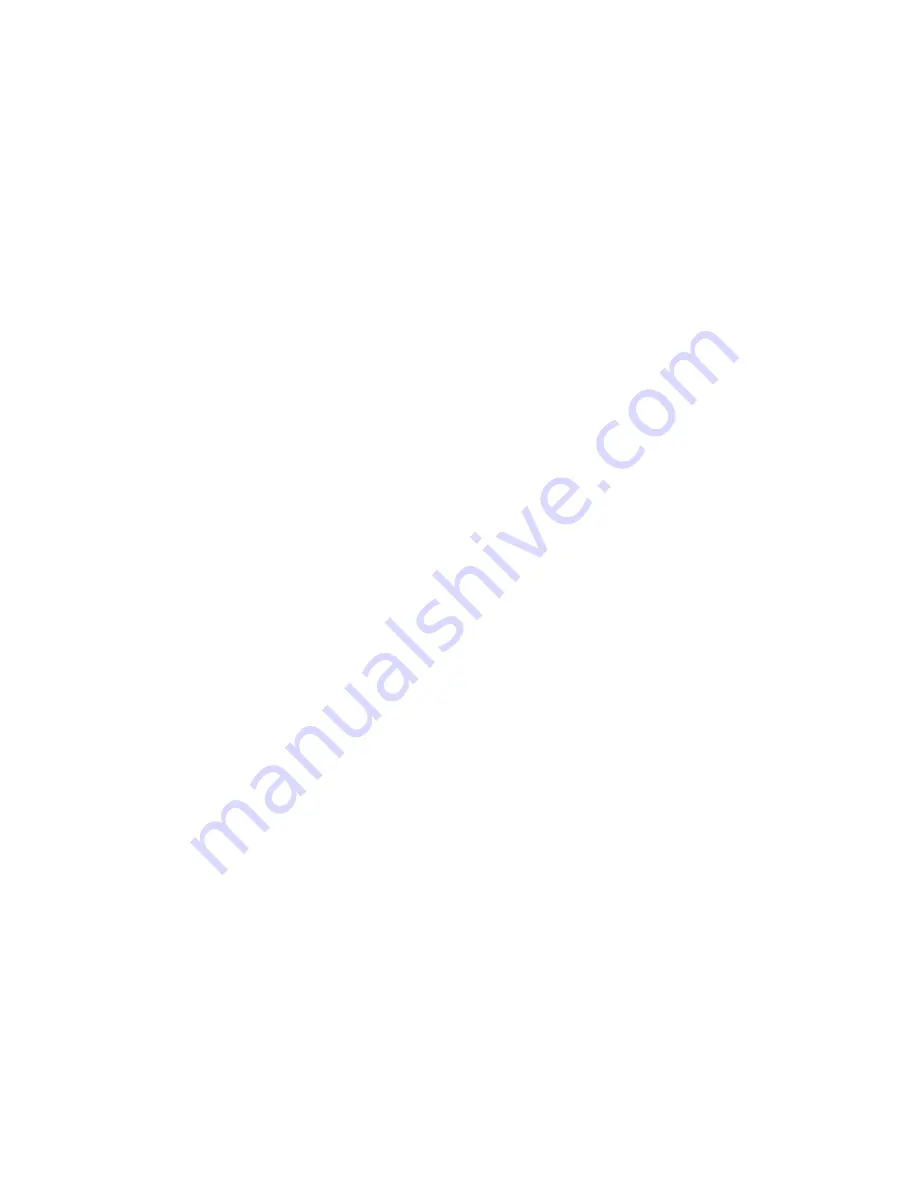
MAN-2V3B-4.1V REV (E)
26
j.
Reinstall the guide cylinder assembly over the guide piston.
k.
Reinstall the compression cylinder assemblies per instructions.
l.
Install distance piece covers and fill crankcase with new oil.
7.12
MAIN BEARINGS:
The crankshaft is supported in the crankcase by two main bearings.
They are a tapered roller design, consisting of an inner race, outer race and rollers. Lubrication is
supplied by the crankcase oil splash. There is no scheduled maintenance for the main bearings.
REMOVE MAIN BEARINGS
.
a.
The compressor must be completely disassembled. See applicable instructions.
b.
Remove the flywheel and bushing by removing the three cap screws that secure the
flywheel and bushing to the crankshaft. Use these screws in the bushing tapped holes to
jack the flywheel and bushing apart. This will "unlock" the bushing from the crankshaft.
c.
Remove the bearing support cover and connecting rods. NOTE: There are notches in the
bearing support cover gasket so that the gasket is not damaged during disassembly.
d.
Pull the crankshaft forward and remove it from the crankcase.
e.
With a suitable puller, remove the bearings from each end of the crankshaft.
INSTALL MAIN BEARINGS
.
a.
Thoroughly clean the crankcase,
crankshaft and bearing cover.
b.
Press a new bearing on each end of the crankshaft main bearing journals.
Preheating the
bearings to 250˚F will facilitate installation.
c.
Install a new shaft seal in the crankcase.
d.
Install the crankshaft with bearings into the crankcase.
e.
Install the bearing plate with a new gasket.
Tighten the bearing plate cap screws to 30
ft-lbs. torque.
f.
Install the connecting rods and guide cylinders. Rotate by hand insure all turns freely.
Fill the crankcase to the proper level with proper oil.
g.
Install the flywheel, hub and key, drive V-belts and beltguard in the reverse procedure of
removal. Insure that the flywheel and driver sheave are lined up. Align V-belts and
pulleys.
h.
Replace compression cylinder assemblies per instructions using special tool for piston
rod attachment.
j.
Connect all other equipment in reverse order of disassembly.
l.
Turn the flywheel by hand a few revolutions to be certain everything is clear before
starting the compressor.
m.
Start the compressor and check for gas or oil leaks. If leakage is present, repair as
required.
Summary of Contents for RIX 2V3B-4.1V Series
Page 54: ......
Page 55: ......
Page 56: ......
Page 57: ......
Page 58: ......
Page 59: ......
Page 60: ......
Page 61: ......
Page 62: ......
Page 66: ......
Page 67: ......
Page 68: ......
Page 70: ...P N 515 910 P N 515 911 P N 515 792 P N 515 829 X515 910 X515 911 X515 792 X515 829...
Page 71: ......
Page 72: ......
Page 73: ...P N 76 713 X76 713...
Page 74: ......
Page 75: ......
Page 76: ......
Page 77: ......
Page 78: ......
Page 79: ......