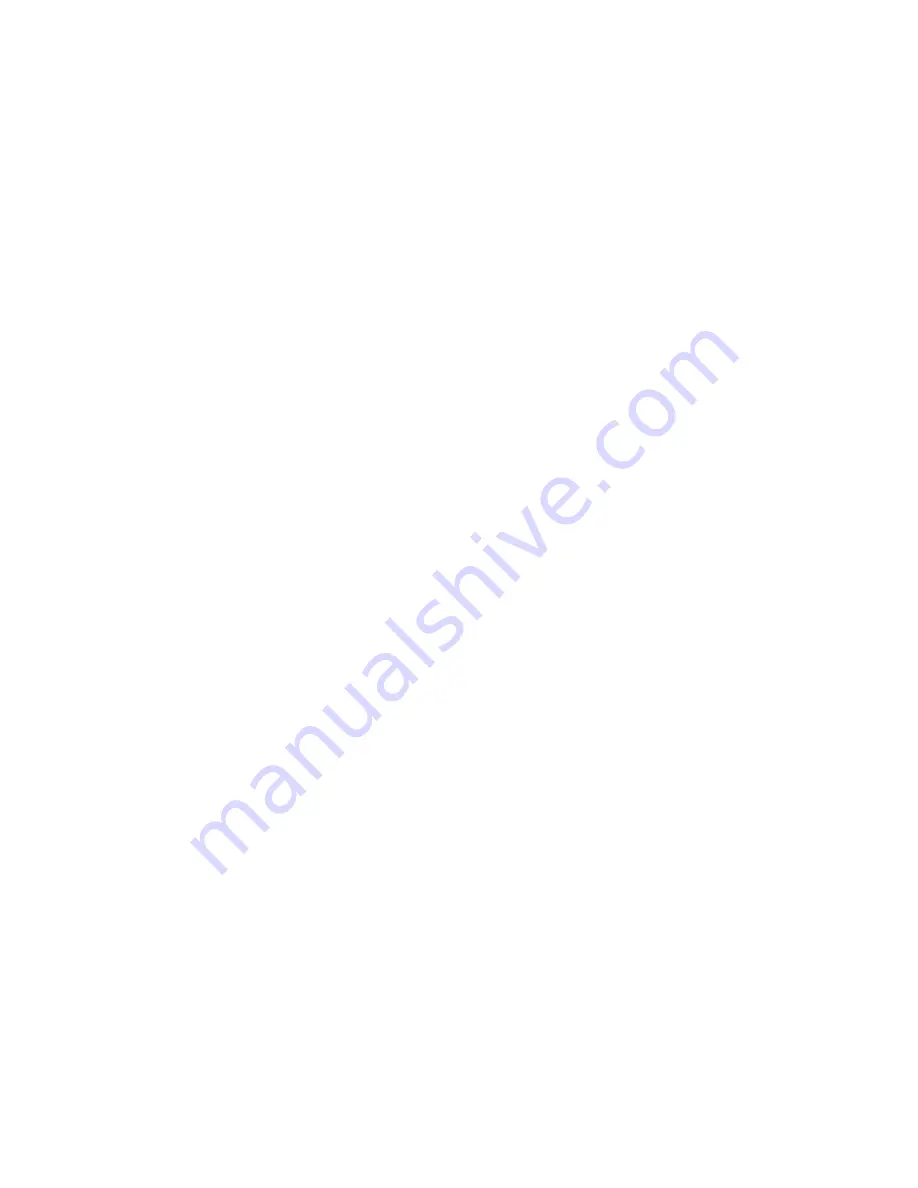
HeatStation™ CONDENSING WATER BOILER
58
34-1161 05/17
17
PERIODIC MAINTENANCE
Listed below are items that must be checked to ensure reliable operations. Maintenance must be performed by a
qualified service or maintenance provider. To ensure proper maintenance, the following instructions should be posted
near the appliance and maintained in legible condition. Verify proper operation after servicing.
WARNING: When servicing the controls, use exact, Factory authorized, replacement parts and label all wires
prior to disconnection. Verify proper operation after servicing. Incorrect parts substitution and wiring errors
can cause damage, improper operation, fire, carbon monoxide, exposure to toxic fumes or other unexpected
and unsafe conditions that can result in fire, personal injury or death.
1. Examine the appliance and venting system at least once a year. Check more often in first year to determine
inspection interval.
a. Check all joints and pipe connections for tightness, corrosion or deterioration.
b. Check the electronic-ignition system for quick ignition and a proper flame signal.
c. Check all safety controls including thermostats for proper operation.
d. Check safety shut-off valves for operation and tightness.
e. Have the entire system, including, but not limited to, the burner, heat exchanger and venting system,
periodically inspected by a qualified service agency.
2. Exposure to Dusty or Dirty Combustion Air: An appliance installed in a dust or dirt contaminated atmosphere will
require more frequent inspection and cleaning of the burner to prevent nuisance shutdowns or premature burner
failure.
3. Any sign of soot on the heat exchanger or in the flue indicates the need for a combustion inspection. Properly
installed and adjusted units seldom need heat exchanger cleaning. If soot has formed, the most common causes
are restricted combustion air or excessive gas. A blocked heat exchanger can cause unsafe operation and will
reduce efficiency. To inspect and clean the heat exchanger, a qualified service agent or installer should use the
procedures described in items 4, 5 & 6 below.
4. All gaskets on disassembled components must be replaced on reassembly with exact, Factory Authorized,
replacement parts only. Gasket kits are available from your Riverside Hydronics Representative or by contacting
Riverside Hydronics.
5. Burner and/or Heat Exchanger Inspection and Cleaning Procedure:
a. Turn off main power to unit.
b. Turn off gas supply.
c. Write notes and/or take pictures during this process to aid in correct reassembly.
d. Disconnect electrical components by disconnecting the wires going to terminal strip in the bottom junction
box and the respective conduit connections on the bottom of the control enclosure. If a wiring diagram is not
attached to the back of the enclosure door or otherwise provided with the boiler, make careful notes of the
locations for all the wires.
e. Remove the metal jacket panels, as needed, by disconnecting the fasteners holding it to the structural frame
and other panels.
f.
Remove the hot surface igniter, (HSI) from the burner. Be very careful not to bump the igniter element due to
the fragility of the igniter.
g. Break the unions that connect the gas train to the blower and the gas supply pipe. Remove the gas train.
h. Remove the nuts that secure the burner transition to the combustion chamber and pull the blower/burner
assembly out until it is completely extracted from boiler.
i.
Inspect refractory for damage. The refractory must provide a tight seal against the top edge of the burner
deck. Be careful not to damage the refractory when removing the burner. With the burner removed, inspect
the deck surface of the burner for lint or other blockage carried in the fuel air stream. If blockage has
accumulated, use brush to loosen debris and use a vacuum or water to remove it from the burner cavities.
j.
Inspect the burner surface for signs of cracking or thermal fatigue.